-
- News
- Books
Featured Books
- design007 Magazine
Latest Issues
Current IssueProper Floor Planning
Floor planning decisions can make or break performance, manufacturability, and timelines. This month’s contributors weigh in with their best practices for proper floor planning and specific strategies to get it right.
Showing Some Constraint
A strong design constraint strategy carefully balances a wide range of electrical and manufacturing trade-offs. This month, we explore the key requirements, common challenges, and best practices behind building an effective constraint strategy.
All About That Route
Most designers favor manual routing, but today's interactive autorouters may be changing designers' minds by allowing users more direct control. In this issue, our expert contributors discuss a variety of manual and autorouting strategies.
- Articles
- Columns
- Links
- Media kit
||| MENU - design007 Magazine
Estimated reading time: 6 minutes
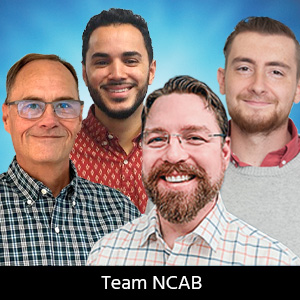
Fresh PCB Concepts: What Damage Does the Assembly Process Have on a PCB? Part 4
In Part 3 of this series, I discussed how phenolic cured laminates can be mechanically weaker than their dicey cured laminate counterparts. I pointed out some of the material properties listed on material data sheets that explain and support this point. Whereas the phenolic systems are better at thermal management, the dicey systems are better under mechanical stress. There is no right or wrong here. The systems just perform differently under different circumstances. Understanding the differences and how they relate to the applied assembly process are important to ensure success. For this post I would like to discuss the effect moisture has on the printed circuit board.
What many people don't realize is that printed circuit boards are hygroscopic. PCBs shall absorb available moisture from the surrounding environment to the point of equilibrium. The various FR-4 laminate data sheets list moisture absorption values. The values are calculated in accordance with the IPC-TM-650 2.6.2.1A specification. The 2.6.2.1A specification basically tests a solid rectangular piece of FR-4 free of copper, no holes, and the edges sanded smooth. First the sample is preconditioned by dry baking the material. This forces any residue moisture out. Immediately after dry baking, the sample is weighed. This is the dry weight. The sample is then submerged for 24 hours in distilled water. The sample is removed, towel dried, and then weighed. This is the wet weight. The wet and dry weights are then plugged into a formula listed in the 2.6.2.1A specification to produce the moisture absorption value.
The value listed on the FR-4 datasheet is for a pristine piece of FR-4. It does not reflect the value you would see on the actual printed circuit board. The tested sample is a solid smooth rectangular block. There are only 6 planes of contact sanded down to remove edge fractures. A finished printed circuit board has many more openings where moisture can be absorbed through. The process of drilling holes, V-scoring and routing result in some material fracturing at the edge of the machined edges. The amount of fracturing is dependent upon the fabrication process and the FR-4 used to make the board. Fracturing promotes moisture absorption. The moisture values listed on the datasheets indicate the FR-4 material's minimum potential to absorb moisture. The completed printed circuit board shall have a higher potential due to the machining and fabrication process.
What does this have to do with the post topic?
If moisture is not managed properly, a lot.
A significant challenge faced by an assembler is electro-static discharge (ESD). ESD can damage electronic devices and components outright so they fail immediately or damage them enough so that they fail later on in the field. Controlled environments and humidification are employed to minimize a static charge build up in the work area. Some contract manufacturing facilities employ elaborate misting systems that pump moisture into the assembly area. The point is that assemblers work in a moisture rich environment. Once the board is unpackaged and enters the assembly area it starts to absorb moisture. How much moisture is a function of how much time the board spend in that environment.
How much moisture a printed circuit board absorbs is a function of several parameters:
- The area relative humidity
- Time in the area
- The bare board fabrication process
- The type of FR-4 laminate used
- Moisture content of the printed circuit board as received
Dry baking a printed circuit board prior to shipping is considered an option by some printed circuit board fabricators. They may not dry bake the printed circuit boards unless requested to do so. When in doubt ask the fabricator what their policy is or specify dry baking as a requirement.
