-
- News
- Books
Featured Books
- design007 Magazine
Latest Issues
Current IssueProper Floor Planning
Floor planning decisions can make or break performance, manufacturability, and timelines. This month’s contributors weigh in with their best practices for proper floor planning and specific strategies to get it right.
Showing Some Constraint
A strong design constraint strategy carefully balances a wide range of electrical and manufacturing trade-offs. This month, we explore the key requirements, common challenges, and best practices behind building an effective constraint strategy.
All About That Route
Most designers favor manual routing, but today's interactive autorouters may be changing designers' minds by allowing users more direct control. In this issue, our expert contributors discuss a variety of manual and autorouting strategies.
- Articles
- Columns
- Links
- Media kit
||| MENU - design007 Magazine
Estimated reading time: 7 minutes
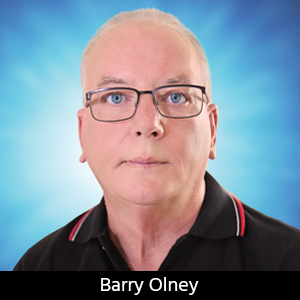
Beyond Design: High Voltage PCB Constraints
Way back in my early 20s, I was tasked with repairing Marconi HiPot testers. These ancient, bulky machines were basically high voltage generators used for testing the dielectric withstanding voltage or isolation of 50KV high voltage power transmission lines that are strewn across the countryside. Opening the box, you see a string of diodes and several huge, high voltage ceramic capacitors creating a voltage multiplier. I used to wind these up to a humming 60KV and they sure packed one hell of a punch (even when switched off), as I soon found out. This instilled in me the importance of spacing to isolate high voltage.
Figure 1: Multiple exposure photo of Tesla in Colorado Springs lab (Source: Wikimedia Commons)
Testing this lethal weapon was an ordeal. I used to position the output cables about nine inches from either end of a 240V three-foot fluorescent tube and stand well back; a crack of blue lightning arced across the gaps and ignited the tube as I wound up the voltage. I felt a bit like Nikola Tesla in his Colorado Springs lab surrounded by high voltage discharges (Figure 1). However, if the HiPot tester did not reach maximum voltage, then locating the issue was done at arm’s length. I used a matchbox to slightly open the lid, turned off the lights and watched the sparks fly from minute cracks in the ceramic capacitors. So, it was easily fixed by just replacing the offending caps. Unfortunately, I forgot to discharge the caps one day and found myself on the floor, on the other side of the room, still holding my spanner. Lesson learned.
Appropriate trace spacing in a PCB design maintains signal integrity and crosstalk, and prevents the propagation of electromagnetic energy coupling between components. We typically use three times the trace-to-reference plane distance as a rule of thumb. However, this is for digital circuits with low supply voltages. In high voltage PCB design, trace spacing becomes even more important or you may end up with a charred board.
To begin with, every designer needs a set of well-established design rules to base their constraints on. The IPC has provided the electronics industry with guidelines for design and manufacture of printed circuit boards, compiled over the years, with the support of both committee and industry members.
The IPC has established design rules for trace spacing, pad-to-pad spacing, and pad-to-trace spacing for PCB designs that incorporate high voltages. The IPC-2221A Generic Standard on Printed Board Design provides clearance and creepage tables that assist with setting design rules and with performing design rule checks and electrical rule checks for minimum requirements.
Table 1 is an extract from the IPC-2221A standard and provides the effective clearance required for both internal (stripline) layers and external (microstrip) layers. However, above 500V the clearance needs to be calculated. For 600V, for instance, the clearance is:
600V – 500V = 100V
0.25 mm + (100V x 0.0025 mm) = 0.5 mm clearance
Design rules must keep up with the latest devices and fabrication processes—without losing sight of design for manufacturability (DFM). DFM is the practice of designing board products that can be produced in a cost-effective manner using existing manufacturing processes and equipment. If you follow the above IPC guidelines, you will be designing for both manufacturability and mass production. However, at times one must stretch the rules a little to meet the specific requirements of a design. This is fine, providing you can justify the reasons and tolerate the consequence of your decision.
Entry-level EDA tools tend to rely on the skills of the PCB designer to detect possible issues as they arise during the design process. However, these days a more constraint-driven, correct by construction approach is required for complex designs. Once the rules are established, they will be followed by downstream tools and validated to conform by the various design rule checkers (DRCs).
Along with applying design rules, PCB layouts can also include slots or vertical insulation barriers between traces. Any metallic print pattern or printed circuit trace that has sharp edges can cause a high electric field across insulators and a flashover.
