-
- News
- Books
Featured Books
- design007 Magazine
Latest Issues
Current IssueProper Floor Planning
Floor planning decisions can make or break performance, manufacturability, and timelines. This month’s contributors weigh in with their best practices for proper floor planning and specific strategies to get it right.
Showing Some Constraint
A strong design constraint strategy carefully balances a wide range of electrical and manufacturing trade-offs. This month, we explore the key requirements, common challenges, and best practices behind building an effective constraint strategy.
All About That Route
Most designers favor manual routing, but today's interactive autorouters may be changing designers' minds by allowing users more direct control. In this issue, our expert contributors discuss a variety of manual and autorouting strategies.
- Articles
- Columns
- Links
- Media kit
||| MENU - design007 Magazine
Estimated reading time: 3 minutes
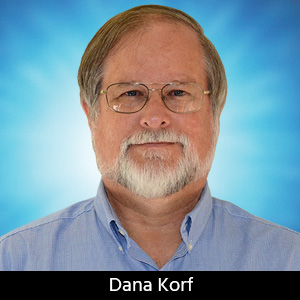
Dana on Data: Are You Ready for 3D AME?
Editor's note: This month's column was written as a collaboration with Volkan Efe, director, RF applications with Nano Dimension.
The PCB interconnect revolution has started. We are no longer constrained to X/Y trace routing with large drilled vias and pads connecting individual horizontal routing layers. Why be constrained with a trapezoidal trace? Why not route with twisted pairs or a coax interconnect? Additively manufactured electronics (AME) eliminates the need for through, blind, and buried vias by replacing them with a trace at non-vertical angles.
What’s holding this implementation up?
Despite numerous technological advancements in recent years, the printed circuit board (PCB) design and production industry has remained relatively unchanged for decades. The introduction of plated through-holes, blind and buried laser vias, and flexible PCBs were some of the notable improvements, but the fundamental process of creating and producing circuit boards has remained largely the same. It’s time to let additive manufacturing technology assist in advancing the PCB industry.
With the growing demand for electronics that are faster, more efficient, and environmentally sustainable, it is becoming increasingly evident that this stagnant state is no longer adequate. We would like to explore the reasons behind the PCB industry's slow adoption of new technologies and the potential benefits of embracing innovation.
The hesitation to change in the PCB industry can be attributed to a few factors. Firstly, traditional methods of PCB design and production have been utilized for a considerable amount of time, and many individuals and companies in the industry have extensive expertise in these methods. As a result, there is a resistance to change, particularly among those who have invested a significant amount of time and effort in mastering traditional techniques. We had long conversations with many folks about this resistance to change at the latest IPC APEX EXPO.
Another reason for the unwillingness to change is the cost associated with transitioning to innovative technologies and methods. Adopting new technologies often requires a substantial investment in both equipment and training, and many companies are hesitant to make such investments without a clear understanding of the benefits and risks. Moreover, the process of transitioning to new methods can be complex and time-consuming, and companies are concerned about the possible disruption to their operations and production processes.
Finally, the lack of standardization in the alternative manufacturing technologies also contributes to the reluctance of the PCB industry to embrace them. For example, despite its many advantages, there is still some uncertainty about the reliability and consistency of additively manufactured printed circuit boards, and many companies prefer to wait until these concerns are fully addressed before relying on the technology.
Several actions are underway to expedite the transition into more innovative, sustainable, and cost-efficient PCB manufacturing through AME.
Education and awareness: Industry professionals need education and training on the potential and benefits of additive technologies, and how they can be integrated into their work processes. Design guides and training classes require development both to re-train existing industry experts, and also to expose AME to new students.
Industry standards: Clear and consistent standards need to be established for the use of AME technologies in the PCB industry, including guidelines for quality control, production processes, data formats, and safety, in order to ensure that fully additive 3D circuit boards are reliable and consistent, and to increase confidence in the technology.
Government support: Governments should encourage the adoption of AME technologies by providing funding for research and development and offering tax incentives for companies to invest in the technology.
Partnership and collaboration: Partnerships and collaboration between companies in the PCB manufacturing and design industry and those in the additive manufacturing industry need to be encouraged. There are many novel routing strategies and formed component types yet to be developed or invented.
Investment in equipment: A key factor is the investment in high-quality equipment and software to ensure that companies have the resources they need to fully take advantage of the benefits of additive technologies.
The demand for faster, more efficient, and environmentally sustainable electronics is increasing, and the PCB industry must adapt to this change by fully adopting and integrating innovative technologies such as additive manufacturing of circuit boards. Additive manufacturing has the potential to offer miniaturization, weight reduction, and design freedom, leading to the creation of more compact and efficient electronic devices with improved functionality and reduced environmental impact.
The industry faces challenges in overcoming resistance to change, including traditional methods, cost and complexity of transition, and lack of standards. To move towards a more innovative and efficient future, the PCB industry needs to educate professionals, establish standards, receive government support, foster partnerships, and invest in equipment.
“To infinity, and beyond!” —Buzz Lightyear in Disney’s animated film “Toy Story.”
Dana Korf is AME standards manager at Nano Dimension.
More Columns from Dana on Data
Dana on Data: Best Practices in Interpreting Drawing Notes—‘Use Latest Revision’Dana on Data: The Missing AI-NPI Link
Dana on Data: Merging 2D Electrical, 3D Mechanical Worlds
Dana on Data: Resurrecting IPC Class 1
Dana on Data: The Evolution of Fabrication Drawing
Dana on Data: The Insane PCB DFM Process
Dana on Data: eCAD PCB Design Deficiencies
Dana on Data: Nuke the Netlist