-
- News
- Books
Featured Books
- smt007 Magazine
Latest Issues
Current IssueSupply Chain Strategies
A successful brand is built on strong customer relationships—anchored by a well-orchestrated supply chain at its core. This month, we look at how managing your supply chain directly influences customer perception.
What's Your Sweet Spot?
Are you in a niche that’s growing or shrinking? Is it time to reassess and refocus? We spotlight companies thriving by redefining or reinforcing their niche. What are their insights?
Moving Forward With Confidence
In this issue, we focus on sales and quoting, workforce training, new IPC leadership in the U.S. and Canada, the effects of tariffs, CFX standards, and much more—all designed to provide perspective as you move through the cloud bank of today's shifting economic market.
- Articles
- Columns
- Links
- Media kit
||| MENU - smt007 Magazine
Estimated reading time: 5 minutes
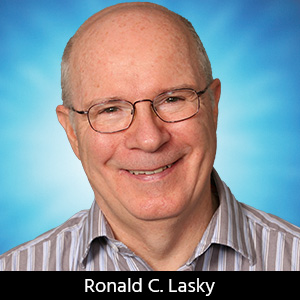
Maggie Benson’s Journey: Slow and Steady is Still Progress
Editor’s note: Indium Corporation’s Ron Lasky continues this series of columns about Maggie Benson, a fictional character, to demonstrate continuous improvement and education in SMT assembly.
We continue to look in on Andy Connors, Sue March, and Chuck Tower at Castellanos Electronics after Maggie and John’s decision to buy the company. Sue is working on minimizing defects that have been categorized in a Pareto chart1, whereas Andy is working on a training program to develop some process engineers, and Chuck is performing an audit to identify and improve uptime and profitability.
Chuck has called a meeting with Andy and Sue to assess their progress.
“Well, the audit I performed went quite well,” Chuck began. “As we thought, there are possible improvements in uptime. I’m also suggesting a different solder paste, as the one they have has poor response-to-pause2.”
“It always surprises me that there are people who choose to use a paste that hurts uptime and yields just to save a few pennies per gram,” Andy commented.
“Yeah, then they lose tens of thousands of dollars in productivity and yields,” Chuck said. “So that’s something to address. I have to admit, though, that as José and I worked on developing an action plan to improve other aspects of the processes, I was quite impressed with their starting point. Unfortunately, I’m going home tomorrow, so Andy, could you work with José on the action plan?”
“Sure thing, boss!” Andy replied jokingly.
Sue sensed it was her turn to share. “Well, Carlos and I developed a Pareto chart of the defects (Figure 1). We started working on the graping issue first. They were using circular apertures for BGAs, so I recommended switching to square apertures. Fortunately, their stencil vendor is in town, so they got new stencils and we already have quite a bit of data. It looks like the square apertures have significantly reduced graping, but I don’t know the details yet. Next, we are going to work on the head-in-pillow (HIP) defect.”
Satisfied with Sue’s progress, Chuck then turned to Andy and asked, “What about the training plan to help some of the workers become process engineers?”
“José identified four potential candidates,” he replied. “After discussing it, we think the people should become SMTA-certified process engineers3. They will need a lot of preparation, so I am developing a workshop using the Handbook of Electronic Assembly (Figure 2)4. I plan to give them a lot of exercises to improve their confidence. This teaching project and the process improvement action plan will keep me busy for the rest of the time Sue and I are here.”
“Sue, I can see you have your hands full working through the defects identified in the Pareto chart,” Chuck said, and with that, the meeting was over. Sue decided to tackle her project right away, so she went to find Carlos to start working on reducing HIP defects.
“Carlos, let’s find Miguel and discuss a plan to reduce HIP defects,” Sue said. José had appointed Miguel to be the point person on working on defect minimization. They soon found him and got to work.
“Señorita Sue, can you tell us what typically causes the HIP defect?” Miguel asked.
“Absolutely,” Sue said. “The basic failure mechanism occurs in predominantly ball grid array packages. During the assembly process, as the circuit board and ball grid array go through the reflow oven, they can often move relative to each other because of thermal warping of the circuit board and ball grid array package. Sometimes, they'll separate during the reflow process: the solder paste will reflow separately from the ball and a solder connection will not be formed.” (Figure 3).
“So, what can we do to minimize HIP defects?” Miguel asked.
“We want to assure that we have a nice, tall stencil-printed solder paste deposit so that we're getting good definition in our printing rather than having hot slump during reflow, which can also be an issue,” Sue said. “We want to make sure that the pick-and-place machine is placing the ball squarely on the pad, not off to the side. It helps to have a solder paste that has a little stringiness to it, so that if the circuit board pad and solder ball do separate, the solder paste will still stick them back together. In these types of situations, an “oxidation barrier” in the solder paste helps in the reflow process, too. The new solder paste that we will be buying to reduce response-to-pause issues also has good HIP resistance. So, that should help a lot.”
“Will the new square apertures also help?” Carlos asked.
“That’s a good point. Having more solder paste in the print is definitely a good thing,” Sue answered.
“Miguel, can you check the printing to make sure we don’t have hot slump, and that the placement machines are placing the BGAs squarely?” Sue asked, as he replied, “Sí, señorita Sue.”
As they were wrapping up, Sue asked, “Carlos, do we have any data on graping since we switched to square apertures?”
“Sí, señorita Sue, graping defects are down by 95%,” Carlos answered.
“Terrific,” said Sue and Miguel in unison.
At the end of the meeting, Sue gave each man a chaste hug. They both turned red and looked like they might swoon…
Will the HIP decrease? What will Andy teach in his SMTA certification preparation classes? Will you be able to answer some of Andy’s quiz questions? Stay tuned to find out.
References
- “Pareto chart,” Wikipedia.org, Sept. 17, 2022.
- “Response to Pause: A Critical Solder Paste Parameter,” by Ron Lasky, Indium Corporation, Indium.com, Aug. 21, 2019.
- “SMTA: Certification,” SMTA.org.
- Handbook of Electronic Assembly and A Guide to SMTA Certification, by Ron Lasky et. al, SMTA Publishing.
This column originally appeared in the February 2023 issue of SMT007 Magazine.
Download The Printed Circuit Assembler’s Guide to… Solder Defects by Christopher Nash and Dr. Ronald C. Lasky. You can also view other titles in our full I-007eBooks library.
More Columns from Maggie Benson's Journey
Maggie Benson’s Journey: The Journey Was Worth ItMaggie Benson’s Journey: A Lesson From Elon Musk’s Playbook
Maggie Benson’s Journey: It’s Just One of Those Days
Maggie Benson’s Journey: Truth Revealed, Balance Restored
Maggie Benson’s Journey: The Big Reveal
Maggie Benson’s Journey: What Is the Profit Potential?
Maggie Benson’s Journey: A Tale of Two Lawn Mowers
Maggie Benson’s Journey: A ‘Cost of Ownership’ Project