-
- News
- Books
Featured Books
- design007 Magazine
Latest Issues
Current IssueShowing Some Constraint
A strong design constraint strategy carefully balances a wide range of electrical and manufacturing trade-offs. This month, we explore the key requirements, common challenges, and best practices behind building an effective constraint strategy.
All About That Route
Most designers favor manual routing, but today's interactive autorouters may be changing designers' minds by allowing users more direct control. In this issue, our expert contributors discuss a variety of manual and autorouting strategies.
Creating the Ideal Data Package
Why is it so difficult to create the ideal data package? Many of these simple errors can be alleviated by paying attention to detail—and knowing what issues to look out for. So, this month, our experts weigh in on the best practices for creating the ideal design data package for your design.
- Articles
- Columns
- Links
- Media kit
||| MENU - design007 Magazine
PCB Designers Are Really Product Designers
February 9, 2023 | Zachariah Peterson, NWESEstimated reading time: 2 minutes
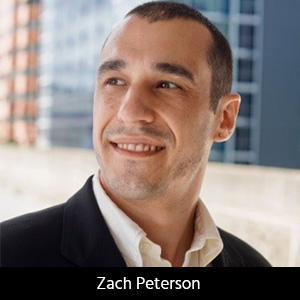
As I look back on 2022, I’m realizing that my company plays multiple roles in client projects beyond just designing circuits and PCBs. Sure, we’re primarily a PCB design company, but we also help with things that happen outside the PCB. This includes tasks like enclosure design, defining mechanical constraints, simulating electrical behavior, mating boards into larger assemblies, selecting cabling, and defining test requirements, all of which slowly creep into the standard scope of work for design projects.
The same set of tasks have crept into CAD software features, especially in the PCB design space. Both mechanical design tools and PCB design software have expanded their capabilities beyond enclosure/fixture design and board layout, respectively. Looking at some of the capabilities in a platform like Fusion 360, the MCAD side has significantly outpaced the ECAD side.
In the ECAD/EDA world, we still focus mostly on simulation and fit to enclosure, but there is so much more that goes into full-scale product development, and the ECAD software world should start to move much faster toward the goals I outline below.
What PCB Designers Need for Product Development
As I mentioned in my earlier I-Connect007 article on simulation, designers need much simpler simulation access either inside their native PCB design tool or through a direct and seamless integration with another design/simulation program1. Now that ECAD/MCAD collaboration has helped bring electrical and mechanical co-design under one roof, designers can instantly pass ECAD data into the MCAD system and vice versa.
What else can the ECAD industry do to support product design? Based on both my personal experience with client projects and current ECAD industry trends, here are some things I’d love to see.
Cable and Harness Design
This area is finally coming to fruition from my preferred EDA vendor, and I expect similar features from others. Many products, whether they are multi-board assemblies or requiring a connection to an external product, may do so with custom cables, custom or standard mated connectors, or flex ribbons.
Harness and cable definition at the logic level, visual integration into the assembly, and even physical design of custom cable assemblies—these are all essential parts of product development. The immediate benefit is in MCAD, where the connector and cable can be viewed in a larger system. However, the broader benefit is in simulation and rules checking, where logical definitions in interconnects are used to examine electrical behavior.
To read this entire article, which appeared in the January 2023 issue of Design007 Magazine, click here.
Suggested Items
Digital Twin Concept in Copper Electroplating Process Performance
07/11/2025 | Aga Franczak, Robrecht Belis, Elsyca N.V.PCB manufacturing involves transforming a design into a physical board while meeting specific requirements. Understanding these design specifications is crucial, as they directly impact the PCB's fabrication process, performance, and yield rate. One key design specification is copper thieving—the addition of “dummy” pads across the surface that are plated along with the features designed on the outer layers. The purpose of the process is to provide a uniform distribution of copper across the outer layers to make the plating current density and plating in the holes more uniform.
Meet the Author Podcast: Martyn Gaudion Unpacks the Secrets of High-Speed PCB Design
07/10/2025 | I-Connect007In this special Meet the Author episode of the On the Line with… podcast, Nolan Johnson sits down with Martyn Gaudion, signal integrity expert, managing director of Polar Instruments, and three-time author in I-Connect007’s popular The Printed Circuit Designer’s Guide to... series.
Showing Some Constraint: Design007 Magazine July 2025
07/10/2025 | I-Connect007 Editorial TeamA robust design constraint strategy balances dozens of electrical and manufacturing trade-offs. This month, we focus on design constraints—the requirements, challenges, and best practices for setting up the right constraint strategy.
The Shaughnessy Report: Showing Some Constraint
07/14/2025 | Andy Shaughnessy -- Column: The Shaughnessy ReportWhen we first decided to cover strategies for setting PCB design constraints, one designer we spoke with said, “They’re not really constraints; they’re more like guardrails that prevent your design from going off a cliff.”
Elementary, Mr. Watson: Rein in Your Design Constraints
07/10/2025 | John Watson -- Column: Elementary, Mr. WatsonI remember the long hours spent at the light table, carefully laying down black tape to shape each trace, cutting and aligning pads with surgical precision on sheets of Mylar. I often went home with nicks on my fingers from the X-Acto knives and bits of tape all over me. It was as much an art form as it was an engineering task—tactile and methodical, requiring the patience of a sculptor. A lot has changed in PCB design over the years.