-
- News
- Books
Featured Books
- design007 Magazine
Latest Issues
Current IssueShowing Some Constraint
A strong design constraint strategy carefully balances a wide range of electrical and manufacturing trade-offs. This month, we explore the key requirements, common challenges, and best practices behind building an effective constraint strategy.
All About That Route
Most designers favor manual routing, but today's interactive autorouters may be changing designers' minds by allowing users more direct control. In this issue, our expert contributors discuss a variety of manual and autorouting strategies.
Creating the Ideal Data Package
Why is it so difficult to create the ideal data package? Many of these simple errors can be alleviated by paying attention to detail—and knowing what issues to look out for. So, this month, our experts weigh in on the best practices for creating the ideal design data package for your design.
- Articles
- Columns
- Links
- Media kit
||| MENU - design007 Magazine
Podcast Review: On the Line with… Designing for Reality
May 9, 2024 | Duane Benson, Positive Edge LLCEstimated reading time: 6 minutes
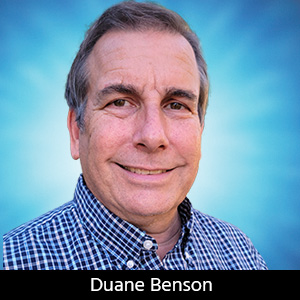
As a technologist, if I were forced to come up with just one recurring theme that I might call a professional “nemesis,” it would be the difference between theory and reality. A lot of technology we have at our disposal works well in theory but falls short when reality hits. That’s not the only reason I chose to listen to and review On the Line with… Designing for Reality, featuring a series of conversations with ASC Sunstone’s Matt Stevenson, but it certainly helped that the title caught my eye.
I have decades of experience in electronics design and manufacturing, including nearly 20 years in a leading quick-turn PCB assembly company. In that time, I have found that the pedigree of the engineer and the stature of the company sending in a design to be manufactured has little correlation to the quality and manufacturability of the product. Big company, small company, university, start-up designer, degreed electronics engineer or self-taught electronics designer—it doesn’t seem to matter. All are subject to the same traps, and all are as capable of making successful or failed designs as any other. The most common failures I have run across relate to inadequate consideration of the reality of manufacturing constraints. In this podcast, Matt dives into the reality of the design and manufacturing process and does his best to enlighten listeners to what they need to know to create designs that are manufacturable under real-world conditions.
Episode 1: Designing for Reality—What Is It?
Matt’s first episode, moderated by I-Connect007’s Nolan Johnson, starts off with a bit of a recap of Matt’s book of the same name. I’ve read the book and it’s worth reading. At the beginning of this episode, Matt talks about the importance to an electronics designer of understanding their manufacturing partners. I cannot agree more. A solid design on paper is a good thing. However, it is nothing until it has been built up and is working. Matt states that manufacturability should be “the goal of the lion’s share of design,” and I strongly agree. An unmanufacturable design is not a design. It is time and money wasted.
Yes, it’s about chemistry and physics.
Matt mentions how much he enjoys giving factory tours and that he likes to discuss the physics and chemistry involved in fabricating printed circuit boards. I start to get really interested when basic sciences are called out. It’s not an absolute requirement to know about what’s beneath the technology you are using, but I have always found that end designs are easier when I do understand why and how the electrons are moving around.
It’s clear that both Matt and Nolan understand the technology they are discussing. They deliver information in an easy conversational style. It’s also evident that Matt is, first and foremost, an engineer and a builder of things. I find it refreshing when information and content get priority over gloss and polish. This podcast is simply two very knowledgeable people trying to help electronics designers by giving insight into the manufacturing process.
Episode 2: The Design Process
Ultimately, the manufacturing process is an exercise in information sharing. You, the designer, need to pass all pertinent aspects of the design to your manufacturing partners, and the manufacturers need to pass information about their processes to you. Matt starts Episode 2 with a discussion about design for manufacturing (DFM) tools.
The DFM tool is essentially an automated way for the manufacturer to communicate process requirements to designers. After the design is complete and the DFM checks have been run, you need to accurately communicate your design to the manufacturing partner. The manufacturing files are the primary tool you have at your disposal to deliver your design. Matt gives pros and cons of different formats and notes the formats that ASC Sunstone prefers.
