-
-
News
News Highlights
- Books
Featured Books
- smt007 Magazine
Latest Issues
Current IssueSpotlight on India
We invite you on a virtual tour of India’s thriving ecosystem, guided by the Global Electronics Association’s India office staff, who share their insights into the region’s growth and opportunities.
Supply Chain Strategies
A successful brand is built on strong customer relationships—anchored by a well-orchestrated supply chain at its core. This month, we look at how managing your supply chain directly influences customer perception.
What's Your Sweet Spot?
Are you in a niche that’s growing or shrinking? Is it time to reassess and refocus? We spotlight companies thriving by redefining or reinforcing their niche. What are their insights?
- Articles
- Columns
- Links
- Media kit
||| MENU - smt007 Magazine
Estimated reading time: 4 minutes
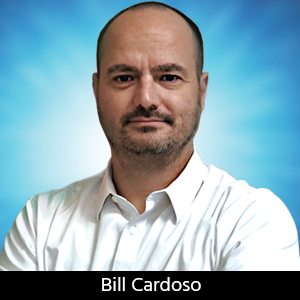
X-Rayted Files: Three or More Intriguing Thoughts on Reshoring
The ground beneath us is always shifting, and while the term “unprecedented” can be somewhat overused, it does seem to be a little tougher to keep our balance these days. For almost every economic disruption, there emerges some argument for how reshoring can mitigate it. This time around, though, there’s a bit of a tug-o-war between the disruptions that are shaping the manufacturing landscape and the broader economy. I’m no economist, but as a dyed in the wool entrepreneur I’d like to share three thoughts about the future of manufacturing with a focus on reshoring, the talent pool, and the joy of making things.
#1 Reshaping Our Supply Chains
Supply chain disruptions have caused pain across the economy and are among the drivers for renewed enthusiasm for reshoring. Reshaping our supply chains could make building things in America not only more practical, but potentially a real competitive advantage. While labor and other costs may be higher for domestic manufacturers, reducing friction for customers when it comes to things like delivery and service support can have a real impact on relationships and the sales they generate. By sourcing and manufacturing in America, we are certainly less susceptible to the constraints of international freight systems. If reshoring is really going to take hold this time around, we’ll need to address labor on a couple of fronts. Not only do we need to educate and train the manufacturing workforce of the future, but we need to attract them to the work.
#2 Closing the Skills Gap
If supply chain is causing a push toward reshoring, issues around labor have the potential to contribute to a pull. Between the “great resignation” and the “skills gap,” labor challenges may put the brakes on a return to domestic manufacturing. There are myriad reasons for talent bowing out of the workforce. For some of our most experienced workers, those nearing the ends of their careers, the strength of the stock market and swelling investment portfolios have resulted in many reaching their retirement savings goals years ahead of schedule. For others the pandemic-induced exodus from the office was a welcome change of pace, and a return to a pre-pandemic workplace and the commute that goes with it holds little appeal.
While the availability of talent presents one problem, the skills of the available talent can present another. Closing the skills gap has been a constant focus for American employers and is why so many of us eagerly support education and training initiatives specific to our industries. Increasing enthusiasm for STEM (or STEAM) education at all levels is having an impact, but I’d argue it still deserves far greater investment.
#3 Hype the Job Potential
As manufacturers, we have an added challenge. Having training opportunities available can only help close the skills gap if prospects are excited by the opportunities that such training creates. We need to actively overcome the reputation of manufacturing jobs as being dirty, dangerous, and monotonous. Advanced manufacturing and modern factories are exciting, and it is a message we need to share if we are going to attract talent. Those of us who have made careers of manufacturing know the pleasure we realize in making real, tangible, useful things. We need to promote that message more often and more broadly. In addition to supporting technical training through internships and endowments, we may need to think about attracting talent as a marketing and messaging challenge.
#4 Make Things Easier to Use
If I may (and since it’s my column, I’ll grant myself the latitude), I have a fourth thought in support of reshoring, overcoming the skills gap, and the future of advanced manufacturing. For those of us who make things used by others who make things, we need to make such things as easy to use as possible. The design of tools for advanced manufacturing should consider and be considerate of the experience of the end user. Incorporating and exploiting opportunities in automation can reduce risk and monotony in certain types of work, allowing talented employees to contribute in more meaningful and satisfying ways. Creating equipment that is genuinely user friendly creates space for technicians to fully utilize tools that otherwise might be too intimidating for workers to take full advantage of. I can’t tell you how many times we’ve won a new customer who already owned an advance inspection system that largely sat idle because it was just too complicated for most of their staff to use. Ease of use as a design feature ensures that the value of equipment will be maximized and can help close the skills gap by making tools more accessible.
I love making things, and I especially enjoy making them in America. I’m hopeful that the renewed interest in reshoring results in an actual resurgence in domestic manufacturing. Since hope is not a strategy, let’s do what we can together to seek out and support those who make things here, and support education and training for the talent that will sustain the future of domestic manufacturing. Let’s not forget to overtly celebrate the joy of manufacturing so that we can entice that young talent with the genuine satisfaction that comes from actually making something.
Dr. Bill Cardoso is CEO of Creative Electron.
More Columns from X-Rayted Files
X-Rayted Files: Best Practices in Buying MachinesX-Rayted Files: ’23 and Me?
X-Rayted Files: Battery-Powered Advancements Keep on Ticking
X-Rayted Files: What’s Cooler Than X-ray?
X-Rayted Files: My Favorite BGA Assembly Ever, Part 3
X-Rayted Files: My Favorite BGA Assembly Ever, Part 2
X-Rayted Files: My Favorite BGA Assembly Ever
X-Rayted Files: Smart vs. Intelligent SMT Factory