-
- News
- Books
Featured Books
- design007 Magazine
Latest Issues
Current IssueProper Floor Planning
Floor planning decisions can make or break performance, manufacturability, and timelines. This month’s contributors weigh in with their best practices for proper floor planning and specific strategies to get it right.
Showing Some Constraint
A strong design constraint strategy carefully balances a wide range of electrical and manufacturing trade-offs. This month, we explore the key requirements, common challenges, and best practices behind building an effective constraint strategy.
All About That Route
Most designers favor manual routing, but today's interactive autorouters may be changing designers' minds by allowing users more direct control. In this issue, our expert contributors discuss a variety of manual and autorouting strategies.
- Articles
- Columns
- Links
- Media kit
||| MENU - design007 Magazine
Happy Holden on Gerry Partida’s ‘Significant’ Microvia Reliabilty Paper
December 30, 2022 | Happy Holden, I-Connect007Estimated reading time: 2 minutes
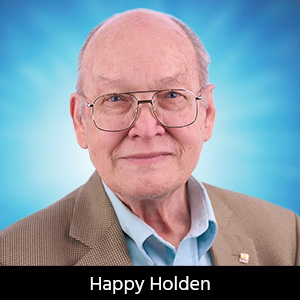
Gerry Partida, vice president of technology at Summit Interconnect, authored a technical paper, “Next Progression in Microvia Reliability Validation—Reflow Simulation of a PCB Design Attributes and Material Structural Properties During the PCB Design Process,” at IPC APEX EXPO 2022, and it’s worth revisiting. This significant paper on microvia reliability validation provides a summary of what’s been happening in the microvia fabrication arena, especially regarding the issue of latent defects in stacked microvias. The paper is available for download here.
Partida offers a thorough look at the controversy initiated in 1996 when latent electrical defects began showing up in field-deployed boards using microvias. My familiarity with this topic dates to 2000, when IPC organized round robin testing of microvia technologies. All looked good, and HDI technology took off. As evolution would have it, the technology grew and diversified. But all the new variants were not necessarily tested like the initial round in 2000.
As Gerry summarizes, “Today, the industry is facing a similar challenge with microvia reliability, especially after reflowing of the PCB at assembly, during rework, or operating in the field. As with the shortcomings of electrical testing in the past, the industry designed PCBs with microvias without evaluating the thermal properties of the material or the geometries in the design. Fabricators produced the finished goods and evaluated the finished PCB to established performance standards such as IPC-6012. When difficult-to-detect failures occurred post assembly, a test method IPC-TM-650 2.6.27 was established and a caution was added to the IPC- 6012 Rev E in Section 3.6, Structural Integrity. The testing of a D coupon via IPC-TM-650 2.6.27 did validate that the finished PCBs were safe for assembly, but it did not stop a fabricator from building a bad design.”
Many studies have shown that the failures seem to be initiated at the interface of the microvia target pad and the plated microvia interface—a plain “butt joint.” As the elevated temperature of lead-free assembly reflow is employed, the stress on this joint exceeds what it can accommodate, unlike tin-lead reflow that occurs at a lower temperature. What caught us unprepared is that after reflowing, the joint appears to be okay and will pass other performance testing, waiting until it fails in the field. This explanation seems to be validated by research that iMEC in Europe has conducted for the European Space Agency. Their finite element analysis of the microvia structure shows the maximum stress at this location and the stress increases as you stack the microvias and increase the temperature.
To read this entire article, which appeared in the November 2022 issue of Design007 Magazine, click here.
Testimonial
"Advertising in PCB007 Magazine has been a great way to showcase our bare board testers to the right audience. The I-Connect007 team makes the process smooth and professional. We’re proud to be featured in such a trusted publication."
Klaus Koziol - atgSuggested Items
SisTech Manufacturing Expands Services: Leading Precision in Electronic Manufacturing
08/11/2025 | Globe NewswireSisTech Manufacturing, known for its expertise in precision electronic manufacturing services, is expanding what it can do in production. For over 30 years, the company has been recognized for its commitment to quality and its ability to meet the diverse demands of industries like aerospace and consumer electronics. With ISO 9001:2015 certification and ITAR registration,
Kaynes Circuits to Invest $570 Million in PCB Tech India’s Tamil Nadu State
08/07/2025 | I-Connect007 Editorial TeamKaynes Circuits India, a subsidiary of Kaynes Technology India, announced on Aug. 4 that it plans to invest roughly $570 million over the next six years in the southern state of Tamil Nadu, the Economic Times reported.
Technica to Host Demo Days Event August 13-14
08/04/2025 | Technica USATechnica USA is proud to announce its upcoming Demo Days Event, taking place August 13–14 at the company’s Demo Center in San Jose, California. The event will feature live demonstrations and presentations from key supply partners ESSEMTEC, INOVAXE, and PARMI showcasing the latest innovations in SMT manufacturing and automation technology.
MacDermid Alpha Electronics Solutions Unveils Unified Global Website to Deepen Customer, Talent, and Stakeholder Engagement
07/31/2025 | MacDermid Alpha Electronics SolutionsMacDermid Alpha Electronics Solutions, the electronics business of Elements Solutions Inc, today launched macdermidalpha.com - a unified global website built to deepen digital engagement. The launch marks a significant milestone in the business’ ongoing commitment to delivering more meaningful, interactive, and impactful experiences for its customers, talent, and stakeholders worldwide.
Federal Electronics Mexico Boosts Speed and Flexibility with New Mycronic A40DX Pick-and-Place
07/23/2025 | Federal ElectronicsFederal Electronics, a leader in providing advanced electronic manufacturing services, has announced a major upgrade at its Hermosillo, Mexico facility with the installation of a Mycronic MYPro A40DX Pick-and-Place system, advancing its surface mount assembly capabilities for high-reliability electronics manufacturing.