-
- News
- Books
Featured Books
- design007 Magazine
Latest Issues
Current IssueShowing Some Constraint
A strong design constraint strategy carefully balances a wide range of electrical and manufacturing trade-offs. This month, we explore the key requirements, common challenges, and best practices behind building an effective constraint strategy.
All About That Route
Most designers favor manual routing, but today's interactive autorouters may be changing designers' minds by allowing users more direct control. In this issue, our expert contributors discuss a variety of manual and autorouting strategies.
Creating the Ideal Data Package
Why is it so difficult to create the ideal data package? Many of these simple errors can be alleviated by paying attention to detail—and knowing what issues to look out for. So, this month, our experts weigh in on the best practices for creating the ideal design data package for your design.
- Articles
- Columns
- Links
- Media kit
||| MENU - design007 Magazine
Simplifying Your Design
November 9, 2023 | I-Connect007 Editorial TeamEstimated reading time: 1 minute
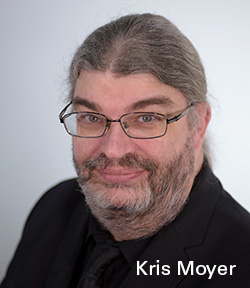
It’s safe to say that millions of dollars, not to mention man-hours, are wasted each year because of over-constrained, overly complicated PCB designs. Much of this is due to the increase in signal speeds and rise times, even in “mature” PCBs, and the extra cost is already part of the budget.
For this issue on simplifying PCB designs, the I-Connect007 Editorial Team spoke with IPC instructor Kris Moyer about ways that designers can avoid overconstraining their designs and making them needlessly complex. As Kris says, streamlining your design comes down to having a solid understanding of fab and assembly processes and the silicon tradeoffs that can simplify or overcomplicate your design, as well as the need to start working with fabricators early in the cycle.
Andy Shaughnessy: What are some typical snafus and missteps that you see designers make to overcomplicate their designs?
Kris Moyer: Here’s what often happens: Let’s say you have one connector on your board that needs tight tolerance. But rather than dimensioning to just that connector, locally, designers will do a tight tolerance to the data from the global dimensioning system, which now constrains the entire board.
Or, if they need perfect coplanarity on a BGA part for good BGA mounting, they’ll put co-planarity back over the entire board where they don't need it, because regular chips, gull-wings, and so on don't need the same amount of coplanarity as a BGA—or they'll try to hold layer tolerances: “I need a 2-mil layer plus or minus 10%,” because they know that 10% is normal for tolerance, but they missed the part of the spec that says 10% or 1 mil, whichever is greater. Fabricators can't hold that tight a layer-to-layer tolerance when it's below a certain layer thickness.
Below about a 10-mil thickness, the best fabricators can do layer-to-layer is 1 mil for nominal processing; If you want to hold a tighter tolerance, you're paying for 100 to get five boards. That’s just a couple of examples. Another is overly tight hole tolerances: “I want to have 150-mil diameter hole ±1 mil.” Again, it's unreasonable, right?
To read the rest of this interview, which appeared in the November 2023 issue of Design007 Magazine, click here.
Testimonial
"Our marketing partnership with I-Connect007 is already delivering. Just a day after our press release went live, we received a direct inquiry about our updated products!"
Rachael Temple - AlltematedSuggested Items
Creating a Design Constraint Strategy
07/24/2025 | I-Connect007 Editorial TeamMost designers learn how to set their design constraints through trial and error. EDA vendors’ guidelines explain how to use their particular tools’ constraints, and IPC standards offer a roadmap, but PCB designers usually develop their own unique styles for setting constraints. Is there a set of best practices for setting constraints? That’s what I asked Global Electronics Association design instructor Kris Moyer, who covers design constraints in his classes.
Designers Notebook: Basic PCB Planning Criteria—Establishing Design Constraints
07/22/2025 | Vern Solberg -- Column: Designer's NotebookPrinted circuit board development flows more smoothly when all critical issues are predefined and understood from the start. As a basic planning strategy, the designer must first consider the product performance criteria, then determine the specific industry standards or specifications that the product must meet. Planning also includes a review of all significant issues that may affect the product’s manufacture, performance, reliability, overall quality, and safety.
Copper Price Surge Raises Alarms for Electronics
07/15/2025 | Global Electronics Association Advocacy and Government Relations TeamThe copper market is experiencing major turbulence in the wake of U.S. President Donald Trump’s announcement of a 50% tariff on imported copper effective Aug. 1. Recent news reports, including from the New York Times, sent U.S. copper futures soaring to record highs, climbing nearly 13% in a single day as manufacturers braced for supply shocks and surging costs.
Digital Twin Concept in Copper Electroplating Process Performance
07/11/2025 | Aga Franczak, Robrecht Belis, Elsyca N.V.PCB manufacturing involves transforming a design into a physical board while meeting specific requirements. Understanding these design specifications is crucial, as they directly impact the PCB's fabrication process, performance, and yield rate. One key design specification is copper thieving—the addition of “dummy” pads across the surface that are plated along with the features designed on the outer layers. The purpose of the process is to provide a uniform distribution of copper across the outer layers to make the plating current density and plating in the holes more uniform.
Gorilla Circuits Elevates PCB Precision with Schmoll’s Optiflex II Alignment System
06/23/2025 | Schmoll MaschinenGorilla Circuits, a leading PCB manufacturer based in Silicon Valley, has enhanced its production capabilities with the addition of Schmoll Maschinen’s Optiflex II Post-Etch Punch system—bringing a new level of precision to multilayer board fabrication.