-
- News
- Books
Featured Books
- design007 Magazine
Latest Issues
Current IssueShowing Some Constraint
A strong design constraint strategy carefully balances a wide range of electrical and manufacturing trade-offs. This month, we explore the key requirements, common challenges, and best practices behind building an effective constraint strategy.
All About That Route
Most designers favor manual routing, but today's interactive autorouters may be changing designers' minds by allowing users more direct control. In this issue, our expert contributors discuss a variety of manual and autorouting strategies.
Creating the Ideal Data Package
Why is it so difficult to create the ideal data package? Many of these simple errors can be alleviated by paying attention to detail—and knowing what issues to look out for. So, this month, our experts weigh in on the best practices for creating the ideal design data package for your design.
- Articles
- Columns
- Links
- Media kit
||| MENU - design007 Magazine
Estimated reading time: 2 minutes
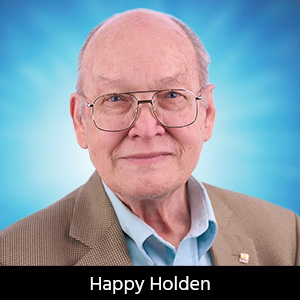
Contact Columnist Form
Happy’s Tech Talk #29: Bend-to-Install Semi-flex FR-4
A special case of rigid board applications is when you would like to bend the board but don’t need it to flex. We have called this case “bend-to-install” or sometimes “semi-flex” (Figure 1). Many electronics applications are in this class of assembly, as illustrated:
- Rigid board needing height adjustments
- Automotive lighting
- Industrial cameras
- Engine control units
- Hand-held portable units
Elements of the Bend-to-Install
The beauty of bend-to-install is that it is made from standard FR-4 materials and processes. What’s important are the design rules/constraints and the materials selected.
The important attribute is that the portion of the board that will be permanently bent will be thin, with thinner glass and a resin system that is not prone to cracking or that has been thinned by final fabrication.
Figure 2 illustrates some of the technology constraints of bend-to-install. The bend angle is less than 90° or between 90° and 180° while employing a flexible solder mask. The area to be bent is only one layer and is usually thinned and subject to a maximum of only three bend cycles during its life.
Materials
Over the years, several materials have been developed that are suitable for the bend-to-install rigid application. Foremost is the newer thin-spread glass prepregs used with the older DiCy-epoxy or cyanate-ester resins (RCC). RCCs are also suitable especially the new ZETA RCC with its C-stage polyimide-cured resin. Figure 3 highlights the newer thin glass cloths of 1015, 1027, and 1037 used in HDI laser-drillable prepregs.
Design Guidelines
It is best to follow a fabricator’s guidelines when designing a bend-to-install FR-4 board. Sample instructions from Unimicron and WUS are shown in Figure 4. The bend portion of the rigid board is usually thinned, either by stackup or by mechanically thinning that portion of the board. Depending on the flex thickness and bend radius, more than one bend can be achieved, but caution is the key here, as this is not a true flex. More design examples are shown in Figure 5.
Examples
Figure 6 illustrates three examples of bend-to-install from Würth-ELEKTRONIK. For many applications, the bend-to-install is ideal and provides the right 3D approach to product design. However, considering the life of the product and any repair considerations are important in the decision to use this approach compared to cable and connectors or traditional flex-rigid designs.
Summary
Although the semi-flex or bend-to-install is an old process, its use today is still practical. The newer, thin laminates and less stiff resin systems make this an attractive alternative. Many of these resin systems are also of lower dielectric constants and lower loss, making this design alternative suitable for very high frequency and some RF applications.
References
- WUS Presentation by Joe Dickson.
- “Semiflex Technology-Semiflex PCB, Smart Solutions for Optimized Integration,” Unimicron-Germany.
- “Rigid PCBs With Bending Zones,” Würth-ELEKTRONIK.
Happy Holden has worked in printed circuit technology since 1970 with Hewlett-Packard, NanYa Westwood, Merix, Foxconn, and Gentex. He is currently a contributing technical editor with I-Connect007, and the author of Automation and Advanced Procedures in PCB Fabrication, and 24 Essential Skills for Engineers.
This column originally appeared in the May 2024 issue of PCB007 Magazine.
More Columns from Happy’s Tech Talk
Happy’s Tech Talk #40: Factors in PTH Reliability—Hole VoidsHappy’s Tech Talk #39: PCBs Replace Motor Windings
Happy’s Tech Talk #38: Novel Metallization for UHDI
Happy’s Tech Talk #37: New Ultra HDI Materials
Happy’s Tech Talk #36: The LEGO Principle of Optical Assembly
Happy’s Tech Talk #35: Yields March to Design Rules
Happy’s Tech Talk #34: Producibility and Other Pseudo-metrics
Happy’s Tech Talk #33: Wet Process Management and Control