Whenever routing traces for high voltage PCBs, the following points are most important:
- Keep the specified clearance between traces and pads that have a high voltage disparity.
- Avoid any sharp turns and edges as these can act as areas of the concentrated electric field.
- Avoid running very high voltage traces on the internal layers of the board.
High voltage design requires insulation that has high dielectric strength, high resistivity to prevent arcing, and a low power factor that reduces heating effects and the possibility of thermal breakdown. Insulating materials may include encapsulating resins applied to high voltage cavities, conformal coatings, or solid insulation that surrounds conductors.
The Comparative Tracking Index (CTI) is used to measure the electrical breakdown properties of an insulating material. It is the maximum voltage at which a material withstands 50 drops of contaminated water without forming conductive paths because of electrical stress, contamination, or humidity. Materials that have a high CTI value have a lower required minimum creepage distance and allow a shorter distance between two conductive parts. The shorter distance allows the use of high-density circuits in a high voltage environment, which is commonplace these days.
Along with requiring different types of insulating materials, high voltage PCBs also need board materials that protect from voltage breakdown and offer the physical properties that match application needs. Although FR-4 laminates have a high breakdown voltage, the weaker structure and porosity of FR-4 can allow the material to become prone to contamination and a gradual lessening of the dielectric value. Because of the FR-4 limitations, high voltage laminates that have a non-conductive base layer and prevent arcing are best for high voltage PCB design. High voltage laminates have higher levels of resin and glass than standard board materials.
A board material that is specifically designed to tolerate an overvoltage event, as well as the regular high voltage operating conditions is best. There are a few material options to consider when dealing with high voltage:
- FR-4 laminate: FR-4 has a very high dielectric breakdown. However, it is more porous than BT epoxy and polyimide, which makes it easier for the substrate to become contaminated. It also has a weak edge structure, and as the edge cracks, the dielectric value will decrease. Aging is a likely problem, especially for electronics near the edge. FR-4 also has no recovery or protection from carbonization that occurs during over-voltage events.
- BT epoxy: A thermoset resin, BT epoxy (bismaleimide triazine resin) has strong sidewalls and is better for applications with planar coils and medium voltage circuits. For example, AGC (Nelco) N5000 BT epoxy laminate and prepreg provides superior electrical properties.
- High V laminates: There are several high voltage laminates. Isola’s is one of the most well-known, that actually extinguishes arcs and leaves a non-conductive base layer. For example, IS550H was developed in conjunction with a consortium of industry experts for high power and high voltage applications and PEV and HEV automotive electrification. The resulting solution addresses critical application needs for use in a harsh environment where very demanding, long-term thermal reliability performance, extreme thermal cycling, and very high voltage conductive anodic filament (CAF) formation and electro-migration resistance are required.
Finally, the copper finish of the PCB laminate is also important. If there is a rough copper surface with particles, inconsistencies and contamination, arcing may occur. These concentrate the electric field and are more prone to arcing.
Key Points
- Spacing is crucial for high voltage isolation.
- Appropriate trace spacing in a PCB design maintains signal integrity, prevents crosstalk, and prevents the propagation of electromagnetic energy coupling between components.
- The IPC-2221A Generic Standard on Printed Board Design provides clearance and creepage tables that assist with setting design rules for high voltage design.
- Any metallic print pattern that has sharp edges can cause a high electric field across insulators and a flashover.
- High voltage design requires insulation that has high dielectric strength, high resistivity to prevent arcing, and a low power factor that reduces heating effects and the possibility of thermal breakdown.
- The Comparative Tracking Index (CTI) is used to determine which PCB material type works best for the specific application when selecting dielectrics and insulators for a PCB.
Resources
- Beyond Design: High-Speed PCB Design Constraints, by Barry Olney, Design007 Magazine, May 2019
- High Voltage Power Supply Design Guide for Space, NASA
- High Voltage Circuit Design Guidelines and Materials, Cadence PCB Solutions
- High Voltage PCB Design Tips: Materials for High Voltage PCBs, Altium
- IPC-2221A Generic Standard on Printed Board Design
This column originally appeared in the January 2022 issue of Design007 Magazine.
More Columns from Beyond Design
Beyond Design: Effective Floor Planning StrategiesBeyond Design: Refining Design Constraints
Beyond Design: The Metamorphosis of the PCB Router
Beyond Design: Radiation and Interference Coupling
Beyond Design: Key SI Considerations for High-speed PCB Design
Beyond Design: Electro-optical Circuit Boards
Beyond Design: AI-driven Inverse Stackup Optimization
Beyond Design: High-speed Rules of Thumb