-
- News
- Books
Featured Books
- design007 Magazine
Latest Issues
Current IssueProper Floor Planning
Floor planning decisions can make or break performance, manufacturability, and timelines. This month’s contributors weigh in with their best practices for proper floor planning and specific strategies to get it right.
Showing Some Constraint
A strong design constraint strategy carefully balances a wide range of electrical and manufacturing trade-offs. This month, we explore the key requirements, common challenges, and best practices behind building an effective constraint strategy.
All About That Route
Most designers favor manual routing, but today's interactive autorouters may be changing designers' minds by allowing users more direct control. In this issue, our expert contributors discuss a variety of manual and autorouting strategies.
- Articles
- Columns
- Links
- Media kit
||| MENU - design007 Magazine
Estimated reading time: 4 minutes
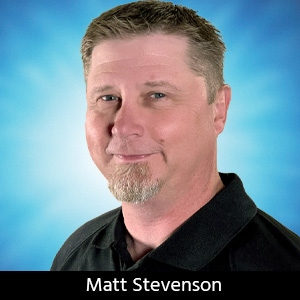
Connect the Dots: Playing the ISO ‘Game’ for Better Quality
If someone asks at your next backyard barbecue, “How is work going?” it might not be gripping to say, “I am improving processes to realize efficiencies based on the ISO 9001 framework.” Unless, like me, they are also an ISO nerd. While that’s what I’m doing at work, perhaps a more engaging answer would be, “We have turned quality improvement into a game that everyone on the production team can participate in.”
Our ISO game turns every production order into a gaming token. Each token generates scores of “on time” and “quality” for every system it passes through.
The sum of the scores from each department is tallied at the end of production to calculate a combined score. Each department, shift, and participant are continually challenged to find ways to increase token scores. Our game complements the competitive elements of human nature, whether between different shifts or neighboring departments. The ultimate goal is to improve the system itself, providing everyone with a common goal, and allowing for a friendlier environment, while at the same time improving on-time deliveries and producing higher quality boards.
That’s right. We have been gamifying our ISO initiative. Gamification is an extremely useful methodology for companies needing to train new knowledge and skills. It is also used successfully for career development, early group learning, and continuing education. It makes the work more fun and, I believe, makes our business more efficient and our products higher quality.
After 20 years as a lab technician, I moved into administering the quality management systems (QMS). That meant I became the ISO point person. My job is to continue the ongoing improvement that has been integral to our company’s success with ISO.
Commitment to ISO Leads to Improved Results
ISO and QMS should be more than a badge on the company website. ISO certification tells the marketplace that your company has created a system that drives continuous improvement of production output.
Even when the QMS functions well and there exists a quality-focused culture, that does not mean it is time to turn on the autopilot. Use the ISO framework to pursue truly continuous improvement. As Jeff Bezos said about developing a space program, we intend to work “step-by-step, ferociously.”
Step-by-step is a great model for our work in building custom PCBs for clients. It is a step-by-step process; a PCB board build goes through multiple systems on our factory floor, from masking and plating to drilling and shipping.
ISO 9001 is a lens to look at the work. Each step costs in time and expense. Each team works in a specific area, taking in a job from the previous stage and performing their task, then handing it off to the next.
With ISO, No Cheat Codes
Once we have the systems set up and scored, we bring in the experts. Not outside experts, but the people who work every day on the factory floor on these questions. The teams that operate each process are our experts and have developed all the innovations of our QMS. They are far more familiar with their process than I am. The game helps to train them in ISO and practice in a more engaging way, which helps us as a team consider how changes would affect the process.
For instance, quality checks are a necessary part of manufacture, but they have a high cost. It is expensive to do constant quality checks and does not add value to a functioning board. However, the sooner a failure or error is identified, the less wasted work—tokens—we will spend on that board. Using the game, we can visualize what happens when we move a quality check. The game helps us ask, “Does the increase in time and expense pencil out to more efficiency and better quality?”
Visualize, Discuss, and Improve
The game is a way for us to look at our system and see how their expertise can find ways to improve. Are quality checks in the optimal place? Is there redundancy? Could we reduce some of the steps?
Any organization that has been successful with ISO will tell you that this is the key: bringing the team together to visualize and refine their work. The game makes that easier and more fun so we get our creative juices flowing. Not only that, but we can also see the results in a measurable way: more tokens.
We have only been using the game for a short while. It has created more interest and increased momentum in our ISO work. It gives people the buy-in and a global vision of how their work impacts the other aspects of our business. We have animated discussions about maintenance, the supply chain, and the other wraparound efforts that impact the business with the same abstraction of tokens expended. It gives flight to our collective purpose.
The accumulated wisdom of the team captured with the game then forces action by leadership. The measure of tokens makes it easy to communicate the impact of proposed changes.
ISO initiatives are ripe for gamification, and we are really happy with how it has energized our initiatives. Maybe soon team members will be working to get on a leaderboard of tokens saved.
Jamin Wilson is quality systems administrator at Sunstone Circuits.
This column originally appeared in the July 2023 issue of Design007 Magazine.
Download Sunstone's The Printed Circuit Designer’s Guide to… Designing for Reality by Matt Stevenson. You can view other titles in the I-007eBooks library here.
More Columns from Connect the Dots
Connect the Dots: How to Avoid Five Common Causes of Board FailureConnect the Dots: Sequential Lamination in HDI PCB Manufacturing
Connect the Dots: The Future of PCB Design and Manufacturing
Connect the Dots: Proactive Controlled Impedance
Connect the Dots: Involving Manufacturers Earlier Prevents Downstream Issues
Connect the Dots: Stop Killing Your Yield—The Hidden Cost of Design Oversights
Connect the Dots: Designing for Reality—Routing, Final Fab, and QC
Connect the Dots: Designing for Reality—Surface Finish