Episode 3: CAM, Materials, and Imaging
If you’ve ever looked at a circuit board and wondered how the PCB fab shop built it, this episode is for you. Matt starts explaining the process with the yellow light of photoresist imaging. This is one of the shorter episodes in the set, but it gives an understanding of the imaging and etch process. In 15 minutes, you will have a better understanding of why “space and trace” dimensions are so important. You’ll hear about optical limits, laser direct imaging and how both technologies work toward giving you a reliable design.
Episode 4: Lamination
The title “Lamination” doesn’t really do justice to the subject of this episode. This installment is about putting together the layers of the circuit board. Matt starts by discussing registration—keeping the layers aligned with each other. While you, as the designer, may not have much effect on registration, an understanding of what goes into lining up the PCB layers will help you know what is important when laying out multilayer designs. Matt’s knowledge of the process should also give you confidence that if you have done your job right, he will as well.
Matt gives advice on reducing the opportunities for error. Fab shops can build high-layer-count boards, but reducing the number of layers when possible, using larger vias if possible, and considering what is going on between the top and bottom surfaces will help ensure a successful design.
Episode 5: The Intricacies of PCB Drilling
Before I worked in manufacturing, as a circuit board designer vias were simply a way to get a signal from one layer to another. I called out one drill size for all signals, another for power, and gave it little thought beyond that. After I set my professional self into a manufacturing facility, I quickly learned how much more there is to the humble drill hole, especially in high performance designs. Matt covers this subject and more in this segment. There is a lot more than just drills here.
Takeaways
I hope I haven’t given away too much of the content. If I have, there are seven more episodes to go, so there are plenty of unspoiled episodes still to come. Most are around 25 minutes, so it’s something you can easily listen to over lunch or on your drive to work. (Click here to listen.)
The real takeaway from the series is to think beyond just the electronic circuit. Design really needs to be a holistic activity that considers all aspects of the product from day one. In the same way that you need to consider the environmental conditions your product will need to operate under, you also need to consider the manufacturing shops where it will be built. It’s not a great design if it won’t function under real-world conditions, and it’s not a great design if it can’t be reliably built.
Ideally, product development is a partnership between the design team, board fabrication house, and assembly manufacturer. It’s a balance between pushing design limits and reducing risk by backing off from those limits when possible. Knowing your manufacturing partners well will contribute to the project's ultimate success.
Duane Benson is a technology journalist and consultant operating as Positive Edge LLC. He has 30+ years of experience in the electronics design and manufacturing industry as a developer, executive, speaker, and writer. You can reach Duane at duane@positiveedge.today.
Suggested Items
Meet the Author Podcast: Martyn Gaudion Unpacks the Secrets of High-Speed PCB Design
07/10/2025 | I-Connect007In this special Meet the Author episode of the On the Line with… podcast, Nolan Johnson sits down with Martyn Gaudion, signal integrity expert, managing director of Polar Instruments, and three-time author in I-Connect007’s popular The Printed Circuit Designer’s Guide to... series.
Showing Some Constraint: Design007 Magazine July 2025
07/10/2025 | I-Connect007 Editorial TeamA robust design constraint strategy balances dozens of electrical and manufacturing trade-offs. This month, we focus on design constraints—the requirements, challenges, and best practices for setting up the right constraint strategy.
Elementary, Mr. Watson: Rein in Your Design Constraints
07/10/2025 | John Watson -- Column: Elementary, Mr. WatsonI remember the long hours spent at the light table, carefully laying down black tape to shape each trace, cutting and aligning pads with surgical precision on sheets of Mylar. I often went home with nicks on my fingers from the X-Acto knives and bits of tape all over me. It was as much an art form as it was an engineering task—tactile and methodical, requiring the patience of a sculptor. A lot has changed in PCB design over the years.
TTCI Joins Printed Circuit Engineering Association to Strengthen Design-to-Test Collaboration and Workforce Development
07/09/2025 | The Test Connection Inc.The Test Connection Inc. (TTCI), a leading provider of electronic test and manufacturing solutions, is proud to announce its membership in the Printed Circuit Engineering Association (PCEA), further expanding the company’s efforts to support cross-functional collaboration, industry standards, and technical education in the printed circuit design and manufacturing community.
Bell to Build X-Plane for Phase 2 of DARPA Speed and Runway Independent Technologies (SPRINT) X-Plane Program
07/09/2025 | Bell Textron Inc.Bell Textron Inc., a Textron Inc. company, has been down-selected for Phase 2 of Defense Advanced Research Projects Agency (DARPA) Speed and Runway Independent Technologies (SPRINT) X-Plane program with the objective to complete design, construction, ground testing and certification of an X-plane demonstrator.