-
- News
- Books
Featured Books
- design007 Magazine
Latest Issues
Current IssueAll About That Route
Most designers favor manual routing, but today's interactive autorouters may be changing designers' minds by allowing users more direct control. In this issue, our expert contributors discuss a variety of manual and autorouting strategies.
Creating the Ideal Data Package
Why is it so difficult to create the ideal data package? Many of these simple errors can be alleviated by paying attention to detail—and knowing what issues to look out for. So, this month, our experts weigh in on the best practices for creating the ideal design data package for your design.
Designing Through the Noise
Our experts discuss the constantly evolving world of RF design, including the many tradeoffs, material considerations, and design tips and techniques that designers and design engineers need to know to succeed in this high-frequency realm.
- Articles
- Columns
- Links
- Media kit
||| MENU - design007 Magazine
Estimated reading time: 4 minutes
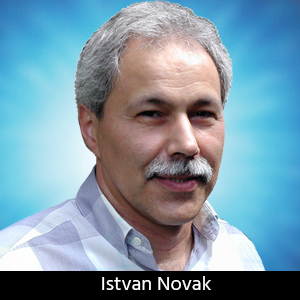
Quiet Power: An Evolution in PCB Design Costs
In this column, I want to cover my experiences, particularly where costs are concerned, with printed circuit boards from the 1960s to the present day. I grew up in an apartment building in downtown Budapest, where I began doing hobby projects building circuits from our kitchen table. Now, I’m lecturing about the most recent advances in signal integrity at Oxford University. We’ve come a long way. Over the decades, new technologies allowed users to have more layers, lower-loss dielectrics, fine-pitch surface connections, blind and buried vias, and HDI and HDI+ board constructions that allow us to design higher-performing systems. I expect this trend to continue.
Today, to connect multiple components into a compact circuit, we mount the components on a printed circuit board. But in the late 19th and early 20th centuries, people would wrap the leads of multiple components around nails and then hammer them into a wooden board. Household electronics, like vacuum-tube radios, amplifiers, and record players, all used a similar concept. The connection between components was done with wires, which were easy to replace if needed, and allowed connections in any direction. However, finding a particular wire in a chaotic three-dimensional wire blob was a real challenge. In the 1960s and ’70s, the main cost driver was the number of layers.
As the number of connections increased, so did the possibility of mis-wiring something and manufacturing also became time-consuming. The printed circuit board technology gradually emerged. (If you are interested in the history of printed circuit boards, see references 2 and 3.)
PCBs on Layers
In the early days, PCBs had one or two connecting layers, which required only a single dielectric sheet with a conducting layer on one or both sides. As a child, electronics fascinated me, and as soon as I could read, I turned to hobby magazines. Some described the new technology: Instead of discrete wires, they could draw connections of electronic circuits on copper-clad dielectric, and then etch away the copper where the connection wasn’t needed.
Later, I made little gadgets with transistors that I had purchased from a local hobby shop that sold materials, tools, and components for radio amateurs and hobbyists. With the non-market economy in those days, a transistor cost about the same price as six pounds of bread.
I built small portable radios on homemade printed circuits. The first attempts failed miserably. The hand-drawn pattern of ink that had to be baked before etching often peeled off too early. Once I discovered the correct temperature, length of baking over the kitchen gas range flame, and the proper etching time, the boards became more reliable. An example is shown in Figure 2. It is the audio amplifier of a battery-powered portable radio I built in the late ’60s4.
By the 1990s, glass-reinforced epoxy had replaced Paper Bakelite. The circuit complexity required several routing layers, plated through-holes, and blind and buried vias became available. Instead of manually drawing the pattern with ink, engineers used CAD software to perform the routing, while optimizing the etching and plating as carefully automated processes. The CPU module in Figure 3 (reproduced from Slide 125) had a 20"x8.5" 24-layer PCB. The board did not have blind or buried vias and used only standard low-cost FR-4 laminates, but it had selective gold plating. The price of the prototype bare boards in small quantities was around $600.
As production ramped up, prices came down. In the 2000s, the cost of bare PCBs with standard laminate materials, no blind or buried vias or special finishes, could be calculated by multiplying the board’s square footage by three times the number of metal layers. As an example, consider a board of 12"x8" with 10 layers and no special technology. This board size means a 0.8 square foot area. As each processed metal layer was estimated having a cost of $3, the estimated cost become 0.8 x 10 x 3, or $24.
Now, we’ve reached the 2020s. In another article6, I describe a simple six-layer board designed and built in 2023. The board was built with regular FR-4-like laminates and had four blind-via layers—two on the top and two on the bottom. The blind vias were copper-filled, but not planarized. Exposed copper was gold-plated. Because of the usual fixed setup costs commonly called non-recurrent expenses (NRE), the cost was a strong function of the number of boards in small quantities. The price of these boards was around $400 each.
As PCBs have evolved over the past 60 years, so have their associated costs. Now, with more efficient manufacturing, new technologies (such as 3D printing), and more automation, I expect to see even more changes in the costs of PCBs that will make them more efficient to produce, thus helping both the manufacturers and the consumers.
References
- “The Future of Power Integrity through the Eyes of Experience,” DesignCon 2023.
- History of PCB Innovations and Their Impact, Millennium Circuits Limited.
- Paul Eisner: My Life with the Printed Circuit, Associated University Press, 1989.
- “Istvan Novak: From behind the Iron Curtain,” PCM Magazine, October 2001, now available at edn.com.
- “Is Power Integrity the New Black Magic?” Cadence eLearning Forum, April 2021.
- “Introducing and Upcoming IEEE Packaging Benchmark,” Signal Integrity Journal, April 3, 2014.
This column originally appeared in the August 2024 issue of Design007 Magazine.
More Columns from Quiet Power
Quiet Power: The Effect on SI and PI Board PerformanceQuiet Power: 3D Effects in Power Distribution Networks
Quiet Power: Noise Mitigation in Power Planes
Quiet Power: Uncompensated DC Drop in Power Distribution Networks
Quiet Power: Ask the Experts—PDN Filters
Quiet Power: Friends and Enemies in Power Distribution
Quiet Power: Be Aware of Default Values in Circuit Simulators
Quiet Power: Do You Really Need That Ferrite Bead in the PDN?