-
- News
- Books
Featured Books
- design007 Magazine
Latest Issues
Current IssueProper Floor Planning
Floor planning decisions can make or break performance, manufacturability, and timelines. This month’s contributors weigh in with their best practices for proper floor planning and specific strategies to get it right.
Showing Some Constraint
A strong design constraint strategy carefully balances a wide range of electrical and manufacturing trade-offs. This month, we explore the key requirements, common challenges, and best practices behind building an effective constraint strategy.
All About That Route
Most designers favor manual routing, but today's interactive autorouters may be changing designers' minds by allowing users more direct control. In this issue, our expert contributors discuss a variety of manual and autorouting strategies.
- Articles
- Columns
- Links
- Media kit
||| MENU - design007 Magazine
Estimated reading time: 7 minutes
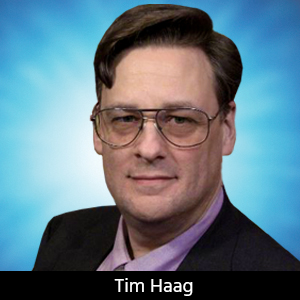
Tim’s Takeaways: Threading the Needle Through Advanced Packaging
Last week, my wife started a new sewing project that required a trip to the craft store for supplies, and she invited me to join her on this errand. This is not the first time I’ve faced this scenario: do I choose to follow her around the craft store pushing the miniature cart that will, by the time we get to the register, barely contain all her chosen fabrics and materials, or stay at home and watch TV? Thankfully, by this point in my life I’ve learned which is the right choice, so we hopped in the car and headed down the road to the craft store.
I’ve been involved in electronics for a very long time now, and I am very familiar with the various manual and automated methods used for PCB design, as well as the different tools and machinery used in their manufacturing. With this background, a simple project using needle and thread should be a cakewalk for me, don’t you think? So—somewhat arrogantly, I must confess—I figured that my wife would ultimately benefit from my experience and expertise when it came to putting her project together.
Boy, do I feel like an idiot now.
The first thing that caught my eye in the craft store was an aisle loaded with assorted tools, where I noticed a selection of cutting instruments. Now I’ve always called them “scissors,” but here was my first lesson of the day: Do you have any idea just how many types of scissors are used when sewing? The type of scissors you’ll need is dependent on whether you are working with small fabrics, embroidery, or double-curved embroidery. Then there are dressmaker shears, pinking shears, and tailor shears. But before we’re done, you also need to know about snips, heavy duty shop snips, applique, and of course, general purpose scissors. It doesn’t stop there. You also need to know when to use serrated blades, non-stick coating, what kind of grip is best, which brands are recommended—and that’s all just for the scissors. We could continue with a discussion on the whole line of rotary cutters, but let’s escape from the sewing tool aisle while we’re still young.
My wife expertly navigated her way through the various areas of the store, choosing between different fabrics, trims, and zippers. Next, she explored several different types and colors of thread, plus the bobbins required to install this thread in her own sewing machine. Buttons and interfacing had to be selected based on color, size, and durability. Just for kicks, we looked at patterns for potential future projects. However, all this took far less time than I would have expected because she had already planned how much fabric she would need, as well as how all the seams, hems, and stitching would be coordinated. Then she said something about a phone, and I thought that we were headed to the Verizon store next. Nope, she meant “foam,” not phone, which was another unique yet crucial component of this project. Would you like me to tell you how many different types, styles, and sizes of foam there are to work with? I didn’t think so.
By the end of the day, I had come to realize that my extremely naïve and rather arrogant perspective on my wife’s sewing was completely out of line. She obviously has just as much—and probably a whole lot more—experience and expertise in the world of sewing as I do in PCB design. After following her around the craft store, I know that I would much rather spend the day puzzling together some complex DDR routing than trying to understand how to sew. But isn’t that the case with most things? There will always be those who have a greater amount of experience and expertise in a specific subject matter. To quote an adage: “There’s always a bigger fish.” An excellent example of this is the advanced packaging of PCB components, and how part selection affects the way we lay out a design.
