-
- News
- Books
Featured Books
- smt007 Magazine
Latest Issues
Current IssueMoving Forward With Confidence
In this issue, we focus on sales and quoting, workforce training, new IPC leadership in the U.S. and Canada, the effects of tariffs, CFX standards, and much more—all designed to provide perspective as you move through the cloud bank of today's shifting economic market.
Intelligent Test and Inspection
Are you ready to explore the cutting-edge advancements shaping the electronics manufacturing industry? The May 2025 issue of SMT007 Magazine is packed with insights, innovations, and expert perspectives that you won’t want to miss.
Do You Have X-ray Vision?
Has X-ray’s time finally come in electronics manufacturing? Join us in this issue of SMT007 Magazine, where we answer this question and others to bring more efficiency to your bottom line.
- Articles
- Columns
Search Console
- Links
- Media kit
||| MENU - smt007 Magazine
Estimated reading time: 4 minutes
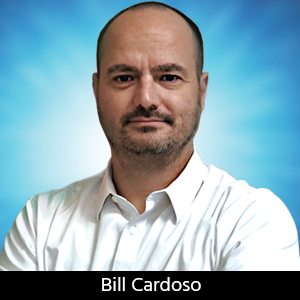
X-Rayted Files: Smart vs. Intelligent SMT Factory
Amazon currently employs over 200,000 robots across 175 fulfillment centers around the world. The robot ranks at Amazon grow every year, and in some facilities, they outnumber the humans. As the lights out concept rapidly grows with the giant retailer, automation adoption still finds resistance in the SMT manufacturing world. I don’t know what the future holds for surface mount technology (SMT) manufacturing, but I’m certain it depends on our intelligence. As a community, we spend a lot of time discussing the Smart factory. Instead, we should aim higher: to the “Intelligent factory.”
Industry 4.0 initiatives that connect the production equipment in the SMT line are critical in the design of a Smart factory. So are smart storage towers or smart stencil storage systems. An Intelligent factory, on the other hand, will connect all these smart pockets inside the factory using an artificial intelligence (AI) engine that will run the factory to optimize efficiency.
Figure 1: Rendering of an automated warehouse.
SMT factories around the world make a wide range of electronic products, from simple toasters to sophisticated avionics. These factories, independent of size, location, or level of sophistication, do one of three things to the materials they receive: move it around, transform it, or store it. Therefore, inside the factory, materials are either being moved, stored, or transformed. An Intelligent factory must be able not only to fully automate all these functions, but also integrate them intelligently.
Figure 2: The SMT line in a Smart factory.
Material transformation is the core of Industry 4.0. It focuses on how materials—in this case electronic components—are transformed as they are assembled onto a printed circuit board (PCB). The SMT line is fully automated today with pick and place machines that can shoot components onto the PCB at warp speeds. Once materials are properly loaded into these machines, no humans are required to enable the transformation performed on these materials from the printer in the beginning of the SMT line to the X-ray machine at the end of the line.
The current evolution in the Smart factory is the automation of material storage. Although the clear majority of SMT factories still rely on miles of shelving space to store electronic components, a few have started to invest in smart storage. In a smart storage system, no human interaction is needed to insert or retrieve reels from shelves. Instead, a robot picks up the reels placed in an entry port and automatically places them on a specially designed shelving system.
Please note that we’re discussing the automation of a single first step in a very complex process. Once robots can move reels from the Smart storage system to the pick and place machine, and from there to an X-ray parts counter, we still need to automate loading and unloading feeders. Currently, we still need a human to place the feeders inside the pick-and-place machine, and to remove them once the run is over.
Figure 3: The SMT line in an Intelligent factory.
With the transformation of materials nearly fully automated, the move from Smart factory to Intelligent factory will focus on the elements of movement of materials as well as material storage. In today’s Smart factories, movement and storage are still largely dependent on people. Intelligent factories will incorporate robotics to reduce or eliminate need for humans to do these tasks. This transformation demands that SMT equipment be designed for human free operation. Developing equipment to interact with material handling robots, for tasks such as feeding components into a pick and place machine or stencils into a printer will take time but will result in SMT lines virtually free of human labor. The same robots that deliver material will return them to storage, where parts counting and communicating inventory levels will be automated.
There will be some key bridges that support the transition from Smart to Intelligent factories. For our part, as X-ray systems manufactures, these will include fully autonomous, AI-enabled inspection systems as well as X-ray parts counters that support smart storage. Autonomous X-ray inspection, when fully integrated into an SMT line, will communicate data used to immediately influence adjustments to process, with or without human intervention. With the pandemic challenging the just-in-time (JIT) approach to inventories, inventory management and parts storage are once again being prioritized. Another knock-on effect of the pandemic has been the labor shortage, and tool such as advanced X-ray parts counters can serve to free talent of the monotony of manual parts counting while improving the accuracy of inventories in real-time.
The enabling technologies described in this article are just a few of the many pieces needed to realize the Intelligent factory. Further, these intelligent factories will no longer be located based on chasing low-cost labor or talent. They will likely look more like a FedEx distribution hub than the factories of today, and supply chain considerations will have as much influence on their location as anything. These are radical changes that will revolutionize the way SMT products are assembled. While a peek inside such a factory will likely be dark, the future of such manufacturing is bright, indeed.
Dr. Bill Cardoso is CEO of Creative Electron.
More Columns from X-Rayted Files
X-Rayted Files: Best Practices in Buying MachinesX-Rayted Files: ’23 and Me?
X-Rayted Files: Battery-Powered Advancements Keep on Ticking
X-Rayted Files: What’s Cooler Than X-ray?
X-Rayted Files: My Favorite BGA Assembly Ever, Part 3
X-Rayted Files: My Favorite BGA Assembly Ever, Part 2
X-Rayted Files: My Favorite BGA Assembly Ever
X-Rayted Files: X-ray Everything!