-
- News
- Books
Featured Books
- design007 Magazine
Latest Issues
Current IssueShowing Some Constraint
A strong design constraint strategy carefully balances a wide range of electrical and manufacturing trade-offs. This month, we explore the key requirements, common challenges, and best practices behind building an effective constraint strategy.
All About That Route
Most designers favor manual routing, but today's interactive autorouters may be changing designers' minds by allowing users more direct control. In this issue, our expert contributors discuss a variety of manual and autorouting strategies.
Creating the Ideal Data Package
Why is it so difficult to create the ideal data package? Many of these simple errors can be alleviated by paying attention to detail—and knowing what issues to look out for. So, this month, our experts weigh in on the best practices for creating the ideal design data package for your design.
- Articles
- Columns
- Links
- Media kit
||| MENU - design007 Magazine
Checking In With ICAPE Group
April 3, 2024 | Nolan Johnson, I-Connect007Estimated reading time: 2 minutes
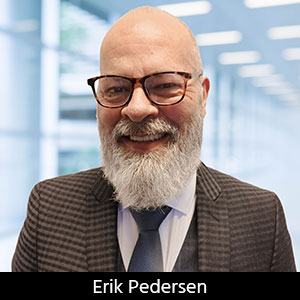
ICAPE Group’s field application engineer Erik Pederson drills down on sustainability, supply chain resiliency, and what value engineering really looks like in this exclusive interview. Founded in 1999, European-based ICAPE Group provides 21 million printed circuit boards and over six million technical parts to manufacturers every month. With 30 PCB manufacturing partners globally and 50 partners providing a wide array of technical parts, ICAPE Group has operations in China, Taiwan, Thailand, South Korea, Vietnam, South Africa, Europe, Mexico, and the United States. The company also focuses on the value proposition for its customers.
Sustainability
Nolan Johnson: How does ICAPE Group incorporate sustainable practices into manufacturing printed circuit boards?
Erik Pederson: There are many things that we do in the process of manufacturing a PCB that focuses on sustainability. PCB fabricators reclaim precious metals from waste and have done so for many years, sending it out to salvage companies that reclaim the metals. Regarding epoxy fiberglass laminate, we can grind it down to small particles that can be used as filler material in things like construction and concrete. As far as the processes themselves, we minimize waste and reclaim materials in as many steps as possible. On the electrolytic copper plating line, when the small copper balls (anodes) are sufficiently depleted, we collect them and send them to salvage for recovery. It is also common to collect router dust from drilling and routing to reclaim especially the gold particles. We reclaim the HASL and precious metals from rinsing during the wet processes. In the etch process, the spent etchant is treated to remove the copper, which is also recovered. This has all been going on for many years, but for someone unfamiliar with the fabrication process, it is important to educate them on all we do to reduce waste.
Johnson: Today, sustainability is not something we only think about during the manufacturing process. PCB fabricators have been focused on environmental sustainability, reducing waste, and maximizing ROI in many ways for decades. Working toward better sustainability really should start long before the board arrives at the PCB shop, correct?
Pederson: That is correct, Nolan. Probably the most important thing we do is to work on sustainability with our customers at the design stage. What are the most (ENIG) and least impactful (OSP) surface treatments to the environment? What is the cost? We also promote the use of halogen-free material. It is my personal belief that customers should pay more attention here. The halogens used to make the fire-retardant materials remain even when you grind down the waste materials. They are harmful to the environment. Today, there are halogen-free materials that have as good a performance as halogen materials, but they cost 20–30% more. But if most PCB makers (and OEMs) would use halogen-free material, the market would drive the price down and they would become more common, addressing a significant environmental issue. One example is NOKIA and Samsung requiring halogen-free material for their PCBs.
To read this entire conversation, which appeared in the March 2024 issue of PCB007 Magazine, click here.
Suggested Items
IBIDEN Selected for Multiple MSCI ESG Indexes for 2025
07/14/2025 | IBIDENIBIDEN Co, Ltd. is pleased to announce that it has been selected for inclusion in MSCI Inc.'s MSCI Selection Indexes (formerly the MSCI ESG Leaders Indexes), MSCI Japan ESG Select Leaders Index, and MSCI Nihonkabu ESG Select Leaders Index.
Rogers Corporation Announces CEO Transition
07/14/2025 | Rogers CorporationThe Board of Directors of Rogers Corporation announced that Colin Gouveia has left his position as President and CEO and has resigned from the Board on July 12, 2025.
Maybank Becomes First Southeast Asian Bank to Grant Sustainability-Linked Loan to Austria’s AT&S
07/14/2025 | AT&SMaybank announced it is granting a Sustainability-Linked Loan (SLL) amounting to USD150 million to Austria Technologie & Systemtechnik Malaysia (AT&S Malaysia).
PCBAA’s David Schild: Where U.S. Electronics Manufacturing Stands Today
07/14/2025 | Marcy LaRont, I-Connect007As the U.S. Congress looks toward a summer break, David Schild of PCBAA discusses the growing momentum in U.S. electronics manufacturing policy, emphasizing bipartisan support for reshoring efforts, the importance of targeted tax incentives, and the challenges posed by global competition. He highlights PCBAA’s growth, advocacy on Capitol Hill, and the need for sustained investment to revitalize the PCB industry.
Digital Twin Concept in Copper Electroplating Process Performance
07/11/2025 | Aga Franczak, Robrecht Belis, Elsyca N.V.PCB manufacturing involves transforming a design into a physical board while meeting specific requirements. Understanding these design specifications is crucial, as they directly impact the PCB's fabrication process, performance, and yield rate. One key design specification is copper thieving—the addition of “dummy” pads across the surface that are plated along with the features designed on the outer layers. The purpose of the process is to provide a uniform distribution of copper across the outer layers to make the plating current density and plating in the holes more uniform.