-
- News
- Books
Featured Books
- design007 Magazine
Latest Issues
Current IssueProper Floor Planning
Floor planning decisions can make or break performance, manufacturability, and timelines. This month’s contributors weigh in with their best practices for proper floor planning and specific strategies to get it right.
Showing Some Constraint
A strong design constraint strategy carefully balances a wide range of electrical and manufacturing trade-offs. This month, we explore the key requirements, common challenges, and best practices behind building an effective constraint strategy.
All About That Route
Most designers favor manual routing, but today's interactive autorouters may be changing designers' minds by allowing users more direct control. In this issue, our expert contributors discuss a variety of manual and autorouting strategies.
- Articles
- Columns
- Links
- Media kit
||| MENU - design007 Magazine
Estimated reading time: 4 minutes
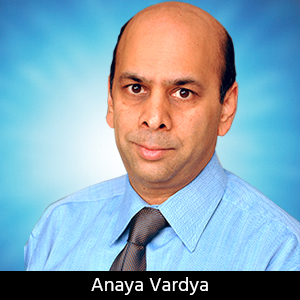
Standard of Excellence: Advancing PCBs—The Total Solution
One of the most important elements of running a business is being able to look forward. A true company leader must be able to define the future as best she or he can and then adapt their own strategies to meet the demands of that future. It’s been said that if you don’t define your future, someone else will do it for you.
This month I want to look at some of the changes, or should I say improvements, that are occurring in our own industry. Some of them are new but others have been around for years. Either way, their time has come.
Seamless Design Integration
While the traditional approach was to work consecutively—first the design, followed by the board fabrication—this led to potential communication gaps and inefficiencies. The new total solution model bridges this gap, allowing for design and fabrication to work in tandem. Seamless integration ensures that the design is optimized for manufacturability, reducing the need for costly iterations and redesigns. We will be seeing more of this cooperative effort in the future as designers and board fabricators find ways to work closer and better together.
Concurrent Engineering
The total solution approach allows concurrent engineering where multiple stages of product development work simultaneously rather than sequentially. This reduces the time-to-market and works well with this concept. Design, fabrication, and assembly teams collaborate and work in parallel. Engineers begin fabrication prototypes while the design is still being completed, thus streamlining the entire production timeline. It allows for fixing any issues and design flaws on the run. Concurrent engineering accelerates the product development cycle and ensures a smoother transition from prototype to production.
New Advanced Fabrication Technologies
New equipment means new technology processes in fabrication. New equipment uses AI to learn as it produces. Equipment also provides for high-speed automated processes, thus allowing the production of cutting-edge technology PCBs in severely reduced turn-around times. Laser drilling, direct imaging, and additive manufacturing are becoming mainstream. Where once only the wealthy and advanced companies could afford DI and LDI equipment, now with a variety of makes, models, and prices, this equipment will become a common sight in all PCB fabrication centers. This modern equipment allows the fabricator to produce more PCBS that are intensely complex. It also eliminates many manual processes, reducing human error and minimizing production bottlenecks. Additionally, the integration of AI and ML (machine learning) in fabrication processes further optimizes production, thus enhancing yield rates and reducing waste.
Streamlined Supply Chain Management
Total solution providers have established partnerships and supply chain networks to ensure a smooth flow of materials and components throughout the product development process. This streamlined supply chain management optimizes material procurement and inventory management and reduces lead times for production. Total solution providers can leverage their purchasing power to negotiate better prices and, in the case of assembly, availability of components. This helps control costs and mitigate supply chain disruptions. An efficient supply chain contributes significantly to accelerated product development and significantly reduces time to market.
Customer-centric Approach
Total solution emphasizes a customer-centric mindset by offering a complete solution of design, fab, and assembly. By working closely with the customers, the supplier will have a clear and complete understanding of the customers’ goals, requirements, and preferences. This will result in faster iterations and design adjustments to meet market demands and capitalize on emerging opportunities. By providing a complete PCB solution, we can offer comprehensive support, including post-launch services that will lead to higher customer satisfaction.
Powerful Cooperative Partnerships
By the mere virtue of providing the customers with a complete total concept-to-reality solution, all parts of the supply chain have to work together in a synergistic, productive, and cooperative partnership. This not only applies to the fabricators, designers, and assemblers, but with our vendors as well. There has been a steady increase in the cooperation between the fab houses and our suppliers. This has always been a good relationship but now it has become a true partnership as new high tech equipment featuring AI, ML, and automation becomes more common in PCB shops. In many cases, such as quality and chemistry processes, these suppliers are installing automatic control and auditing systems to make sure that quality and processes are always within tolerances.
The printed circuit board industry’s new total concept-to-reality approach is revolutionizing product development and time-to-market. By integrating design, fabrication, and assembly, the industry is achieving seamless collaboration, concurrent engineering, advanced fabrication technologies, enhanced testing, streamlined supply chain management, and a complete customer-centric focus. These factors, combined with the improved synergistic relationship with our suppliers, is achieving an experience of improvement unlike at any other time in our industry’s history.
What I am encouraged about is the way companies are working together in a spirit of generous collaboration to achieve a better solution—a complete solution for the benefit of all concerned, especially the customer.
Anaya Vardya is president and CEO of American Standard Circuits; co-author of The Printed Circuit Designer’s Guide to...Fundamentals of RF/Microwave PCBs and Flex and Rigid-Flex Fundamentals. He is the author of Thermal Management: A Fabricator's Perspective and The Companion Guide to Flex and Rigid-Flex Fundamentals. Visit I-007eBooks.com to download these and other free, educational?titles.
More Columns from Standard of Excellence
Standard of Excellence: Training Your Team to Excel in Customer ServiceStandard of Excellence: Delivering Excellence—A Daily Goal
Standard of Excellence: The Role of Technology in Enhancing the Customer Experience
Standard of Excellence: Turning Negative Customer Feedback Into Positive Outcomes
Standard of Excellence: Anticipating Customer Needs Early and Often
Standard of Excellence: The Power of Personalization in Customer Care
Standard of Excellence: Building Trust with Customers—The Foundation of Excellent Service
Standard of Excellence: Finding and Developing Future Leaders in Manufacturing