-
- News
- Books
Featured Books
- design007 Magazine
Latest Issues
Current IssueProper Floor Planning
Floor planning decisions can make or break performance, manufacturability, and timelines. This month’s contributors weigh in with their best practices for proper floor planning and specific strategies to get it right.
Showing Some Constraint
A strong design constraint strategy carefully balances a wide range of electrical and manufacturing trade-offs. This month, we explore the key requirements, common challenges, and best practices behind building an effective constraint strategy.
All About That Route
Most designers favor manual routing, but today's interactive autorouters may be changing designers' minds by allowing users more direct control. In this issue, our expert contributors discuss a variety of manual and autorouting strategies.
- Articles
- Columns
- Links
- Media kit
||| MENU - design007 Magazine
IPC-2581: An Open, Neutral, Efficient Data Transfer Format
November 8, 2021 | Hemant Shah, IPC-2581 Consortium, and Patrick Davis, Cadence Design SystemsEstimated reading time: 3 minutes
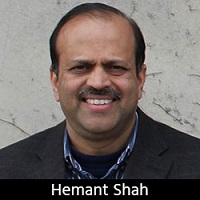
Introduction
PCB design and manufacture has become exponentially more complex as modern electronics providers strive to meet consumer demand for greater connectivity and performance. In the current process, two major pain points need to be overcome to achieve an efficient design and manufacturing process that results in first-time-right products that go to market quickly.
The first pain point is time to manufacture—the flow from end of design to start of manufacturing is dependent on multiple communications and shared files between the design house and the manufacturing partner. The industry-standard Gerber file format-based package contains a set of files with data in different formats, along with documentation/notes/instructions, forcing the manufacturer to go back and forth with the design house customer to ensure that their interpretation is correct. An additional problem is that the data in Gerber files doesn’t match what is in the netlist or in the instructions, leaving the manufacturer to determine which one is correct. This back and forth is done in written form so that the manufacturer can document what the overriding instructions are.
The second pain point is the design for manufacturing (DFM) analysis that all manufacturers run on the data to see if the design violates any of their manufacturing rules/guidelines. They can bend the rules to some extent in some instances, but if there are many violations, the customer must be told that either the design cannot be manufactured, or if manufactured, the yield will not be high, and therefore the cost to the customer will be high. The feedback from DFM analysis tools from the manufacturer is in electronic paper, such as Excel spreadsheets, HTML code, PowerPoint slides, Word documents, and email. This electronic paper is then read and interpreted by the design engineer/PCB designer and correlated into elements in the design. The DFM feedback and this second round of back-and-forth communication is a time-consuming and error-prone manual process in which both sides must keep track/document what they discussed, what was overridden, and what was decided.
This article examines the various PCB manufacturing handoff formats, such as Gerber, ODB++, and IPC-2581, and highlights why IPC-2581, the only standard that solves both the design-to-manufacturing handoff and the DFM issues, is becoming widely adopted.
Design-to-Manufacturing Handoff Challenges
There has been much debate in the PCB industry recently about the need for more modern, automated file formats for sending board designs to fabricators. The popular Gerber-based package, invented in the 1980s, is still the backbone of the industry because it is familiar and workarounds for its shortcomings, such as EDA library “hacking,” have been devised in-house to produce Gerber-based handoff packages.
For engineers, the problem with using Gerber-based packages is that there is no efficient way for the design house to receive feedback from the manufacturing partner. At every stage that the data is handled by the manufacturing partner, feedback is sent via electronic paper, and because the feedback is shared in multiple pieces, those on the manufacturing side must reverse-engineer the design, hope they make the right decisions, and spend additional time asking questions to verify the accuracy of the data. It is time consuming and risky for design divisions to produce and manufacturing divisions to consume, because so many files are being produced that it is difficult to ensure they are all in sync when changes are made. There are too many formats, the data is split into too many incoherent pieces that are not easy to digitalize, and it isn’t possible to do smart processing. If an error is made during handoff, the design house is responsible for the cost, and, conversely, if an error is made during manufacture, the manufacturer is responsible for the cost.
To read this entire article, which appeared in the October 2021 issue of Design007 Magazine, click here.