-
- News
- Books
Featured Books
- pcb007 Magazine
Latest Issues
Current IssueInventing the Future with SEL
Two years after launching its state-of-the-art PCB facility, SEL shares lessons in vision, execution, and innovation, plus insights from industry icons and technology leaders shaping the future of PCB fabrication.
Sales: From Pitch to PO
From the first cold call to finally receiving that first purchase order, the July PCB007 Magazine breaks down some critical parts of the sales stack. To up your sales game, read on!
The Hole Truth: Via Integrity in an HDI World
From the drilled hole to registration across multiple sequential lamination cycles, to the quality of your copper plating, via reliability in an HDI world is becoming an ever-greater challenge. This month we look at “The Hole Truth,” from creating the “perfect” via to how you can assure via quality and reliability, the first time, every time.
- Articles
- Columns
- Links
- Media kit
||| MENU - pcb007 Magazine
Estimated reading time: 6 minutes
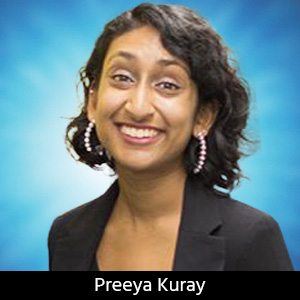
Material Insight: The Revival of Domestic PCB Fabrication
Harken back to the start of the millennium, which rung in several historically defining events: Ramifications of Y2K were dispelled (to global relief), George Bush defeated Al Gore in the 54th U.S. presidential election, and AOL combined with Time Warner in a $165 billion merger, signaling the convergence of old and new media. This significant moment in history also marked the onset of decay for PCB fabrication in America.
Just a few decades prior, the United States had been dominating the electronics industry. Innovation and manufacturing were done symbiotically on home soil; improvements of one led to reform of the other. Advancements, such as surface mount technology (SMT), were developed in the late 1980s, which not only improved integrated circuit board performance, but significantly reduced manufacturing costs by allowing for automation of assembly processes.
The advent of EDA software allowed for designs to be saved as computer files and input directly into manufacturing machinery to produce PCBs (instead of relying on photographs). Finally, the arrival of ball-grid array technology in the 1990s enabled higher board complexity and densification. Manufacturing reached new heights. This synergy between research and manufacturing (coupled with the growing demand for consumer electronics) allowed the U.S. PCB industry to reach its apex by the late 1990s, where it was valued at $11 billion (30% of the global share) with over 2,000 operating board shops.
By the start of the millennium, however, PCB fabrication plants in the U.S. started closing. OEMs began offshoring manufacturing to reduce operating costs. Today, U.S. PCB manufacturing is valued at $3 billion (3% of the global share) while board shops have dwindled to less than 200.
What happened in the past three decades? How did the United States lose its manufacturing prowess? What are the impending ramifications for R&D and innovation?
To answer these questions, consider that in the beginning of PCB manufacturing in America, OEMs owned their fabrication facilities. However, by the mid-1990s, OEMs were being pushed to maximize profit margins and restructure company finances. The most promising fiscal gain came from offshore manufacturing, where labor costs were orders of magnitude cheaper.
“There were some companies that did not want to do this,” says Brian Sinclair, technical marketing analyst at AGC Multi Material America. “Higher tier technology companies like HP, IBM, and Motorola spent decades becoming powerhouses by investing in cutting edge manufacturing technologies, processes, and methods. A significant portion of their money was spent on R&D to keep these processes state-of-the-art.”
And rightfully so. Technological improvement often led to major changes in the manufacturing process. When through-hole design was being phased out in favor of SMD, the manufacturing process was changed accordingly: Soldering pins were now replaced with thermal adhesives that bound SMDs to the PCB surface. When manufacturing is offshored, advances in production become severed from R&D. As a result, long-term innovation stagnates as state-of-the-art manufacturing processes are no longer developed on home soil.
“Unfortunately, the fiscal gains attained from outsourcing were tremendous,” Sinclair continues. “At this point in time, western OEMs were achieving record-setting financial results thanks to the low wages, the endless supply of workforce, lack of environmental regulations, and the duty-free taxation that came from offshoring to places like China.”
What led to China’s shift to manufacturing dominance? Former Chinese president Deng Xiaoping ordered a series of economic reforms in the late 1970s that opened the doors of a free market to China for the first time. This reform also created designated zones dedicated solely to manufacturing.
Today, several of those zones have evolved into entire cities devoted to manufacturing, sustained by decades of cultivating production know-how and expertise. Shenzhen, for example, is a zone-turned-city that produces 90% of the world’s electronics. Unsurprisingly, from the manufacturing advancements made over the last four decades (as well as the fact that most raw materials are imported domestically), China dominates global PCB production, currently controlling 30% of the market share ($37 billion). With the steady permeation of AI into consumer electronics and modern society, the demand for PCBs with higher complexity, finer pitches, and new materials will be higher than ever before. This will inevitably call for more advanced equipment, production lines, and manufacturing processes. The message is clear: Investment in advanced manufacturing is a necessity for long-term growth of the domestic PCB industry.
