-
- News
- Books
Featured Books
- design007 Magazine
Latest Issues
Current IssueProper Floor Planning
Floor planning decisions can make or break performance, manufacturability, and timelines. This month’s contributors weigh in with their best practices for proper floor planning and specific strategies to get it right.
Showing Some Constraint
A strong design constraint strategy carefully balances a wide range of electrical and manufacturing trade-offs. This month, we explore the key requirements, common challenges, and best practices behind building an effective constraint strategy.
All About That Route
Most designers favor manual routing, but today's interactive autorouters may be changing designers' minds by allowing users more direct control. In this issue, our expert contributors discuss a variety of manual and autorouting strategies.
- Articles
- Columns
- Links
- Media kit
||| MENU - design007 Magazine
Estimated reading time: 5 minutes
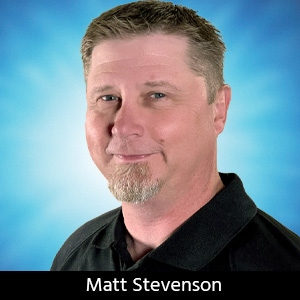
Connect the Dots: Top 5 High-profile Activities for Production Excellence
Editor's note: Kevin Beattie is a guest columnist this month. He is a quality assurance manager at Sunstone Circuits.
For electronics manufacturers, consistently producing quality products is the baseline for success. Even as pressures created by supply chain disruptions and labor scarcity persist, organizations need to focus on continuous improvement to remain competitive.
In this effort, manufacturers should challenge themselves by constantly seeking to make operations run better, increase profitability, and improve the customer experience. By focusing on activities that move the performance needle, organizations can attain a higher state of production excellence.
Identifying High-payoff Activities
What exactly is a high-payoff activity (HPA)? HPAs are activities that directly improve processes, enhance best practices, and evolve the production facility to the next level of production excellence.
HPAs fall into five categories. They are:
- Safety
- Quality
- On-time delivery
- Cost reduction/efficiency gain
- Continuous improvement
When deployed, these five types of HPA can improve production performance.
Safety
Safety should be the top priority for every PCB manufacturer. Protecting employees on the production floor is not only the right thing to do, but it is also a business best practice. Employees are happier and more productive working in a safe workspace, using safe processes, and operating throughout the day under an umbrella of safety.
Engineering controls to error-proof (Poka-Yoke) safety standards can be utilized to attain a higher level of safety and decrease the probabilities of injuries. Common examples of error-proofing in manufacturing include:
- Interlock door switches on machine doors, so the machine will not run with the door open
- Using a self-retractable box knife which automatically retracts the knife when not in use
- Fixing uneven production floors to avoid slips, trips, and falls
Chemical processes play a big role in PCB manufacturing, and establishing exceptional standards for proper use of personal protective equipment (PPE) can improve the safety of a working environment. Goggles, face shields, aprons, gloves, and chemical boots are common forms of PPE used on the production floor. When choosing PPE equipment, manufacturers should make sure it is impermeable to the chemicals being used.
Ongoing training of both new and current employees is perhaps the most important aspect of ensuring safety on the production floor. Training should be diverse and comprehensive, covering everything from proper lifting techniques to electrical safety.
Quality
Quality is about more than quality products. It should be top of mind with respect to every aspect of production. The quality cycle really begins with process development and evaluation. Manufacturers need to scrutinize production output data in search of process variances. This will help to determine where in the manufacturing cycle process that quality output meets or exceeds expectations.
There are several tools available to control production quality. They include:
- DMAIC (Define, Measure, Analyze, Improve, and Control) refers to a five-step, data-driven improvement cycle aimed at improving, optimizing, and stabilizing operational processes
- SPC (Statistical Process Control) is a quality control method used by manufacturers to maximize efficiency and minimize waste
- FMEA (Failure Mode and Effects Analysis) can be employed to create a known production quality output
Quality does not begin and end with the production process. It should be embedded in the organization’s culture and a priority for everything from the overall customer experience to individual elements of employee relations such as training or incentive programs.
On-Time Delivery
Quality products do not arrive late. The first thing customers ask during the quote process is often, “When can I expect delivery?” PCB manufacturers are often among the most mission-critical supply chain components for producers of electronic products. This means manufacturers must understand with great accuracy every component of their production process before committing to a shipping due date.
Every manufacturer strives for perfection, 100% on-time, all the time. If an organization is not at 100%, improvement is possible. To ensure on-time delivery, manufacturers should focus on the following:
- Process the order correctly the first time. Customers won’t wait for a supplier to build an order twice.
- Know the capacity limitations of the facility. Correlate capacity level to the volume and timing of customer orders, paying particular attention to where the largest constraints are located in the production process.
- Continuously learn to overcome processing challenges using root cause analysis. This will make order processing less variable, more predictive, and less constrained.
Cost Reduction/Efficiency Gain
Efficiency gains and cost reductions sound like the same thing, but they are more like two sides of the same coin.
- Cost reduction is measured by use of fewer consumables
- Efficiency gains are the result of utilizing less labor
To improve at both, manufacturers need meaningful, granular metrics in place to measure how much of each is being used.
The metrics for raw materials consumed during production should be in the purview of the accounting and finance team. They can set metrics for the volume of consumables used during production. How those materials are used on the production floor requires analysis of manufacturing processes. Once an organization has a clear vision of how and how much of a raw material is being used, then strategies and best practices for cost reduction can be put into place.
The process for making efficiency gains is similar to material cost reduction initiatives. It is essential to understand labor costs at a granular level, including how process and technology impact operational efficiency down to the individual level. When a facility learns how to increase output at the per person level, the opportunities for improvement increase substantially.
Continuous Improvement
Continuous improvement is arguably the most important of the five HPAs.
Repeatedly challenging the status quo with an eye toward improvement will keep production excellence at its highest level. Manufacturers who adopt continuous improvement programs and implement quality management systems (QMS) will realize improvement efforts across the production floor.
Common elements of successful continuous improvement programs include:
- Utilize Lean Six Sigma, 5S, and 5-Why root cause analysis.
- Perform daily process walks, known as Gemba in the Lean manufacturing philosophy. These provide daily observation of processes occurring in real time and can uncover resource gaps.
- Plan-Do-Check-Act (PCDA) is a method to both continually improve and measure results—setting the stage for solid countermeasures that will prevent reoccurrence of an observed weakness or gap in the process.
Putting the five HPAs into practice on a daily basis into any production process will help keep any production team laser-focused on achieving production excellence through the continual improvement cycle.
This column originally appeared in the April 2023 issue of Design007 Magazine.
More Columns from Connect the Dots
Connect the Dots: How to Avoid Five Common Causes of Board FailureConnect the Dots: Sequential Lamination in HDI PCB Manufacturing
Connect the Dots: The Future of PCB Design and Manufacturing
Connect the Dots: Proactive Controlled Impedance
Connect the Dots: Involving Manufacturers Earlier Prevents Downstream Issues
Connect the Dots: Stop Killing Your Yield—The Hidden Cost of Design Oversights
Connect the Dots: Designing for Reality—Routing, Final Fab, and QC
Connect the Dots: Designing for Reality—Surface Finish