-
- News
- Books
Featured Books
- pcb007 Magazine
Latest Issues
Current IssueInventing the Future with SEL
Two years after launching its state-of-the-art PCB facility, SEL shares lessons in vision, execution, and innovation, plus insights from industry icons and technology leaders shaping the future of PCB fabrication.
Sales: From Pitch to PO
From the first cold call to finally receiving that first purchase order, the July PCB007 Magazine breaks down some critical parts of the sales stack. To up your sales game, read on!
The Hole Truth: Via Integrity in an HDI World
From the drilled hole to registration across multiple sequential lamination cycles, to the quality of your copper plating, via reliability in an HDI world is becoming an ever-greater challenge. This month we look at “The Hole Truth,” from creating the “perfect” via to how you can assure via quality and reliability, the first time, every time.
- Articles
- Columns
- Links
- Media kit
||| MENU - pcb007 Magazine
Estimated reading time: 5 minutes
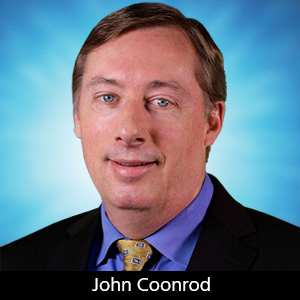
Lightning Speed Laminates: Prepreg Choices for Millimeter-wave PCB Applications
There are numerous prepreg choices in the PCB industry. In the past, the choice of prepreg was often dominated by PCB fabrication concerns. The prepregs used for high frequency or high-speed digital (HSD) address many of the same PCB fabrication concerns, but they also have other properties which are important for consistent high-frequency or HSD performance. There are also other bonding materials used as prepreg, such as a film or non-glass woven bonding materials, which are called bonding film or bondplys. Basically, these prepregs and other bonding materials are used to adhere the different layers in a multilayer PCB and can have a significant influence on many aspects of the circuit.
Over the past several years there have been more high-volume PCB programs that are using millimeter-wave (mmWave) frequencies. Most of these applications, until the past few years, are PCBs typically built as a four- or six-layer circuit with only the top two copper layers being related to the high frequency circuitry. Many of the more recent mmWave PCBs, especially those used in high resolution automotive radar, are multilayer PCBs with many high frequency circuit layers and in some cases the entire multilayer PCB is designed to have all layers to be supportive of mmWave frequencies. It is these types of circuitry where the prepreg and bondplys can be critical to good RF performance and still need to maintain all the other properties for good PCB fabrication and reliability.
A circuit using mmWave frequencies is a propagating medium for the wave, and the wavelengths at these high frequencies are very small. Generally, the small wavelength means the propagating wave will be more sensitive to anomalies in the medium than a propagating wave at a lower frequency. There are several items which are relatively normal to the circuit fabrication process, which could be considered an anomaly. Having a very small etching defect that is normally acceptable at lower frequencies may not be acceptable at mmWave frequencies. The normal variation of conductor trapezoidal effects, differential etching, slight undercut, layer-to-layer alignment, are all things that can normally happen in the PCB fabrication process and are relatively harmless to the RF performance of the PCB when operating at lower frequencies. However, at mmWave frequencies these normal variations can be problematic.
Another issue that is relatively normal and related to the high frequency circuit materials, is the glass reinforcement layers which are used to give mechanical stability to the material, among other things. Depending on the formulation of the laminate or prepreg and the glass style used, the supporting glass fabric can cause small disturbances in the RF propagation medium of the PCB. Again, at lower frequencies this may not be a concern, but at mmWave frequencies the very small wavelength can easily detect and be affected by the small differences due to the glass and/or overall formulation of the laminate or prepreg.
The main issue with the glass is known as the glass-weave effect, fiber-weave effect, or woven-glass-weave effect. The glass styles that have been used for decades are typically open-weave glass and, as the name implies, there are openings between the glass bundles. The glass that has been typically used is E-glass and that type of glass has a Dk of about 6 and a Df near 0.004. However, the E-glass Df will significantly increase with an increase in frequency and the Dk will decrease some as well. The basic issue for the glass-weave effect is related to the opening size in the glass fabric as well as the wavelength of the propagating wave.
