-
-
News
News Highlights
- Books
Featured Books
- design007 Magazine
Latest Issues
Current IssueAll About That Route
Most designers favor manual routing, but today's interactive autorouters may be changing designers' minds by allowing users more direct control. In this issue, our expert contributors discuss a variety of manual and autorouting strategies.
Creating the Ideal Data Package
Why is it so difficult to create the ideal data package? Many of these simple errors can be alleviated by paying attention to detail—and knowing what issues to look out for. So, this month, our experts weigh in on the best practices for creating the ideal design data package for your design.
Designing Through the Noise
Our experts discuss the constantly evolving world of RF design, including the many tradeoffs, material considerations, and design tips and techniques that designers and design engineers need to know to succeed in this high-frequency realm.
- Articles
- Columns
- Links
- Media kit
||| MENU - design007 Magazine
Microvias Can Be Stacked in Certain Package Densities
October 13, 2022 | I-Connect007 Editorial TeamEstimated reading time: 2 minutes
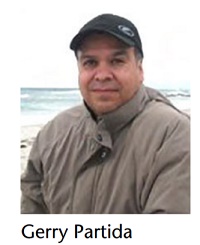
Summit Interconnect’s Gerry Partida recently spoke with the I-Connect007 Editorial Team about his research into root causes of weak microvias. Rather than a single manufacturing process cause, Gerry suggests that microvia reliability is the culmination of several material interactions and that contrary to popular belief, microvias can still be stacked in small, tight packaging densities. He highlights the need for simulation, as well as some of his findings that he plans to publish in a paper at IPC APEX EXPO 2023.
Nolan Johnson: Gerry, I understand your team has been doing some research into microvia stacking and will have a paper at the upcoming IPC APEX EXPO on this topic. What have you been learning?
Gerry Partida: Remember back in the early days of HDI, we would stack microvias as deep and plentiful as we wanted to? Then people started experiencing intermittent failures. Boards got hot, the components would fail, and it went back and forth. Manufacturing did something wrong, the assembler overbaked the boards, and it would go back and forth again. A lot of designs started to suffer, especially certain military products that would stack microvias. We would ask, “Why isn’t it working? Why does it work when it does work?” Most of the microvias that were stacked originally were small BGA packages. They were 0.4 mm or 0.5 mm, and those densities drove you to stack. These designs often were for the commercial OEMs, but if something failed, the commercial guys didn’t come back to discuss the issues.
But for the military guys who have ASICS that cost hundreds of thousands of dollars each, the stakes are much higher. If it is for space, then it can only be assembled once for flight; it cannot be taken off and reused. The military packaging then was a much wider pitch than the commercial guys who were stacking microvias initially.
When we looked at where the failures were happening, they were still happening with the commercial guys who were going three or four deep stacking microvias. They weren’t trying to make short, squatty, wide-diameter microvias because they were using thicker dielectrics to get wider lines for impedance. Consequently, we went for a time where there really didn’t seem to be a problem. Then it became, “We see a fracture at the target pad on the stack of the microvias,” and everybody thought there was a weakness in the electroless copper.
We all came up with these rules of thumb: Don’t stack more than two. A lot of DOEs were done, and they almost always concluded, “Do two stacks, then stagger off.” That seemed to work. Even fabricators we would work with had rules like, “Keep your aspect ratio for a single microvia at 0.75 to one. If you’re stacking them, keep them at 0.6 to one.” That seemed to work; we got good results.
Now, during this time we employed reflow resistance testing to monitor the strength of connections in the finished product. We started learning more about what works, and what doesn’t work. Some designs would slip through, where they do a three-stack on tight pitch, and they were passing. We were asking that if our rule of thumb was only two, then why is it working at three? When you look at the design, it’s a 0.4 mm pitch.
To read this entire conversation, which appeared in the September 2022 issue of PCB007 Magazine, click here.
Suggested Items
The Evolution of Picosecond Laser Drilling
06/19/2025 | Marcy LaRont, PCB007 MagazineIs it hard to imagine a single laser pulse reduced not only from nanoseconds to picoseconds in its pulse duration, but even to femtoseconds? Well, buckle up because it seems we are there. In this interview, Dr. Stefan Rung, technical director of laser machines at Schmoll Maschinen GmbH, traces the technology trajectory of the laser drill from the CO2 laser to cutting-edge picosecond and hybrid laser drilling systems, highlighting the benefits and limitations of each method, and demonstrating how laser innovations are shaping the future of PCB fabrication.
Day 2: More Cutting-edge Insights at the EIPC Summer Conference
06/18/2025 | Pete Starkey, I-Connect007The European Institute for the PCB Community (EIPC) summer conference took place this year in Edinburgh, Scotland, June 3-4. This is the third of three articles on the conference. The other two cover Day 1’s sessions and the opening keynote speech. Below is a recap of the second day’s sessions.
Day 1: Cutting Edge Insights at the EIPC Summer Conference
06/17/2025 | Pete Starkey, I-Connect007The European Institute for the PCB Community (EIPC) Summer Conference took place this year in Edinburgh, Scotland, June 3-4. This is the second of three articles on the conference. The other two cover the keynote speeches and Day 2 of the technical conference. Below is a recap of the first day’s sessions.
Preventing Surface Prep Defects and Ensuring Reliability
06/10/2025 | Marcy LaRont, PCB007 MagazineIn printed circuit board (PCB) fabrication, surface preparation is a critical process that ensures strong adhesion, reliable plating, and long-term product performance. Without proper surface treatment, manufacturers may encounter defects such as delamination, poor solder mask adhesion, and plating failures. This article examines key surface preparation techniques, common defects resulting from improper processes, and real-world case studies that illustrate best practices.
RF PCB Design Tips and Tricks
05/08/2025 | Cherie Litson, EPTAC MIT CID/CID+There are many great books, videos, and information online about designing PCBs for RF circuits. A few of my favorite RF sources are Hans Rosenberg, Stephen Chavez, and Rick Hartley, but there are many more. These PCB design engineers have a very good perspective on what it takes to take an RF design from schematic concept to PCB layout.