-
- News
- Books
Featured Books
- design007 Magazine
Latest Issues
Current IssueProper Floor Planning
Floor planning decisions can make or break performance, manufacturability, and timelines. This month’s contributors weigh in with their best practices for proper floor planning and specific strategies to get it right.
Showing Some Constraint
A strong design constraint strategy carefully balances a wide range of electrical and manufacturing trade-offs. This month, we explore the key requirements, common challenges, and best practices behind building an effective constraint strategy.
All About That Route
Most designers favor manual routing, but today's interactive autorouters may be changing designers' minds by allowing users more direct control. In this issue, our expert contributors discuss a variety of manual and autorouting strategies.
- Articles
- Columns
- Links
- Media kit
||| MENU - design007 Magazine
Estimated reading time: 4 minutes
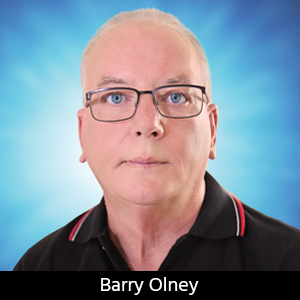
Beyond Design: Design Success with IPC Standards
PCB design is all about knowing your EDA software tool backward. There is no point in designing a complex board if it doesn’t perform to expectations or isn’t manufacturable. The goal is to create a board that is functional, reliable, and cost-effective. Design rules are important because they help optimize the design of a product for its manufacturing and assembly praocess. This is called design for manufacturing (DFM). It aims to minimize the risk of errors and delays when a product is transitioning from prototyping to mass manufacturing. It also optimizes design and cost and is vital to meet time to market. Employing DFM strategies reduces the cost and difficulty of producing a product while maintaining its quality.
I started laying out single- and double-sided boards way back in 1975 using Bishop Graphics tape. The thinnest tape was 12 mils with 50-mil vias and 60-mil component pads. It was too easy; I did not have to worry about design rules for traces and footprints. Clearance was always the same as the trace width. A few years later, I progressed to the first version of Protel PCB layout software. No schematics or libraries to consider; just drop a few DIP footprints and passives and start connecting the dots. Again, the rules were all done with standard 60-mil-wide round and oblong pads, but I could push the envelope to 8-mil traces which was the narrowest ink pen for the XY plotter. The challenge was to etch the 8-mil traces without a break. But a touch-up pen on the photoresist fixed that. This was sufficient for prototype boards we were producing for university research projects. The clock speed was 10 MHz max, so signal integrity was not an issue and planes were not considered.
In 1987, I was thrown in the deep end. The R&D company I was working for purchased IC and PCB design software from Daisy (later acquired by Intergraph Electronics). BoardMaster PCB was a complex UNIX package that had a steep learning curve so the focus was on learning the tool so that we could produce our new fiber broadband network. The prototype network took 18 months of colossal effort to produce and it proved the concept. However, it was not manufacturable in quantities.
Our technology partners—Siemens and Alcatel in Europe, and US West and Bell Atlantic in the U.S.—provided us with their design rules so that all our equipment could be assembled in any modern production facility worldwide. I also obtained the IPC standards for PWB design and manufacture, and merged them into a complete set of design rules. Three years later, we were ready for mass production. The lesson here is that anyone can produce a prototype but it takes much, much more effort (at first) to produce a manufacturable product. However once set up, the constraints become part of the design process and take little extra effort to enforce.
Where Does a Newbie Designer Start?
IPC was founded in 1957, and has provided the worldwide electronics industry with standards for the design and manufacture of printed circuit boards, compiled over the years with the support of both committee and industry members. IPC has more than 300 active multilingual industry standards that cover nearly every stage of the electronics product development cycle.
IPC-2221B is the foundation design standard for all documents in the IPC-2220 series. The series is built around the IPC-2221, Generic Standard on Printed Board Design, the base document that covers all generic requirements for printed board design, regardless of materials. From here, the designer chooses the appropriate sectional standard for a specific technology.
All five sectional standards are included in the series:
- IPC-2222B, Sectional Design Standard for Rigid Organic Printed Boards
- IPC-2223E, Sectional Design Standard for Flexible Printed Boards
- IPC-2224, Sectional Standard for Design of PWBs for PC Cards
- IPC-2225, Sectional Design Standard for Organic Multichip Modules (MCM-L) and MCM-L Assemblies
- IPC-2226, Sectional Design Standard for High-Density Interconnect (HDI) Printed Boards
This series provides coverage on material and final finish selection, current-carrying capacity and minimum electrical clearances, test-specimen design, guidelines for V-groove scoring, dimensioning requirements, and conductor thickness requirements. Some of these standards are now published in Chinese and German.
Also, several documents apply to high-speed and land-pattern design:
- IPC-2228, Sectional Design Standard for High Frequency (RF/Microwave) Printed Boards
- IPC-2251, Design Guide for Electronic Packaging Utilizing High-Speed Techniques
- IPC-2141A, Design Guide for High-Speed Controlled Impedance Circuit Boards
- IPC-7351B, Generic Requirements for Surface Mount Design and Land Pattern Standard
These standards (and their predecessors) have been part of a well-used section of my technical library since 1987. They provide excellent reading and reference material for all PCB designers. These documents are available for purchase from IPC. A complete list of standards with their latest revision is available from the IPC Document Revision Table. Design rules must keep up with the latest devices and fabrication processes without losing sight of DFM. If you follow the above IPC guidelines, you will be designing for both manufacturability and mass production.
IPC standards are important for PCB design because they standardize requirements for the installation and fabrication of electronic equipment and assemblies. IPC standards ensure that manufacturers produce safe, reliable, and high-performance PCB boards by focusing on manufacturing details, and are committed to maintaining quality throughout the manufacturing process. Adhering to IPC standards issued by the industry body can ensure that you produce high-quality PCBs consistently. IPC certification ensures that vendor and PCB manufacturer use the same terminology so there is not any scope for miscommunication.
For the latest trends in PCB and high-speed design, both the newbie and the seasoned designer should read industry magazines such as Design007, PCB007, and SMT007 to keep up to date with new techniques for design and manufacture.
Resources
Beyond Design: Design Rules & DFM for High-Speed Design by Barry Olney
This column originally appeared in the October 2023 issue of Design007 Magazine.
More Columns from Beyond Design
Beyond Design: Effective Floor Planning StrategiesBeyond Design: Refining Design Constraints
Beyond Design: The Metamorphosis of the PCB Router
Beyond Design: Radiation and Interference Coupling
Beyond Design: Key SI Considerations for High-speed PCB Design
Beyond Design: Electro-optical Circuit Boards
Beyond Design: AI-driven Inverse Stackup Optimization
Beyond Design: High-speed Rules of Thumb