-
- News
- Books
Featured Books
- pcb007 Magazine
Latest Issues
Current IssueInventing the Future with SEL
Two years after launching its state-of-the-art PCB facility, SEL shares lessons in vision, execution, and innovation, plus insights from industry icons and technology leaders shaping the future of PCB fabrication.
Sales: From Pitch to PO
From the first cold call to finally receiving that first purchase order, the July PCB007 Magazine breaks down some critical parts of the sales stack. To up your sales game, read on!
The Hole Truth: Via Integrity in an HDI World
From the drilled hole to registration across multiple sequential lamination cycles, to the quality of your copper plating, via reliability in an HDI world is becoming an ever-greater challenge. This month we look at “The Hole Truth,” from creating the “perfect” via to how you can assure via quality and reliability, the first time, every time.
- Articles
- Columns
- Links
- Media kit
||| MENU - pcb007 Magazine
Estimated reading time: 4 minutes
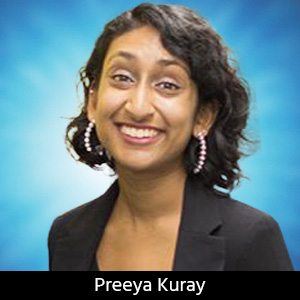
Material Insight: The Material Science of PCB Thermal Reliability
Printed circuit board (PCB) reliability testing is generally performed by exposing the board to various mechanical, electrical, and/or thermal stimuli delineated by IPC standards, and then evaluating any resulting failure modes. Thermal shock testing is one type of reliability test that involves repeatedly exposing the PCB test board to a 288°C pot of molten solder for a specific time (typically 10 seconds) and measuring the number of cycles it takes for a board’s copper layer to separate from the organic dielectric layer. If there is no delamination, fabricators can rest assured that the board will perform within expected temperature tolerances in the real world.
From a materials perspective, what is happening to the copper and dielectric during thermal shock testing? What causes copper to separate from the organic dielectric layer in the first place?
To answer these questions, it is necessary to take a closer look at each component at the molecular level during testing. Subjection to intense thermal fluctuations causes different rates of expansion and contraction in different materials. This can generate stresses and ultimately lead to cracks or delamination between the copper and dielectric parts of the test board. The coefficient of thermal expansion (CTE) is defined as a material’s dimensional change in length over a measured temperature range. Typical CTEs are listed in Table 1. Copper exhibits a Z-axis CTE of ~18 ppm/°C from 20–25°C while organic materials like epoxy display higher values (~55 ppm/°C). The quantitative differences in CTE between copper and organic materials can better explain why delamination may occur: Some types of materials just expand and contract more easily than others, leading to stresses and ultimately cracks during reliability testing.
But why do some materials have higher CTE values than others? Why do organic materials like epoxy and polyimide have higher CTE values compared to metals and ceramics?
The CTE is contingent on the bond strength between the atoms that make up that material. Covalently bonded materials exhibit strong shared bonds between the individual atoms, resulting in very low CTEs. For this reason, dielectric layers in PCBs are often reinforced with fillers like fused SiO2, in which silicon is covalently bonded to oxygen (SiO2 CTE = 0.5 ppm/°C). Other popular fillers include ceramics such as Al2O3 (CTE = 8 ppm/°C) or TiO2 (CTE = 10 ppm/°C). Ceramic materials exhibit ionic bonding, where the oxygen atom completely transfers its valence electrons to a metal atom, generating two oppositely charged ions. The unequal sharing of electrons yields a slightly weaker bond and contributes to a higher overall CTE (compared to materials that are purely covalently bonded).
What about metals? In the early 1900s, Paul Drude described the bonding between metallic atoms as a “sea of electrons,” in which metals can be modeled as a lattice of positively charged metallic cores, all sharing a vat of communal valence electrons. The electron delocalization (or electron sharing) in metals results in an even lower bonding energy than covalent or ionic bonding, which may contribute to why pure metals like copper typically have higher CTE values than ceramic fillers.
Finally, we arrive at the metaphorical glue holding together the PCB dielectric layer: the polymer. The CTE values of typical polymers can range from 20–100 ppm/°C (from 20°C–25°C), which are much higher than ceramics or metals. Polymers are defined as chemical compounds in which individual molecules are bonded together in long, repeating chains. (Imagine pearl beads bound together to make a necklace.) The low energetic barrier of polymer chains to move and undergo conformational changes can help explain their higher CTE values.
Bearing all this in mind, it is the task of formulation scientists to develop dielectric laminates, prepregs, and bond plies that will mitigate the impact of thermal expansion within a PCB and ultimately pass thermal reliability testing. By considering the intrinsic material properties of all components (and combining them in appropriate quantities), it is possible to create new materials that can meet, or even surpass, thermal reliability performance requirements. For example, fastRise™ TC (from AGC Multi Material America) is an example of a non-reinforced (pure resin, fiberglass-free) bond ply that exhibits excellent thermal reliability. By matching the CTE of copper (18 ppm/°C), this material is able to expand and contract at the same rate as the copper, mitigating stresses formed in the PCB during thermal reliability testing. In following IPC-TM-650 2.5.27, 24 panels of test coupons made from this material underwent 200 thermal cycles from 25°C to 260°C without exhibiting any failures. This is especially remarkable, considering that most dielectric materials on the market contain fairly large amounts of polymeric components.
Breaking through barriers like this illustrates the challenges and fulfillments of formulation science: pushing past intrinsic physical limitations to create something greater than the sum of its parts. It is what first drew me to become a materials scientist, and what will keep me grounded in this field for years to come.
This column originally appeared in the October 2023 issue of PCB007 Magazine.
More Columns from Material Insight
Material Insight: David Griesel: Career Success Requires Tenacity, FlexibilityMaterial Insight: Diversifying PCB Manufacturing Through Nearshoring
Material Insight: The Dielectric Constant of PCB Materials
Material Insight: The Importance of Standards for the Chip Packaging Industry
Material Insight: A Conversation with Congressman Blake Moore
Material Insight: India’s Rise in the Global Electronics Ecosystem
Material Insight: The Revival of Domestic PCB Fabrication
Material Insight: My Journey From Atomic Lattices to Circuit Boards