-
- News
- Books
Featured Books
- design007 Magazine
Latest Issues
Current IssueProper Floor Planning
Floor planning decisions can make or break performance, manufacturability, and timelines. This month’s contributors weigh in with their best practices for proper floor planning and specific strategies to get it right.
Showing Some Constraint
A strong design constraint strategy carefully balances a wide range of electrical and manufacturing trade-offs. This month, we explore the key requirements, common challenges, and best practices behind building an effective constraint strategy.
All About That Route
Most designers favor manual routing, but today's interactive autorouters may be changing designers' minds by allowing users more direct control. In this issue, our expert contributors discuss a variety of manual and autorouting strategies.
- Articles
- Columns
- Links
- Media kit
||| MENU - design007 Magazine
Estimated reading time: 3 minutes
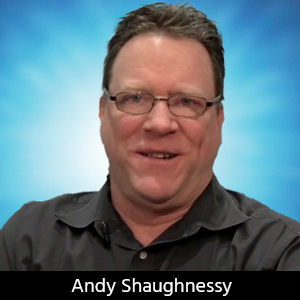
The Shaughnessy Report: A Clearer Image
Out of all the process steps in a fabrication cycle, imaging may be the most critical. This is where the design begins to take a physical shape, where the theoretical world meets the physical world.
Much like photography, PCB imaging is a nearly magical process. I’ll bet the first technologists to use a Gerber Science photoplotter to create a PCB felt a lot like Nicéphore Niépce and Louis Daguerre, trying to coax a Daguerreotype photograph into life in the 1830s.
The primary method of imaging has evolved quite a bit over the last six or seven decades, from screening to liquid photoresist to dry film and then to aqueous dry film. Now laser direct imaging has created a world of possibilities that were unthinkable with film.
Despite all the advantages of direct imaging, the equipment is expensive—nearly seven figures—and there’s no automated DI system for lower-volume fabricators. Nor is there a “turnkey” DI system available yet. You may wind up buying a DI machine from one company and the supporting software from another.
Yes, the “old-school” film imaging systems have a big advantage over DI: They’re completely automated. Will DI ever replace film imaging completely? Probably not in my lifetime.
Some smaller shops may send this job through a 20-year-old etcher. Your system is only as strong as its weakest link; the best imaging process in the world is still dependent on your shop’s printing, etching, plating, and drilling.
Customers are becoming more educated about the capabilities and hurdles related to imaging. They often want to see straight sidewalls, not trapezoidal, that mSAP has made a reality. Straight sidewalls on traces offer a variety of benefits, including interference reduction, and they just look better, don’t they? (Admit it: The beauty contest among your co-workers is real.)
The old axiom says, “It’s all relative.” We’re primarily speaking of the North American fabrication market, which is made up of low- and medium-volume fabricators. These companies are barely an afterthought for the big imaging equipment makers serving the Asian high-volume market. To the big imaging equipment makers, North American fabs are “the little guys.” Keep that in mind.
As we see in this month's issue of PCB007 Magazine, there are still plenty of variables to deal with in imaging, making solid data collection and analysis practices a must. Several of this month’s contributors point out the many ways to get burned by trusting your gut instinct instead of your imaging data. Cost, yield, and quality all depend on a fabricator’s ability to collect and interpret data.
So, in this issue, our experts will discuss ways for the readers to fine-tune their imaging process by understanding how printing, etching, plating, and imaging all work together. We start out with a great interview with Loren Davidson of TTM Chippewa Falls, who explains his medium-volume facility’s imaging processes, and why it’s so important to let the data drive all your decisions. Happy Holden’s column focuses on laser direct imaging—its advantages and its disadvantages. Chris Bonsell of Chemcut discusses how to optimize your etcher for better imaging results. Alexandre Camus, Damien Boureau, and Alexis Guilbert of Altix bring us an article that compares the pros and cons of web and digital imaging systems. And Mivatek’s Brendan Hogan provides the five top priorities for implementing a DI system.
We also have columns from our contributors Travis Kelly, George Milad, Hannah Nelson, Mike Carano, Steve Williams, Christopher Bonsell, and Todd Kolmodin. And don’t miss the interview with Atotech’s Stefan Stefanescu, who discusses the company’s latest suite of control software for wet processes.
We have a busy trade show season coming up. I hope to meet with some of you on the road. See you next month.
Preview or download your PDF copy of the October issue of PCB007 Magazine today!
More Columns from The Shaughnessy Report
The Shaughnessy Report: A Plan for Floor PlanningThe Shaughnessy Report: Showing Some Constraint
The Shaughnessy Report: Planning Your Best Route
The Shaughnessy Report: Solving the Data Package Puzzle
The Shaughnessy Report: Always With the Negative Waves
The Shaughnessy Report: Breaking Down the Language Barrier
The Shaughnessy Report: Back to the Future
The Shaughnessy Report: The Designer of Tomorrow