-
- News
- Books
Featured Books
- smt007 Magazine
Latest Issues
Current IssueSupply Chain Strategies
A successful brand is built on strong customer relationships—anchored by a well-orchestrated supply chain at its core. This month, we look at how managing your supply chain directly influences customer perception.
What's Your Sweet Spot?
Are you in a niche that’s growing or shrinking? Is it time to reassess and refocus? We spotlight companies thriving by redefining or reinforcing their niche. What are their insights?
Moving Forward With Confidence
In this issue, we focus on sales and quoting, workforce training, new IPC leadership in the U.S. and Canada, the effects of tariffs, CFX standards, and much more—all designed to provide perspective as you move through the cloud bank of today's shifting economic market.
- Articles
- Columns
- Links
- Media kit
||| MENU - smt007 Magazine
Estimated reading time: 4 minutes
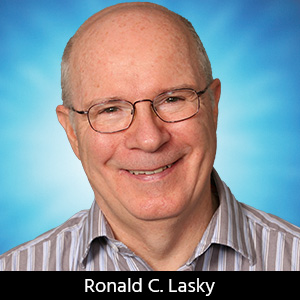
Maggie Benson’s Journey: Fair and Square
Editor’s note: Indium Corporation’s Ron Lasky continues this series of columns about Maggie Benson, a fictional character, to demonstrate continuous improvement and education in SMT assembly.
Let’s look in on Andy Connors, Sue March, and Chuck Tower at Castellanos Electronics after Maggie and John’s decision to buy the company.
Maggie and John have asked Andy, Sue, and Chuck to join them in a Zoom meeting to discuss the details of their recent purchase of Castellanos Electronics. The meeting appeared to be winding down when Maggie asked Andy and Sue about their summer plans.
“It’s only early June and your part-time classes at Ivy U don’t start until early September, right?” Maggie asked. “Can you two stay onsite and help us with the transition?”
Andy gave Sue a questioning look. He was about to say that he and Sue needed to talk it over when Sue suddenly grabbed his hand. “We would love to,” she said excitedly.
Andy and Chuck looked at each other and burst out laughing.
“What?” Sue asked, unsure why agreeing to help was so funny.
“Ah, you might have asked Andy’s opinion,” Chuck teased.
“Oops, sorry honey,” Sue replied sheepishly.
Even though they were engaged, Andy melted every time Sue referred to him with an endearment. “It’s okay,” he said, “I’m just as excited as you are about staying here.”
After hopping off the call, Andy, Sue, and Chuck began developing a plan. Chuck would stay a few days to perform a thorough audit of the entire operation and develop a suggested continuous improvement plan. Andy would work with José to identify four people who, with the proper training, had the potential to become fully-fledged process engineers. Andy would oversee developing and executing that training. Eventually, these engineers would have the capability to set up lines for new jobs and, essentially, run the factory if José was not there. Sue decided that she would help Carlos develop a plan to address the defects identified in the Pareto chart the two of them had made together (Figure 1).
Once everyone was clear on their tasks, Sue met with Carlos.
“Carlos, we’ve identified graping as the most common defect,” Sue said. “Who would be the best person to discuss this with?” Carlos answered that she should meet with Miguel Santos, so together they found Miguel at his desk.
“How can I help?” Miguel asked, once everyone had introduced themselves.
Sue explained that she and Carlos had identified graping as the company’s biggest quality issue, and she wanted to discuss how to minimize it (Figure 2).
“Sue, can you explain how graping happens?” Miguel asked.
“Sure,” she said. “Graping occurs when the oxygen barrier in the solder paste is exhausted. This situation can occur for a few different reasons. The major reason for graping is that the printed solder paste deposit is too small. Because the deposit is so small, it has too much surface area-to-volume ratio, which exhausts the oxygen barrier materials in the flux—meaning they can no longer protect the solder particles from oxidation. Once solder particles oxidize, graping can occur. Graping usually occurs on solder joints that were printed with circular apertures for BGA components—is that correct, Carlos?”
“Si, señorita,” Carlos responded.
Sue continued, “Printing square apertures provides about 25% more surface area, hence 25% more paste volume. However, experiments1 have shown that square apertures also enable improved transfer efficiency over circular apertures. It is believed that this is due to the curvature of the circular aperture, which makes the solder paste adhere more to the stencil than the pad. If we change the stencil apertures to square, the problem might go away.”
To illustrate her point, Sue pulled out a couple photos showing the differences between reflowed solder deposits from both circular and square apertures (Figure 3).
Miguel seemed impressed. “Wow, that is a dramatic difference,” he said.
“I see your PWB pads are solder mask defined, and that helps keep the solder paste flux from flowing away, which is a good thing,” Sue said. “In addition, the reflow profile is a ramp-to-peak, which also minimizes graping. So, my hope would be that changing from circular to square apertures might solve the problem1.”
Meanwhile, Andy was meeting with José and the four process engineer candidates: Juan, Santiago, Jesús, and María. José explained to the group that Andy wanted to train the candidates to become process engineers. The training would be voluntary and would be performed on overtime, so the candidates would be adequately compensated for their time. All four looked nervous. José had selected them because they had worked at the company for more than five years, were all good employees, had good attitudes, and most importantly, were eager to learn.
“What if we’re not smart enough?” Santiago asked anxiously.
“Andy and I discussed what you would need to learn and I’m confident all of you can do it. You are all high school graduates, know how to run almost all the equipment, are good at math, and most importantly, you’re all curious and interested in learning new things,” José answered.
“How do you know we are good at math?” María asked.
“Because, at one time or another, each of you has asked me either how line balancing or reflow throughput is calculated. After showing you how to do those calculations, I’ve asked you to perform them on numerous occasions, and you’ve always gotten them right,” José responded.
Will square apertures fix the graping problem? How will Andy prepare these new process engineers for success? Stay tuned to find out.
References
-
Square vs. Circular Apertures and the Five Ball Rule Revisited,” by Ron Lasky, hotwires.net.
-
For more details on minimizing graping, see The Printed Circuits Assemblers Guide to... Solder Defects, by Christopher Nash and Dr. Ronald C. Lasky, 2021.
This column originally appeared in the January 2023 issue of SMT007 Magazine.
More Columns from Maggie Benson's Journey
Maggie Benson’s Journey: The Journey Was Worth ItMaggie Benson’s Journey: A Lesson From Elon Musk’s Playbook
Maggie Benson’s Journey: It’s Just One of Those Days
Maggie Benson’s Journey: Truth Revealed, Balance Restored
Maggie Benson’s Journey: The Big Reveal
Maggie Benson’s Journey: What Is the Profit Potential?
Maggie Benson’s Journey: A Tale of Two Lawn Mowers
Maggie Benson’s Journey: A ‘Cost of Ownership’ Project