-
- News
- Books
Featured Books
- smt007 Magazine
Latest Issues
Current IssueSupply Chain Strategies
A successful brand is built on strong customer relationships—anchored by a well-orchestrated supply chain at its core. This month, we look at how managing your supply chain directly influences customer perception.
What's Your Sweet Spot?
Are you in a niche that’s growing or shrinking? Is it time to reassess and refocus? We spotlight companies thriving by redefining or reinforcing their niche. What are their insights?
Moving Forward With Confidence
In this issue, we focus on sales and quoting, workforce training, new IPC leadership in the U.S. and Canada, the effects of tariffs, CFX standards, and much more—all designed to provide perspective as you move through the cloud bank of today's shifting economic market.
- Articles
- Columns
- Links
- Media kit
||| MENU - smt007 Magazine
Estimated reading time: 9 minutes
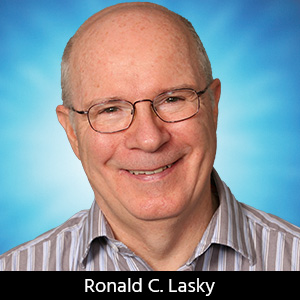
Maggie Benson's Journey: A Tale of Two Perspectives
Editor’s note: Indium Corporation’s Ron Lasky continues this series of columns about Maggie Benson, a fictional character, to demonstrate continuous improvement and education in SMT assembly.
The workers at Ivy Electronics felt nervous. Because their company had recently been sold, many expected that the new management would lay them off. They worried their backgrounds and experience at Ivy Electronics did not provide them with enough skills to land a new job, even in the current surplus environment. The workers gathered on the shop floor to hear from the new owners. Ned Price, the previous owner, was not present.
A tall, confident woman entered the shop floor. “Hello everyone, I’m Maggie Benson, your new co-worker at what will now be called Ivy Benson Electronics.”
Everyone held their breath, expecting the worst.
“I want to start by reassuring anyone who may be concerned that you will be able to keep your jobs,” Maggie announced to the group, adding, “All employees will also receive an immediate 20% raise.”
The room was quiet enough to hear a pin drop. The workers were so stunned that no one said anything. Maggie was unsure how to read the silence, so she continued speaking.
“We feel we should close the shop for two weeks, starting tomorrow,” she said. “The time will be used to repair the restrooms, remodel the break room, and for general cleaning and organizing of the shop floor. We will all work together to accomplish these much-needed tasks. We have hired a few plumbers, electricians, and carpenters. As you may know, these folks are hard to come by, so these specialists have requested some help from us to do the work. I plan to be on the cleaning and painting crew.” As pointed to John, Maggie said, “My fiancé John will work with the plumber, as he worked as a plumber’s assistant while in college.”
John then spoke up: “There is coffee and donuts in the break room for all. We will be there to answer questions.”
Everyone proceeded to the break room, many still stunned by the good news. Expected questions were asked and answered. It was shared with the employees that Ivy Benson Electronics would be offering training for their employees, and even tuition assistance at the local colleges. Maggie and John introduced Chuck Tower as the general manager, and Tanya Brooks as a lead engineer, who would be sharing these duties with Phil Consol.
It took three weeks to prepare Ivy Benson Electronics to be reborn. The new restrooms were immaculate with completely new fixtures and repaired plumbing (Figure 1). The break room was remodeled beautifully. It included vending machines that sold food and drinks at cost, Wi-Fi for smartphones, and two computers for email and web surfing during breaks (Figure 2).
The workers pitched in to create these new changes. When the shop was back up and running, 5S had been implemented at all repair work stations and in the two manufacturing lines. The manufacturing processes were streamlined to eliminate any of the 8 Mudas, and spaghetti diagrams1 were used to minimize wasted motion. From lessons learned in improving productivity and quality at Benson Electronics, the uptime and first pass yield were at 30% and 95%, respectively, soon after production began anew. To support these improvements, Pareto charts were used to track defects and assembly line uptime was measured continuously.
About three months later, things were humming at Ivy Benson Electronics. So many new orders were coming in that Maggie and John had to hire new workers. Employee morale was terrific because of the improvements in the facility, training, and after-work reimbursed education at the local colleges.
Maggie was working in her office when she was startled by the phone ringing.
“Hello, this is Maggie at Benson Electronics. How many I help?” Maggie cheerfully answered.
“This is Ned Price. I wondered if I could meet with you and John and get a tour of what you have done to my factory and the workers?” Ned asked gruffly.
Maggie agreed and suggested they meet at Ivy Benson and then “do lunch.” A few days later, on the appointed day and time, Ned showed up at Ivy Benson. He seemed angry.
“Why don’t you just give me a tour, and I won’t say anything,” Ned began.
Maggie and John were a bit surprised by Ned’s approach but welcomed him into the factory.
“As you can see, we organized the shop floor using 5S and addressing 8 Muda issues. The rework stations all have shadow graphs for the tools, and we have encouraged the staff to keep them neat. We have been impressed with the many helpful suggestions the workers have made to help us achieve an effective workflow,” John said.
“Everyone chipped in and worked with a few plumbers, carpenters, and electricians to update the restrooms, the break rooms, and the basic structure of the two buildings. I think all of us did a lot of painting,” Maggie added with a chuckle.