Where does that leave us now? Is funding domestic manufacturing the key to reclaiming the industry market share? How will this impact R&D and innovation?
The answer is complicated, but the tides are turning. With the passing of the Defense Production Act in March 2023, President Biden announced $50 million in investment toward domestic PCB manufacturing. On May 11, 2023, Congress reintroduced the Protecting Circuit Boards and Substrates Act of 2023, which would allocate $3 billion to domestic PCB manufacturing and provide 25% tax credit for purchases of American-made PCBs and substrates. Public awareness is also slowly changing. On social media, PCBs are getting the attention they deserve from trending hashtags like #chipsdontfloat. Finally, there are pathways that manufacturing plants can take now to offset operating costs and improve capabilities, such as taking advantage of R&D tax credits that may help fund advanced fabrication equipment.
Reinvesting in manufacturing may be a necessary component for the growth and prosperity of the domestic PCB industry. It will require continued dialogue and communication between industry and government. It will require training the new generation to carry on production knowledge and know-how. The solution is not straightforward; but from this vantage point, the future looks promising.
Resources
- “The History of High Density Interconnect,” by Amit Bahl, Sierra Circuits, Sept. 30, 2015.
- “The Changing World of PCBs,” NCAB Group, Nov. 23, 2020.
- “The Development of China’s PCB Manufacturing Industry in the World,” NextPCB, April 21, 2021.
- “What Will the PCB Act Mean to Electronics Manufacturers?” by Terri Enborg, PRIDE Industries, May 24, 2022.
- “The History and Evolution of Printed Circuit Board (PCB) Designs.” By G. Ken, EDN, April 18, 2022.
- “The Exodus of Chinese Manufacturing: Shutting down ‘The World’s Factory,’” by Prince Ghosh, forbes.com, Sept. 18, 2020.
- “A History of the Printed Circuit Board (PCB).” 911EDA.
- “Comparing PCB Industry in China and the United States, How Small and Medium-Sized Enterprises Can Do Better, by Kerstin,” PCBA Manufacturers, Sept. 27, 2022.
- “Legislation Introduced to Restore America’s Printed Circuit Board Industry after Two Decades of Decline,” Yahoo! Finance, May 11, 2023.
- “PCB History and Development Trends—Moko Technology,” by Will Li, MOKO TECHNOLOGY: Your Trusted Electronic Manufacturing Services Partner, Nov. 11, 2021.
- “Circuit Board Manufacturing: USA vs. Asia,” by Isaac Maw, Engineering.Com, Aug. 18, 2018.
- “NTI 100: The Unsinkable, Unstoppable PCB Market,” by Hayao Nakahara, Printed Circuit Design & Fab Online Magazine, July 28, 2022.
- “Leadership Lost? Rebuilding the U.S. Electronics Supply Chain,” by Joseph O’Neil, IPC, January 2022.
- “US Congress Proposes Support for American PCB Manufacturing,” by Zachariah Peterson, Altium, May 13, 2022.
- “The History of PCBS from 1870 to Today,” by Edwin Robledo, Fusion 360 Blog, May 10, 2022.
- “A Look inside Shenzhen’s High-Tech Empire,” by Wade Shepard, Forbes, July 14, 2016.
- “How Did R+D Disappear from American Electronics Manufacturing?” by Brian Sinclair, Microwave Product Digest, July 21, 2021.
- “Who Killed US Manufacturing?” by Ruth Strachan and Shehadi Sebastian, Investment Monitor, May 12, 2021.
- “America’s Defense Electronics Supply Chain Is Dangerously Thin and Falling Behind,” by Eric Tegler, Forbes, June 30, 2021.
- “Chips Don’t Float: Reviving Semiconductor Manufacturing Alone Won’t Assure America’s Security,” by Eric Tegler, Forbes, Jan. 7, 2022.
- “Top 10 Largest Printed Circuit Board Manufacturers in the US,” IndustrySelect, July 2021.
- Summary of the Protecting Circuit Boards and Substrates Act, U.S. Congress, Reps. Blake Moore and Anna G. Eschoo.
This column originally appeared in the June 2023 issue of PCB007 Magazine.
More Columns from Material Insight
Material Insight: David Griesel: Career Success Requires Tenacity, FlexibilityMaterial Insight: Diversifying PCB Manufacturing Through Nearshoring
Material Insight: The Dielectric Constant of PCB Materials
Material Insight: The Importance of Standards for the Chip Packaging Industry
Material Insight: A Conversation with Congressman Blake Moore
Material Insight: The Material Science of PCB Thermal Reliability
Material Insight: India’s Rise in the Global Electronics Ecosystem
Material Insight: My Journey From Atomic Lattices to Circuit Boards