-
- News
- Books
Featured Books
- design007 Magazine
Latest Issues
Current IssueShowing Some Constraint
A strong design constraint strategy carefully balances a wide range of electrical and manufacturing trade-offs. This month, we explore the key requirements, common challenges, and best practices behind building an effective constraint strategy.
All About That Route
Most designers favor manual routing, but today's interactive autorouters may be changing designers' minds by allowing users more direct control. In this issue, our expert contributors discuss a variety of manual and autorouting strategies.
Creating the Ideal Data Package
Why is it so difficult to create the ideal data package? Many of these simple errors can be alleviated by paying attention to detail—and knowing what issues to look out for. So, this month, our experts weigh in on the best practices for creating the ideal design data package for your design.
- Articles
- Columns
- Links
- Media kit
||| MENU - design007 Magazine
Rigid-flex Design Guidelines
September 27, 2023 | Cherie Litson, CID+, Litson1 ConsultingEstimated reading time: 4 minutes
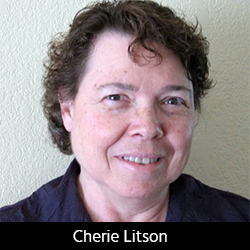
Rigid-flex circuits are unique structures; part rigid board and part flex, they’re increasingly working their way into many of the electronic devices we use every day.
There have been many advances in rigid-flex lately as more companies find themselves exploring this technology. So, before I started writing this article about rigid-flex design, I double-checked a few things. Fortunately, there is plenty of rigid-flex information available on a variety of great websites that we all know and trust. So, here’s a quick look at some of the principles of rigid-flex design.
Rigid board designers who consider entering the rigid-flex arena typically have a handful of questions. One of the most obvious is, “Why do we need rigid-flex anyway?” If we just need a way to fit circuitry into a case and it will stay that way, rigid-flex will work fine. But if the board will be moving on a regular basis during operation, then opting for just flexible circuits or attaching flex to a traditional rigid board is a better way to go.
Another common question is, “How does my PCB layout software work with curves and hatched planes?” There are a lot of curved traces and hatched planes in flex circuits. If it’s a hassle to create a curved trace, you may need a different software package that is optimized for flex and rigid-flex design. Many of today’s EDA tools are set up for rigid-flex design.
Rigid-flex boards use the same materials as any rigid board. One way to do this is by creating the flex portion along with the layers of the rigid board, and use a delamination process to remove any unwanted layers. No components are mounted on the flex portion of the board. One layer is used for the return and the other layer is used for your signals. The return is commonly a GND plane and hatched in the flex area of the board. Vias are not usually placed in this area either but may be used if needed.
Another rigid-flex approach is to first create a flex board and then laminate or adhere a rigid board (or just a stiffener) to the flex. This is done when you need more signal layers in the flex portion, the flex needs to be longer, and/or it needs to withstand multiple flexing without breaking. The rigid portions are processed separately and have the components assembled to them. In general, components should not be mounted on the flex portion. Flexing solder joints is just a bad thing.
Now you’ve got the basics, what’s next? Here are a few guidelines, in no particular order:
- Layer stackup: Keep the flex layers to a minimum of two for increased mechanical flexibility and reduced costs.
- Electrical design constraints: What needs to be on the flex and what doesn’t? Trace widths may need to vary. They may need to be very long. Make sure that the signals can handle these conditions. Also, designers should have a good understanding of the heat sinking capabilities of the flex portion.
- Mechanical design constraints: You will need more clearance to the edges of the board, cutouts, slots, other traces, etc., as well as more space around bends and corners. Any slots or holes that must be cut will need “relief” features so that the material doesn’t tear.
- Component placement and finishes: As I mentioned, components in general, should not be mounted on flex, but there are exceptions. Some components can be mounted on the flex portion with a stiffener material attached beneath them to prevent solder joint breakage. The finish used to protect the open copper traces is usually an overlay material or a thicker solder mask—not LPI. Both of these have larger clearance areas around the components. Conformal coatings can be used to protect the bare copper after soldering.
- Testing and verification: Because of the unique structure of rigid-flex circuits, testing and verification are critical parts of the process. Test points must be strategically placed, not too close to edges or components, and not covered by solder mask. Ask your fabricator for more information.
Rigid-flex Resources
IPC has a variety of great resources and specific industry standards on its website. IPC-6013 Qualification and Performance Specification for Flexible Printed Boards, features a treasure trove of information. IPC-4201 through IPC-4204 cover many of the base materials used for flex circuits. IPC-4562 covers copper foils and IPC-SM-840 defines the masks that can be used.
Once you’ve defined what you need in your rigid-flex design, find a flex fabricator you can work with to get the job done. Most of the guidelines listed by fabricators online focus on the company’s limitations. They all have different capabilities, so be sure to match your needs with their limits for the best cost return. Pay close attention to their “standard” feature sizes, not the “highest-end capability.” If your electrical and mechanical constraints are critical to your design, be sure to have a conversation with the production engineer at the facility. This will help you and the fabricator.
Your EDA software company should also have an online section titled “How to Layout a Flex Design.” These are great resources and worth looking at. If you don’t like your software’s approach to rigid-flex, check out some of the videos from the other software companies. You might find something you didn’t think of before.
Cherie Litson is a PCB design and engineering consultant.
This article originally appears in the September 2023 issue of Design007 Magazine.
Suggested Items
Flexible Printed Circuit Board Market to Reach US$40.447 Billion by 2030
07/10/2025 | Globe NewswireThe flexible printed circuit board market will grow at a CAGR of 8.28% to be valued at US$40.447 billion in 2030 from US$27.17 billion in 2025.
Taiwan PCB Industry Adopts Cautious CapEx Strategy, Eyes AI and Southeast Asia for Growth
07/10/2025 | TPCADriven by the stabilization of the global electronics market and the strong demand for AI applications, although the Taiwan printed circuit (PCB) industry is facing a trend of capital expenditure convergence for three consecutive years, its output value and operating performance continue to rise, indicating that the industry is shifting from high investment to high added value development, and the industrial structure is undergoing a steady transformation.
IBIDEN Earns Recognition in FTSE Russell ESG Indexes, Reinforcing Commitment to Sustainable Growth
07/07/2025 | IBIDENIBIDEN Co, Ltd. is pleased to announce that it has been selected for FTSE4Good Index Series for the tenth consecutive year, FTSE Blossom Japan Index for the nineth consecutive year, and FTSE Blossom Japan Sector Relative Index for the fourth consecutive year.
Symposium Review: Qnity, DuPont, and Insulectro Forge Ahead with Advanced Materials
07/02/2025 | Barb Hockaday, I-Connect007In a dynamic and informative Innovation Symposium hosted live and on Zoom on June 25, 2025, representatives from Qnity (formerly DuPont Electronics), DuPont, and Insulectro discussed the evolving landscape of flexible circuit materials. From strategic corporate changes to cutting-edge polymer films, the session offered deep insight into design challenges, reliability, and next-gen solutions shaping the electronics industry.
Flexible Electronics Market to Reach $66.9 Billion by 2032, Growing at a CAGR of 9.2% from 2025
06/30/2025 | PRNewswireThe flexible electronics market is projected to reach $66.9 billion by 2032, up from an estimated $38.4 billion in 2025, growing at a robust CAGR of 9.2% during the forecast period.