For example, if the average opening size in the glass fabric is 16 mils x 16 mils and operating at 3.6 GHz with a wavelength of 2.1 inches (or 2100 mils), the openings in the glass fabric are such a small percentage of the propagating wavelength, that the openings do not have a significant effect on the wave performance. Although, it is well known that a fraction of a wavelength can be significant and if an anomaly is half wavelength in size it can cause wave disturbance in the propagation of the wave. If the anomaly is one-quarter wavelength it can also cause a disturbance but usually less than the half wavelength anomaly.
Typically, around one-eighth wavelength or less and the anomaly will not influence the propagating wave. Continuing with the example and using the same glass with openings of 16 mils x 16 mils and now considering the wavelength at 77 GHz, which is 97 mils, it is obvious that the 16-mil anomaly is a larger portion of the 97-mil wavelength and can have a disturbance on the propagating wave. At this frequency, the 1/8th wavelength size is 12 mils and the 16-mil opening in the glass will likely have some influence on the wave behavior.
These mmWave prepregs will often use open-weave glass due to its lower cost than spread-glass fabric, a better performing alternative glass fabric. Spread-glass fabric has very few or no openings between the glass bundles and will behave as a more uniform propagating medium than one using open-weave glass. Additionally, it has been found that if the laminate is heavily loaded with ceramic fillers, the differences of the propagating medium between the openings and the glass bundles of the glass fabric are greatly minimized.
Due to concerns of the glass-weave effect, many of the legacy mmWave PCB designs used an unsupported ceramic-filled laminate such as RO3003G2 laminate. In this case, there is no glass fabric layer, so the glass-weave effect is not applicable. However, due to the more recent high resolution mmWave designs, which use many layers for mmWave circuitry, a laminate with supporting glass fabric is needed for improved circuit fabrication, and then laminates using spread-glass are used such as the CLTE-MW laminate. Additionally, this laminate not only has the spread-glass, but it is also heavily loaded with ceramic filler and the glass-weave effect is typically not a concern at 77 GHz.
With the higher resolution mmWave radar circuits, the prepreg must also have very good RF performance properties. There are prepregs which have no glass reinforcement, which means the glass-weave effect is not a concern. Some of these prepregs or bondplys may need special lamination conditions and it is recommended to speak with your material provider’s technical support person about how to process these materials for circuit fabrication.
For certain high resolution mmWave radar circuitry, circuit materials that are glass reinforced are desired for the PCB fabricator to obtain good yields and good reliability of the PCB. These prepregs are often available with open-weave or spread-weave glass styles and it is best to use the spread-weave versions of this prepreg for mmWave circuitry. Additionally, some of these prepregs can have spread glass and be heavily loaded with ceramic filler, which is a best-case scenario for mitigating the glass-weave effect. Many of these prepregs are formulated to be friendly in the PCB fabrication process, but it is still suggested to contact your technical support engineer at the material company to ensure the processing and final performance will be as needed.
This column originally appeared in the February 2022 issue of Design007 Magazine.
More Columns from Lightning Speed Laminates
Lightning Speed Laminates: Millimeter-wave Properties and PCB Design ChallengesLightning Speed Laminates: Optimizing Thermal Management for Wireless Communication Systems
Lightning Speed Laminates: Test Vehicles for PCB Electrical Material Characterization
Lightning Speed Laminates: Optimum Thermal Stability Considerations
Lightning Speed Laminates: Thermal Management Isn’t Getting Easier
Lightning Speed Laminates: Benefits of High-Performance Hybrid Multilayer PCBs
Lightning Speed Laminates: An Overview of Copper Foils
Lightning Speed Laminates: The Importance of Circuit Features for Millimeter-Wave Applications