When I first started designing circuit boards, components were less dense and more generic in both size and shape. I remember being told to leave enough room at the top of my through-hole 14-pin DIPs for a bypass cap. When I asked for the size, shape, or part number, I was told that it wasn’t important; I just needed to create a generic part with a 0.4" x 0.1" rectangle using 62-mil pads spaced 300 mils apart from each other. They (whomever “they” were) would figure out later what to put in there, or they would just leave that part location empty. I wouldn’t recommend using a relaxed component selection technique like that on a next generation smartphone design, as it probably won’t get you many admirers.
Today, there are many component packaging variables that designers must consider when designing a board. Here are a few that come to mind:
- Functionality
- Power
- Price
- Availability
- Component life cycle
- Routability
- Human interface
Depending on the options, designers need to choose the part that will work best for their circuit, but they also must take into account the part’s power needs and thermal issues, as well as whether the board design will support it. Before they can check off component selection on their to-do list, they also need to consider the part’s price and availability, and whether that availability will extend throughout the life of the project. Then they will have to verify that the component’s footprint and density will work with the layer stackup and anticipated routing parameters. Lastly, the ability to manufacture, test, configure, rework, or manipulate the part by technicians and/or end users must also be considered. Yes, there’s a lot to consider when choosing parts, and making a mistake can be costly.
One board that I designed many years ago had a new, unique through-hole connector placed in the middle that spanned almost the complete width of the narrow board being designed. This was a new part, and those that planned the interconnect strategy of the device had carefully chosen the connectors on the different boards for their size and pin density. The plan was to leverage the multiple layers of the board to route out of the connector, as well as to route all the other board traces between its pins. The problem was that the connector specifications called for a pad size that didn’t allow for trace routing between pads, but no one had thought to check on this critical detail when the connectors had been chosen. By the time this design got into my hands, the mating connector had already been built into the other boards in the device—we were stuck. If memory serves, I think that we had to get a special exemption from our manufacturers just to build the board.
This story illustrates the importance of not only choosing the correct component for the application, but also the critical need for expertise in advance component packaging; without advanced packaging know-how, designers can’t understand all the aspects and implications of using a new part. As I said earlier, component selection mistakes can end up being very costly in terms of manufacturing expenses and board failures. Yet as new and increasingly advanced PCB components become available, making these kinds of mistakes becomes more likely. While we would all do well to learn as much about component engineering as possible, it’s important to identify resources that can help us understand the latest developments in advanced packaging and how they might affect component selection. One such resource is your circuit board manufacturer, who often has a full-time staff of component engineers to ensure that the best possible part choices are being made for their customers. Also, this edition of Design007 Magazine is full of insights from leaders in the PCB component packaging field on new technologies and how to make the best part choices.
The moral of the story is to not be ashamed to admit when you need help, especially when it comes to PCB component selection. It may very well save you a lot of time, grief, and expense in the end. Today’s advanced parts include high-density, fine-pitch BGAs that demand a well-thought-out layer stackup and routing strategy long before they are ever placed on the board. Just as my wife knew exactly what she needed from the craft store before she even got in the car, PCB designers need to know just how much we can and can’t do with the parts in our designs—before we go to layout.
Until next time, keep on designing.
This column originally appeared in the January 2023 issue of Design007 Magazine.
More Columns from Tim's Takeaways
Tim’s Takeaways: One for the ArchivesTim’s Takeaways: The Art of Technical Instruction
Tim’s Takeaways: PCB Design and Manufacturing—Let’s Work Together
Tim’s Takeaways: Take It From Scotty, Simple Really is Better
Tim’s Takeaways: Human Ingenuity and the Rigid-flex PCB
Tim’s Takeaways: How I Learned Advanced Design Strategies
Tim’s Takeaways: Batter Up—Stepping Up to the Substrate
Tim’s Takeaways: Tribal Knowledge—Not the Villain You Thought