-
- News
- Books
Featured Books
- smt007 Magazine
Latest Issues
Current IssueSupply Chain Strategies
A successful brand is built on strong customer relationships—anchored by a well-orchestrated supply chain at its core. This month, we look at how managing your supply chain directly influences customer perception.
What's Your Sweet Spot?
Are you in a niche that’s growing or shrinking? Is it time to reassess and refocus? We spotlight companies thriving by redefining or reinforcing their niche. What are their insights?
Moving Forward With Confidence
In this issue, we focus on sales and quoting, workforce training, new IPC leadership in the U.S. and Canada, the effects of tariffs, CFX standards, and much more—all designed to provide perspective as you move through the cloud bank of today's shifting economic market.
- Articles
- Columns
- Links
- Media kit
||| MENU - smt007 Magazine
Estimated reading time: 4 minutes
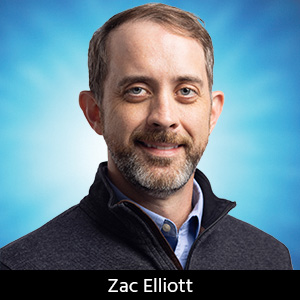
Lean Digital Thread: Achieving Supply Chain Resilience
In this column I’d like to address the challenges manufacturers have been facing due to the semiconductor chip shortage that began in late 2020 because of the COVID-19 pandemic, as well as ways to mitigate those challenges.
The shortage of semiconductor components emerged during a hypergrowth of demand for semiconductor chips. To emphasize the magnitude of the hypergrowth, the global semiconductor market is projected to grow from $452.2 billion in 2021 to $803.1 billion in 2028—almost 78% in just seven years1, or an average of 8.5% annually. The combination of this growth in demand and the shortage of semiconductor chips poses a great challenge for the entire electronics industry and for manufacturers, particularly.
A 2020 Deloitte survey2 showed that almost all manufacturers have encountered delays in semiconductor component supply as well as other critical issues such as poor component quality, order cancellations, and part substitution. These significantly impact manufacturers’ ability to supply products to customers on time, while maintaining quality and remaining within budget.
Keys for Building Supply Chain Resilience
According to the Deloitte survey, there are five key considerations in building supply chain resilience. These considerations include supply chain configuration and control, visibility into the supply chain, digitalization of supply networks, collaboration with the supply chain, and supply chain flexibility. I will cover each of these considerations in this article.
1. Supply chain configuration and control
In the Deloitte survey, 85% of the respondents indicated that analyzing critical dependencies in the supply chain is important to their business. Manufacturers need to be aware, now more than ever, of all critical aspects in the supply chain that might affect their ability to deliver their products to their customers. To respond effectively to emerging issues, manufacturers need to consider dual or multiple sourcing for critical components, maintain both local and offshore suppliers in order to cope with regional risks, take the supply risks into consideration in their make-or-buy-decisions, be aware of the resilience of production, and more.
Another aspect that manufacturers learned during the crisis is that bigger suppliers are not necessarily the most critical. Sometimes the least expensive and almost trivial component might become the bottleneck in the supply chain and eventually affect their ability to produce their goods on time.
Building a configurable supply chain with redundancy for all critical components presents an IT challenge for the manufacturer. To address that challenge, manufacturers must digitalize their supply chains and manage risk regarding each and every supplier.
2. Visibility into the supply chain
To achieve supply chain resilience, it is important for the manufacturers to have visibility into the supply chain. During PCB design, it can assist them in identifying components that are currently in low supply or might be in low supply during the project lifecycle and thus cause delays, reduced order quantity, order cancellation, or create a need for replacement components which would mean redesigning the PCB and redoing the NPI. The main objective is to identify these risks as early as possible in the process and turn these insights into actions that will, in turn, mitigate or eliminate supply chain risks.
3. Digitalization of supply networks
Digitalization and extending the digital thread throughout the supply chain is key to building supply chain resilience. With the new trend of cloudification in the industry and the emergence of cloud solutions, there is a great opportunity to break the silos of information in the designing organization and enable analysis of PCB supply chain risks during the design stage. This type of digitalization allows the PCB designer to get immediate feedback about the ability to manufacture the design and could include a supply chain analysis that would indicate any possible risk with any component used in the design as part of the design-for-manufacturing (DFM) analysis. This kind of cloud solution could automatically offer all possible alternatives to mitigate problems in the component supply. The value of this kind of cloud solution is that supply-related decisions would be taken during the product design stage, mitigating the risks of delays in component supply that lead to cancellations or reduced order quantity.
4. Collaboration with the supply chain
The digitalization described in the previous section could be further leveraged to gain full collaboration across the supply chain. From an IT perspective, it would be almost as if the supply chain was part of the design organization. This would enable automation and AI engines that could fully harmonize the design stage with the supply chain and would minimize risk in the supply chain, thus achieving a resilient supply chain.
5. Supply chain flexibility
To mitigate the various supply chain risks, supply chain flexibility is required. Risks include geopolitical tensions, protectionist tariffs, part unavailability, pandemic-related restrictions, and more. Given the risks, it is impossible to reach supply chain resilience without flexibility. This flexibility requires building a supply chain that allows redundancy in components and resource suppliers, while taking all the risks into consideration. Flexibility is key to managing a network of suppliers, being able to operationally route orders and automatically respond to any emerging issue that might affect the supply of components and resources.
References
- Semiconductor market, FORTUNE Business Insights, May 2021.
- Building Supply Chain Resilience beyond COVID-19, Deloitte.
Zac Elliott is technical marketing engineer for Siemens Digital Industries Software.
Check out this additional content from Siemens Digital Industries Software:
- The Printed Circuit Assembler's Guide to ...Smart Data: Using Data to Improve Manufacturing?by Sagi Reuven and Zac Elliott (a free eBook available for download)
- The Printed Circuit Assembler's Guide to… Advanced Manufacturing in the Digital Age? by Oren Manor (a free eBook available for download)
- The Printed Circuit Designer’s Guide to… Power Integrity by Example by Fadi Deek (a free eBook available for download)
- Siemens’ free, 12-part, on-demand webinar series?“Implementing Digital Twin Best Practices From Design Through Manufacturing.”
- RealTime With ...?Siemens and Computrol: Achieving Operational Excellence in Electronics Manufacturing
- You can also view other titles in our full I-007e Book library here
More Columns from Lean Digital Thread
Lean Digital Thread: The Manufacturing Metaverse RevisitedLean Digital Thread: The Secure Digital Thread
Lean Digital Thread: The Manufacturing Metaverse
Lean Digital Thread: Closing the Loop on Manufacturing
Lean Digital Thread: Keeping an Eye on Quality
Lean Digital Thread: Streamlining the Internal Supply Chain
Lean Digital Thread: (Pro)curing the Supply Chain Virus
Lean Digital Thread: Why is Everyone Suddenly Interested in Supply Chain?