-
- News
- Books
Featured Books
- design007 Magazine
Latest Issues
Current IssueAll About That Route
Most designers favor manual routing, but today's interactive autorouters may be changing designers' minds by allowing users more direct control. In this issue, our expert contributors discuss a variety of manual and autorouting strategies.
Creating the Ideal Data Package
Why is it so difficult to create the ideal data package? Many of these simple errors can be alleviated by paying attention to detail—and knowing what issues to look out for. So, this month, our experts weigh in on the best practices for creating the ideal design data package for your design.
Designing Through the Noise
Our experts discuss the constantly evolving world of RF design, including the many tradeoffs, material considerations, and design tips and techniques that designers and design engineers need to know to succeed in this high-frequency realm.
- Articles
- Columns
- Links
- Media kit
||| MENU - design007 Magazine
A PCB Design Data Management Overview
November 15, 2021 | I-Connect007 Editorial TeamEstimated reading time: 4 minutes
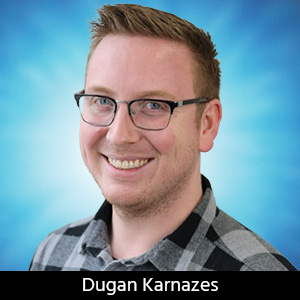
In recent issues of Design007 Magazine, we’ve covered strategies for managing specific types of data. But in this issue, we’re looking into data management techniques from a company level.
The I-Connect007 Editorial Team recently spoke with three PCB designers who have quite a bit to say about PCB data management: Altium’s John Watson, and Bissell’s Dugan Karnazes and Patryk Akhurst. They discussed their data management philosophies, the need for detailed processes that fit each company, and why data management techniques must undergo continuous improvement to be effective.
Andy Shaughnessy: Dugan, would you please share your overall thoughts on data management, and we’ll go from there?
Dugan Karnazes: Coming from a consulting background, my first question, which shapes who’s managing the data, is “Who is your customer?” If you’re managing data for a contracting situation, ultimately you must give all the files back to the customer. You hope that they have standards for how they’re storing these things. The unfortunate reality that I saw is that many companies don’t. Even though they specify how they want their files back (and the good ones will give you a list of everything that makes up a complete data package), often they don’t even enforce that. Many times, four months down the road, they’ll ask for it again. So, who’s the customer? What are their requirements, and what are your own higher requirements?
When I was responsible for handing off a design to a customer, one company gave me a list of everything they wanted: “We want the PCB in this format. We want exports for the schematic libraries and a separate export for the footprint libraries.” It made it easy. When I gave it to them, they were highly surprised because no one else had ever given it to them.
I had other customers who said, “I don’t even know what an RC filter is. Why are you asking me that? I just want to come to you and get the boards.” Now I need to do it all for my standards, and I need to have a system internally for tracking that. I think that ownership of the standard needs to be set at the manager’s level, but ultimately, it’s always going to come down to the engineer and the people who are in the CAD package to make sure that the data is meeting those standards. I’m curious to see how other people handle this, because every group I’ve talked to handles it differently.
Shaughnessy: Right. John, you worked at an OEM for years; you had a lot of designers working for you. Who was responsible for all that data?
John Watson: First, it really depended on whether things were working well with the data or not working well (laughs). But, understanding your finish line and what you’re providing to that customer is vital. Let’s say your company makes Christmas cards that play music when you open them. They’re not going to be looking for the same quality of data as a DoD company. It’s a matter of understanding everyone’s role internally in your company. Who is responsible for creating the documents or that data? Who is responsible for QC-ing it? Who’s responsible for coming up behind and making sure it’s correct?
Dan Feinberg: Let’s say that there’s a gross error, something that should have been caught. Who is responsible: the company, or the individual employee who made the error?
Watson: I think it would be both because the company is responsible for putting in place the quality checks that are necessary to make sure it’s correct. If the process is not put in place and followed, then you’re doomed for failure.
Feinberg: That’s a good answer. I agree.
Watson: If you’re putting footprints on a board that have not been looked at and verified, according to a standard, and you’re using your fab house and assembly house to verify your footprints, forget it; you’re done as a company. I have worked in the medical field and the DoD as a PCB layout person. I can tell you their standards are so high that they had a set procedure and process to do things with a required endpoint, a deliverable; if you broke that SOP, you were done. That’s the level you must work at today.
Feinberg: Especially today. I agree because we see a a trend toward individuals not wanting to take responsibility.
Watson: Yes. When something happens, the first words out of anyone’s mouth are, “That’s not my fault. That wasn’t my area. That wasn’t my responsibility.”
I actually got to the point where I had my engineers signing documents, signing the schematic, signing the PCB, and releasing it. We would do a design review. We would pass a piece of paper around, and everybody who signed was saying, “Yes, I approve of this design.” We had gotten into a habit where six months down the road, if something was missed, everyone said, “No, I didn’t agree to that.” Then, you could pull that piece of paper out and say, “Well, there’s your signature.”
What happened? We need to do a postmortem and identify what happened here. Why did this occur? That’s where a lot of the solutions then happen in a company where a negative situation could become a positive for them. At least they learn a lesson through that.
To read this entire conversation, which appeared in the November 2021 issue of Design007 Magazine, click here.
Suggested Items
Specially Developed for Laser Plastic Welding from LPKF
06/25/2025 | LPKFLPKF introduces TherMoPro, a thermographic analysis system specifically developed for laser plastic welding that transforms thermal data into concrete actionable insights. Through automated capture, evaluation, and interpretation of surface temperature patterns immediately after welding, the system provides unprecedented process transparency that correlates with product joining quality and long-term product stability.
Smart Automation: The Power of Data Integration in Electronics Manufacturing
06/24/2025 | Josh Casper -- Column: Smart AutomationAs EMS companies adopt automation, machine data collection and integration are among the biggest challenges. It’s now commonplace for equipment to collect and output vast amounts of data, sometimes more than a manufacturer knows what to do with. While many OEM equipment vendors offer full-line solutions, most EMS companies still take a vendor-agnostic approach, selecting the equipment companies that best serve their needs rather than a single-vendor solution.
Keysight, NTT, and NTT Innovative Devices Achieve 280 Gbps World Record Data Rate with Sub-Terahertz for 6G
06/17/2025 | Keysight TechnologiesKeysight Technologies, Inc. in collaboration with NTT Corporation and NTT Innovative Devices Corporation (NTT Innovative Devices), today announced a groundbreaking world record in data rate achieved using sub-THz frequencies.
Priority Software Announces the New, Game-Changing aiERP
06/12/2025 | Priority SoftwarePriority Software Ltd., a leading global provider of ERP and business management software announces its revolutionary aiERP, leveraging the power of AI to transform business operations.
Breaking Silos with Intelligence: Connectivity of Component-level Data Across the SMT Line
06/09/2025 | Dr. Eyal Weiss, CybordAs the complexity and demands of electronics manufacturing continue to rise, the smart factory is no longer a distant vision; it has become a necessity. While machine connectivity and line-level data integration have gained traction in recent years, one of the most overlooked opportunities lies in the component itself. Specifically, in the data captured just milliseconds before a component is placed onto the PCB, which often goes unexamined and is permanently lost once reflow begins.