“We have had several meetings to explain the importance of uptime, quality, and productivity in general,” she continued. “We have daily Pareto charts posted to show yield fallout, and graphs to demonstrate important productivity metrics. We have made a considerable effort to help us understand what makes Ivy Benson productive with quality products.”
As they walked, John told Ned, “We are training the operators to understand how the machines work, and how to operate them most effectively. All operators can be cross-trained on as many machines as they like. We have been really impressed by how enthusiastic the staff has been with these opportunities. On a side note, the solder paste being used was inexpensive, but it had response-to-pause and yield issues, so we replaced it with a more expensive, but better one.”
The one-way chatting continued as they walked to the breakroom. Ned looked around at the new vending machines. His eyes wandered over the low prices. He looked at the two computers. He looked angry.
“We have installed Wi-Fi in the facility for the workers to use during their breaks,” Maggie proudly stated.
They then headed to the restrooms, ensuring they were empty first. Ned glared at the attractive new fixtures and the overall bright, cheery appearance. Neither Maggie nor John knew if he noticed that the bad odor was gone.
As it was obvious that they were finished, Ned began to speak. “You two have ruined my masterpiece! I was determined to deliver to my customers the lowest possible price, and I did it by reducing my costs. You two have gone crazy by spending all this money to make the place look fancy and by coddling the workers. They will just take advantage of you.”
As his face turned red, he continued, “Subsidized vending machines and Wi-Fi? Are you daft? The workers will be in the break room all day goofing off. And educating them? What a joke! These aren’t the kind of people that you educate. When you do, they will just leave for other companies.
“I have a mind to start a new business to take care of my customers since you two have abandoned them,” he finished with rage in his voice.
There was silence for a moment, then John responded, “Our colleague, Frank Emory, has performed a cost and profit analysis of the business when you owned it vs. after we took over. By improving uptime, productivity, and quality, we have reduced our manufacturing costs considerably and have passed some of these savings on to our, not your, customers.”
“We can also show that improving the working conditions and educating the workers has reduced turnover and absenteeism, also reducing costs,” Maggie said. “We forgot to mention that we have a year-end bonus program for the workers that is tied to our profitability. The workers have really bought into it, and it has helped the bottom line.”
Ned Price was beside himself. “You ‘Ivory Tower’ types are all the same. There’s no sense taking me to lunch. You should save the money to offset the losses you will accrue with your big spending practices,” he said.
With that final comment, he huffed and walked out the door. As Maggie and John watched Ned leave, three workers approached them. They looked extremely troubled.
Finally, one spoke. “Is Mr. Price coming back?” Sam Berzinski asked, his chin appearing to quiver.
“No, Sam, Ned Price is not coming back,” John answered. Sam was impressed that John knew his name.
“We’re so relieved,” said Rachel Goodman, another of the three.
“Ever since you took over, we have been excited to come into work,” said Lucy Concha, the third member of the group. “It is so pleasant here, and you and Chuck treat us so well. We all want to work very hard to make Ivy Benson as successful as possible. We are also so grateful for the educational opportunities you have given us. We’ve never been treated so well by an employer in our lives.”
Sam, Lucy, and Rachel chatted for a few more minutes with John and Maggie, and then suggested that they should get back to work.
“How can something so obvious be missed by someone like Ned Price?” John asked Maggie.
“I think I know what you mean, but can you elaborate?” she responded.
“Well, isn’t it obvious that by treating the team at Ivy Benson well and providing good working conditions and opportunities for education, that the company will make the most profit?” John asked.
“And it’s the right thing to do as a human being,” Maggie added.
A bit overcome with emotion by the comments of Sam, Rachel, and Lucy, Maggie was simultaneously reminded of her gratitude for John. How fortunate she was to have such a wonderful life partner. Without thinking, she pulled John toward her, and gave him a substantial kiss. She didn’t care that all the workers cheered.
Stay tuned for the next episode, as Maggie and John visit Maggie’s grandparents to summarize the improvements at Benson and Ivy Benson Electronics.
Note: I imagine many readers are chuckling or groaning as they read how outrageous and non-perceptive Ned Price was. However, Ivy Electronics, before Maggie and John took over, is a composite of several of the assembly facilities I have audited among the scores I have visited worldwide. The descriptions of the restrooms and mistreatment of the people was real. Luckily, there were only a few facilities as described in the last few episodes. Most troubling, however, is that in some parts of the world, educating or training workers is frowned upon. I was involved in several cases where free training was offered and turned down as management was concerned that the newly trained workers would leave and go to competitors.
References
- What is a Spaghetti Diagram?, ASQ.org.
This column originally appeared in the March 2022 issue of SMT007 Magazine.
Download The Printed Circuit Assembler’s Guide to… Solder Defects by Dr. Ronald C. Lasky and Christopher Nash. You can also view other titles in our full I-007e Book library here.
More Columns from Maggie Benson's Journey
Maggie Benson’s Journey: The Journey Was Worth ItMaggie Benson’s Journey: A Lesson From Elon Musk’s Playbook
Maggie Benson’s Journey: It’s Just One of Those Days
Maggie Benson’s Journey: Truth Revealed, Balance Restored
Maggie Benson’s Journey: The Big Reveal
Maggie Benson’s Journey: What Is the Profit Potential?
Maggie Benson’s Journey: A Tale of Two Lawn Mowers
Maggie Benson’s Journey: A ‘Cost of Ownership’ Project