-
- News
- Books
Featured Books
- design007 Magazine
Latest Issues
Current IssueProper Floor Planning
Floor planning decisions can make or break performance, manufacturability, and timelines. This month’s contributors weigh in with their best practices for proper floor planning and specific strategies to get it right.
Showing Some Constraint
A strong design constraint strategy carefully balances a wide range of electrical and manufacturing trade-offs. This month, we explore the key requirements, common challenges, and best practices behind building an effective constraint strategy.
All About That Route
Most designers favor manual routing, but today's interactive autorouters may be changing designers' minds by allowing users more direct control. In this issue, our expert contributors discuss a variety of manual and autorouting strategies.
- Articles
- Columns
- Links
- Media kit
||| MENU - design007 Magazine
Estimated reading time: 3 minutes
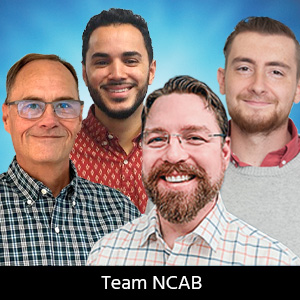
Fresh PCB Concepts: Copper Coin for Dissipating Heat
Are you trying to fit more high-power parts on your board, but can’t find the proper heat management technique? With more high-power components there is a need for increased thermal management. When you’ve tried everything else and are still having trouble keeping your parts within proper operating temperature, copper coin is one of the best ways to dissipate heat throughout your board.
There have been plenty of different solutions that have drawn heat from a component through the board to a heatsink or cold wall. Some of the previous thermal management solutions were heavier copper, via farms, conductive epoxy in holes, IMS, etc. All are effective in their own ways, and some are a bit better at conducting heat or are more cost effective than others. However, these “old” solutions have not been able to keep up with the new high-heat-generating components. The industry came up with a new way to handle heat in the form of copper coin.
When we talk about thermal management, copper coin is the apex. This can be a costly, but very effective solution when it comes to thermal dissipation. This solution is when we’ve exhausted all other options like thermal vias, extra copper plating or filled holes, heatsinks, or IMS. Copper coin attaches the high heat generating components straight to copper, allowing us to draw the heat straight through the copper. Copper is more thermally conductive than most other materials and can be much more efficient than an IMS board with a thermally conductive dielectric. Yes, these materials are attached to aluminum or copper, however, we’re getting capped by our materials in an IMS board. Copper coin allows us to stop using a metal backer to dissipate this heat and we can have more complex designs and real estate on our boards for other less intensive components. This amount of heat reduction can add a lot of life to your chips, and in some cases maybe even double their life span.
It may sound like a simple process, but we’re not just sticking a slab of copper in a board. These coins have to be designed into the board from the very beginning and held within tight tolerances to make sure this works. These coins are typically press-fit into the board so we have to look at the same types of tolerances as we would for press-fit holes. We shouldn’t have all our coins in a straight line down the board either, if there is more than one coin. This can cause the board to crack along the line of the coins. Instead we should have them offset so we can avoid this. Another reason why it’s a good idea is because adding coins on only one side of the board can affect bow and twist; it’s just like not having proper copper balancing in your copper layers, but on a grander scale. Since there would be a heavier amount of copper on one side of the board it would want to bow during fabrication.
When we talk about copper coins we also tend to think of a few different types as well. We have what are called I, T, and U coins. They are shaped exactly how each letter looks in the PCB stack. “I” coin is the simplest: copper surrounded by prepreg in the stack straight through the board. A T coin offers a bit more surface to heatsink or air on the back side of the board while keeping real-estate used on the top to a minimum. A U coin allows for recessed components and allows your heat-generating components closer to your cold wall.
So why turn to copper coin? It is the best source to relieve thermal stress on a board and get as much heat away from those high-power and highly intensive components. This can greatly increase your components’ lifespans; a cool chip is a happy chip. Since it’s an emerging and complex technology, I recommend working with your PCB supplier as early as possible in the design phase.
Nicholas Marks is a quote engineer for NCAB Group.
More Columns from Fresh PCB Concepts
Fresh PCB Concepts: More Than Compliance—A Human-centered Sustainability ApproachFresh PCB Concepts: Assembly Challenges with Micro Components and Standard Solder Mask Practices
Fresh PCB Concepts: The Power of a Lunch & Learn for PCB Professionals
Fresh PCB Concepts: Key Considerations for Reliability, Performance, and Compliance in PCBs
Fresh PCB Concepts: Traceability in PCB Design
Fresh PCB Concepts: Tariffs and the Importance of a Diverse Supply Chain
Fresh PCB Concepts: PCB Stackup Strategies—Minimizing Crosstalk and EMI for Signal Integrity
Fresh PCB Concepts: PCB Plating Process Overview