-
- News
- Books
Featured Books
- design007 Magazine
Latest Issues
Current IssueShowing Some Constraint
A strong design constraint strategy carefully balances a wide range of electrical and manufacturing trade-offs. This month, we explore the key requirements, common challenges, and best practices behind building an effective constraint strategy.
All About That Route
Most designers favor manual routing, but today's interactive autorouters may be changing designers' minds by allowing users more direct control. In this issue, our expert contributors discuss a variety of manual and autorouting strategies.
Creating the Ideal Data Package
Why is it so difficult to create the ideal data package? Many of these simple errors can be alleviated by paying attention to detail—and knowing what issues to look out for. So, this month, our experts weigh in on the best practices for creating the ideal design data package for your design.
- Articles
- Columns
- Links
- Media kit
||| MENU - design007 Magazine
Estimated reading time: 3 minutes
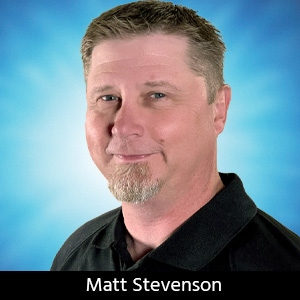
Connect the Dots: Everything You Wanted to Know About Electromagnetic Interference
EMI is another of those TLAs (three-letter acronyms) that the PCB industry is notorious for. You hear it all the time, referring to electromagnetic interference. The devices we create are, in the context of this conversation, bundles of boards, chips, and cables that produce and are affected by EMI. When current flows through wires, traces, or circuits, some of the energy is propagated through the air in the form of electromagnetic radiation. This also takes place within a closed design—creating disturbance voltages throughout the conductors in your device.
Though most prevalent in devices with longer interconnects and at higher frequencies above 50MHz, nothing operates at 100% electromagnetic compatibility. This means every device is going to generate at least some amount of EMI.
If enough EMI radiates from a device, it will interfere with the operation of other electronic systems operating in the vicinity. That’s why they ask you to turn off your cellphones on airplanes and the reason grandpa made your dad turn off the radio in his room when it was time for Ed Sullivan on TV.
Keeping an Eye on EMI
There are two main concerns with EMI that you need to consider. You should first determine how much EMI your device is generating and radiating to the environment. Different operational environments bring with them unique tolerances for EMI. An electronic device that is part of a billionaire’s spaceship near other devices on board would have a much lower EMI tolerance than a moisture evaporator operating in the middle of a desert.
Everyone from the FCC to the DoD to a slew of international regulatory bodies are at hand to dictate the amount of interference that a device can give off, depending on its intended use. These regulations have been put in place for personal safety and to ensure an electronic device will be able to carry out its function long term.
It’s also important to determine your device’s inherent ability to operate in the presence of EMI, regardless of whether it is EMI-created within the device or bombarding it from external sources. Too much exposure to interference can negatively impact the functionality of some systems and you will need to design shielding, grounding, or other protection.
Poor PCB design is many times the culprit when it comes to intolerable levels of EMI. The issues that often cause problems can be traced to design flaws that cause interference among the traces, circuits, vias, PCB coils, and other elements.
Limiting the EMI in a PCB layout can be an effective method for reducing emissions, meeting FCC regulations, and keeping your design signals clean so the system works as expected.
Designing With EMI in Mind
Here are a few items to consider during the planning and schematic stages of your design that will set you on the right path.
- Choose SMD components over through-hole parts. Generally, the leads on the through-hole parts create higher levels of inductance and thus opportunity for EMI.
- Maximize ground area, so signals can disperse more easily with more area. If you need to keep the area of your ground plane as small as possible, create a multi-layer PCB.
- Design with multilayers—add a ground plane on the layer directly below the external signals (2 and n-1). The presence of these planes near the signal will effectively reduce the return path, keep signals clean, and limit EMI emission.
- Connecting decoupling or bypass capacitors to these planes offers another effective technique for reducing EMI because of the short and logical return paths created.
- If you are using split planes to avoid having too many ground planes in your design, be sure they are only connected at a single point to avoid creating loops that effectively become antennas that radiate EMI.
- In multi-layer PCBS, use solid ground planes rather than hashed planes to reduce impedance levels.
- Limit the operating current and/or the rise times of the signals to help reduce larger fluctuations in current offering lower EMI emission rates.
- Match the impedance on signals. This is a critical practice of design especially at higher signal speeds that will reduce the opportunity for signal reflection, harmonics, ringing, and overshooting digital signals—all of which increase the EMI radiation.
Don’t let yourself be surprised by EMI. It can create issues with your projects that could result in delays, budget overrun, and missed deadlines. Considering EMI during the pre-planning stage of your PCB design can help save you time and effort in the prototyping and testing phases.
This column originally appeared in the January 2022 issue of Design007 Magazine.
More Columns from Connect the Dots
Connect the Dots: Sequential Lamination in HDI PCB ManufacturingConnect the Dots: The Future of PCB Design and Manufacturing
Connect the Dots: Proactive Controlled Impedance
Connect the Dots: Involving Manufacturers Earlier Prevents Downstream Issues
Connect the Dots: Stop Killing Your Yield—The Hidden Cost of Design Oversights
Connect the Dots: Designing for Reality—Routing, Final Fab, and QC
Connect the Dots: Designing for Reality—Surface Finish
Connect the Dots: Designing for Reality—Solder Mask and Legend