DFM 101: PCB Via Structures
November 2, 2021 | Anaya Vardya, American Standard CircuitsEstimated reading time: 3 minutes
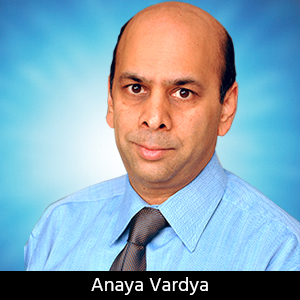
One of the biggest challenges facing PCB designers is not understanding the cost drivers in the PCB manufacturing process. This article is the latest in a series that will discuss these cost drivers (from the PCB manufacturer’s perspective) and the design decisions that will impact product reliability.
DFM
Design for manufacturing (DFM) is defined as the practice of designing printed circuit boards that meet not only the capabilities of the customer’s assembly manufacturing process, but also the capabilities of the board fabrication process at the lowest possible cost. While not a substitute for early design engagement with the PCB fabricator, these articles will provide guidelines that will help to “design for success.”
Microvias
One of the most important technological advancements that made HDI viable was development of the microvia: a very small hole (typically 0.006” or smaller) that only connects certain layers either as “blind” or “buried” via holes. This represents a totally new way of making electrical connections between layers on a PCB. Traditional PCB technology has utilized “through-holes,” which by definition, are drilled through the entire PCB connecting the two outside layers with all of the internal layers. The ability to strategically connect only certain pads on certain layers greatly reduces the real estate needed for a PCB design and allows a much greater density in a smaller footprint. Figure 1 shows through-holes and buried and blind vias.
Figure 1: Microvias vs. through-hole vias. (Image credit: NCAB Group)
Types of Microvias
- Blind via: Used to connect one surface layer with at least one internal layer
- Buried via: Used to create connections of internal layers with no contact to the surface layers
- Via-in-pad: A type of blind via in which the via hole is drilled in a surface mount pad, eliminating the need to run a trace and via pad from each SMT pad
- Filled vias: Completely filling the microvia with either a non-conductive or conductive paste. Conductive fill is typically used for heat dissipation and non-conductive fill is used to closely match the thermal expansion of the substrate.
Microvia Formation
Microvias can be formed through a number of methods, primarily mechanical drilling, laser drilling and sequential lamination.
- Mechanical drilling: Uses traditional drilling equipment to mechanically form holes, but typically limited to 0.006” diameter and dependent on the depth needed
- Laser drilling: Special drilling equipment that utilizes a laser to form the hole and can go down to 0.001” in diameter
- Sequential lamination: A process where the microvias are drilled all the way through a sub-panel of the layers that need to be connected by the via, which could require multiple lamination, plating, filling and planarization operations (Figure 2).
Figure 2: Sequential lamination. (Source: Siemens EDA)
Stacked vs. Staggered Microvias
- Stacked: Microvias that are electrically connected and literally stacked vertically on top of each other through various layers of the PCB
- Staggered: Microvias that are electrically connected and offset to one another through various layers of the PCB (Figure 3)
Figure 3: Staggered and stacked microvias.
Via-in-Pad Microvias
The via-in-pad production process allows you to place vias in the surface of the flat lands on your PCB by plating the via, filling it with one of the various fill types, capping it and, finally, plating over it. Via-in-pad is typically a 10- to 12-step process that requires specialized equipment and skilled technicians. Via-in-pad is often an optimum choice for HDI PCBs because it can simplify thermal management, reduce space requirements, and provide one of the shortest ways to bypass capacitors for high-frequency designs (Figure 4).
Figure 4: Via-in-pad.
Understanding the cost drivers in PCB fabrication and early engagement between the designer and the fabricator are crucial elements that lead to cost-effective design success. Following your fabricator’s DFM guidelines is the first place to start.
This article originally appeared in the October 2021 issue of Design007 Magazine.
Anaya Vardya is president and CEO of American Standard Circuits; co-author of The Printed Circuit Designer’s Guide to…Fundamentals of RF/Microwave PCBs and Flex and Rigid-Flex Fundamentals; and author of Thermal Management: A Fabricator's Perspective. Visit I-007eBooks.com to download these and other?free, educational titles. He also co-authored “Fundamentals of Printed Circuit Board Technologies,” and is an I-Connect007 columnist. To read past columns, or contact Vardya, click here.
Testimonial
"Advertising in PCB007 Magazine has been a great way to showcase our bare board testers to the right audience. The I-Connect007 team makes the process smooth and professional. We’re proud to be featured in such a trusted publication."
Klaus Koziol - atgSuggested Items
The Death of the Microsection
06/26/2025 | Bob Neves, Reliability Assessment Solutions, Inc.I got my start out of college grinding and polishing PCB microsections. My thumbs are a bit arthritic today because of the experience (microsection grinders know what I mean). Back then, via structures were rather large, and getting to the center in six steps of grinding and polishing was easy compared to what my team has been doing recently at the lab.
Day 2: More Cutting-edge Insights at the EIPC Summer Conference
06/18/2025 | Pete Starkey, I-Connect007The European Institute for the PCB Community (EIPC) summer conference took place this year in Edinburgh, Scotland, June 3-4. This is the third of three articles on the conference. The other two cover Day 1’s sessions and the opening keynote speech. Below is a recap of the second day’s sessions.
American Standard Circuits to Exhibit at IMS 2025
06/12/2025 | American Standard CircuitsAnaya Vardya, President and CEO of American Standard Circuits & ASC Sunstone Circuits, announced that his companies will exhibit at the IEEE International Microwave Symposium (IMS 2025), taking place June 15-20, 2025, at San Francisco’s Moscone Center.
UHDI Fundamentals: UHDI Drives Unique IoT Innovation—Smart Homes
06/03/2025 | Anaya Vardya, American Standard CircuitsThe combination of UHDI's high-bandwidth capabilities and IoT's real-time data processing can lead to more efficient, immersive, and smarter IoT systems. This convergence of two revolutionary technologies is enabling quantum advancements in some very “unconventional” applications.
Choosing the Right Strategic Path
04/29/2025 | Marcy LaRont, PCB007 MagazineTom Yang, CEO of CEE PCB, discusses the current economic challenges, noting reduced purchasing power post-pandemic. He highlights the growing demand for HDI in consumer electronics due to AI growth. Tom also expresses concerns about tariffs under the new U.S. administration, prompting CEE to diversify production locations, including new plants in Southeast Asia. He emphasizes the need for PCB manufacturers to adapt strategically amidst rising costs and fierce competition, particularly for mid-sized shops facing unique challenges in the industry.