-
- News
- Books
Featured Books
- design007 Magazine
Latest Issues
Current IssueAll About That Route
Most designers favor manual routing, but today's interactive autorouters may be changing designers' minds by allowing users more direct control. In this issue, our expert contributors discuss a variety of manual and autorouting strategies.
Creating the Ideal Data Package
Why is it so difficult to create the ideal data package? Many of these simple errors can be alleviated by paying attention to detail—and knowing what issues to look out for. So, this month, our experts weigh in on the best practices for creating the ideal design data package for your design.
Designing Through the Noise
Our experts discuss the constantly evolving world of RF design, including the many tradeoffs, material considerations, and design tips and techniques that designers and design engineers need to know to succeed in this high-frequency realm.
- Articles
- Columns
- Links
- Media kit
||| MENU - design007 Magazine
Book Excerpt: 'The Printed Circuit Designer's Guide to... Manufacturing Driven Design'
August 3, 2023 | I-Connect007 Editorial TeamEstimated reading time: 2 minutes
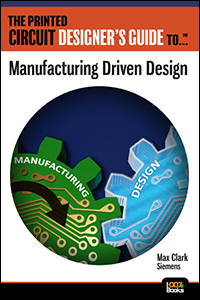
Chapter 1: How We Got Where We Are
The Paradox of DFM
Before the development of PCB computer-aided manufacturing (CAM), the process of preparing a board for fabrication and assembly was as cumbersome as actually designing the board itself. Early PCB manufacturing involved several manual processes which remain largely intact today, mirrored by a modern digital equivalent. Manual design for manufacturing (DFM) began with PCB artwork that was produced by applying an opaque film on a clear piece of mylar. The examination and measurement process involved using an eye loupe, and any necessary edits were made by either carefully scratching off the tape with an X-ACTO® knife to provide additional clearance or filling in voids with a black marker.
Tasks such as drilling and component placement relied on custom-built mechanical programs. These were stand-alone solutions, created individually in a time-consuming and painstaking process involving specialized equipment such as drill bomb-sight machines. With such an intensive and manual process, there were many challenges to overcome to meet all the necessary operational complexities needed to produce a circuit board.
As the complexity of systems increased, these physical sheets were replaced by digital files, but the manual complexities persisted.
During the 1980s, the design data transferred to manufacturing facilities was heavily split as a result of the myriad of solutions necessary to produce a PCB. Gerber data was used for artwork, Excellon drill format for mechanical drilling, typically a centroid file which assisted in component placement and, if you were very lucky, a netlist file in IPC-356-A format was included. This data came accompanied by a corresponding component bill of materials.
The objective of the PCB CAM system was to reverse engineer that collection of files back into a semblance of what originated in the initial design application. Shortly after these PCB CAM systems began reconstructing the design, manufacturers began to realize the potential in evaluating the PCB—only this time from their unique manufacturing perspective.
PCB CAM was created to optimize the process of transferring a design to manufacturing. The manufacturing process capabilities were assembled into Engineering Rules Files (ERFs), with multiple ERFs created based on the technology present within the design. Fabricators would often modify the design data to improve the overall quality, yield, and reliability of the final PCB. The use of generated artwork by photoplotters meant both the previous manual operations, as well as the mechanical programs, became obsolete.
At this point, Electronic Design Automation (EDA) solutions were focused on the PCB’s electrical requirements rather than its manufacturability. Even now, you often see this manifested when PCB designers “throw the design over the wall.” This could be more accurately stated as “let the manufacturers deal with it” or “my manufacturers do that!” This sentiment of making it someone else’s problem is a mantra I still hear repeated by designers to this day. Whether this line of thinking is further exasperated depends on when in the manufacturing process the issues occur. If the issues are related to assembly and identified after fabrication, then a corrective design modification is too late. This could lead to the use of expensive process variation which may require specialized tooling, such as a step stencil, adding additional manpower resulting in higher cost, and could negatively impact yield, quality, and reliability.
"Is this really DFM?" asks the author. Continue reading The Printed Circuit Designer's Guide to... Manufacturing Driven Design to find out his answer to this question.
Suggested Items
Delta SEA Partner Event 2025 Unites Regional Partners to Embrace a “Future Ready” Vision
07/03/2025 | Delta ElectronicsDelta Electronics (Thailand) Public Company Limited, successfully hosted its Delta SEA Partner Event 2025: Future Ready at Delta Chungli Plant 5, Taiwan on June 10 – 11 , 2025.
Murray Percival Company Welcomes CeTaQ to Its Line Card, Optimizing SMT Processes for PCB Manufacturers
07/03/2025 | Murray Percival CompanyThe Murray Percival Company, a trusted supplier to the Midwest's electronics industry, is pleased to announce that it has added CeTaQ to its line card, a global expert in Surface Mount Technology (SMT) measurement systems.
RBB’s Jeff Schartiger Appointed to SMTA Ohio Board as Technical Advisor
07/03/2025 | RBBRBB, a trusted leader in electronics manufacturing since 1973, is proud to announce that Jeff Schartiger, Operations Manager at RBB, has been appointed to the SMTA Ohio Chapter Board as a Technical Advisor.
Kitron Receives EUR 4 Million Contract for Defense Airborne Radar Application
07/02/2025 | KitronKitron has received an order valued at EUR 4 million to produce electronics modules for airborne radar application, destined for the US market.
Zollner Completes Full Acquisition of Bluechips Microhouse
07/01/2025 | Zollner Elektronik AGZollner Elektronik AG has successfully finalized its complete takeover of Bluechips Microhouse Co., Ltd., in Thailand. In the future the company will operate as part of the Zollner Group of companies under the leadership of Thomas Kiefl—strategically networked, technologically focused and internationally oriented.