Moisture in the printed circuit board shall become a problem when the board is exposed to assembly soldering temperatures. Hygroscopic materials containing moisture are placed under stress when exposed to heat. The moisture wants to expand when heated. The expansion stress is referred to as the Coefficient of Hygroscopic Expansion (CHE). It may also be referred to as the Coefficient of Moisture Expansion (CME). The material data sheets provided by FR-4 laminate manufacturers do not list values on CHE/CME data. The import thing to understand is that materials bearing moisture expand when heated. The moisture expands at a different rate. This places stress on the laminate.
What's the worst thing that can happen? Delamination.
If enough moisture is present the FR-4 shall delaminate. Moisture exposed to soldering temperature will vaporize and violently expand. Delamination caused by moisture expansion is considered a mechanical failure. The stress exceeded the laminate mechanical bond or flexural strength. The delamination shall be at the weakest point containing the most moisture. Zones for failure may include prepreg to copper, prepreg to core or between plys of prepreg. The delamination may propagate from a drilled hole or other fracture point. Phenolic cured epoxy systems can be mechanically weaker than their dicey cured cousins. Phenolic laminates may be more susceptible to moisture delaminations due to this property.
Bow and Twist
If moisture is present and the design is unbalanced enough, the board shall expand unevenly with a bow and twist. How is this possible? It is important to understand that the assembly temperatures are above the FR-4 laminate glass transition temperature (Tg). Below Tg, the epoxy is hard and solid. Above Tg, the epoxy becomes soft and pliable. Copper expands at a slow and steady rate (19 ppm/deg C) as it is heated and is not a hygroscopic material. When the epoxy is heated above the Tg, the epoxy becomes soft and pliable. Below the Tg, the epoxy rate of expansion is near 25 ppm/deg C. Above the Tg, the epoxy rate of expansion is near 250 ppm/deg C. In a PCB, the distribution of copper may not be even due to the design. Materials will expand at different rates. An area of the design with low amounts of copper expands at a greater rate than an area of the board with a high amount of copper. The epoxy, being soft and pliable warps, resulting in the bow and twist between the different materials. When the board cools down below the Tg, the epoxy becomes hard and solid again. If the PCB has bow and twist when it cools below the Tg, the PCB may lock in the new bow and twisted shape. A PCB in a dry state will experience bow and twist to some degree. Moisture absorbed by the FR-4 expands at a higher rate than the epoxy and copper. Moisture can increase the amount of bow and twist.
How Do You Minimize the Effect of Moisture at Assembly?
If unsure of the moisture content of the PCB, you dry bake the PCB before populating it with components and prior to any thermal exposure to soldering temperatures. Dry baking at low temperatures for long periods of time works best. For PCBs, the temperature needs to be above 100° C to gradually vaporize and force the moisture out. Forcing the moisture out prior to assembly temperatures eliminates the effect of moisture on the assembly process. NCAB Group provides guidance on dry baking parameters for rigid PCBs and for flex/rigid-flex PCBs.
David Duross is an engineering director for NCAB Group USA.
More Columns from Fresh PCB Concepts
Fresh PCB Concepts: More Than Compliance—A Human-centered Sustainability ApproachFresh PCB Concepts: Assembly Challenges with Micro Components and Standard Solder Mask Practices
Fresh PCB Concepts: The Power of a Lunch & Learn for PCB Professionals
Fresh PCB Concepts: Key Considerations for Reliability, Performance, and Compliance in PCBs
Fresh PCB Concepts: Traceability in PCB Design
Fresh PCB Concepts: Tariffs and the Importance of a Diverse Supply Chain
Fresh PCB Concepts: PCB Stackup Strategies—Minimizing Crosstalk and EMI for Signal Integrity
Fresh PCB Concepts: PCB Plating Process Overview