-
-
News
News Highlights
- Books
Featured Books
- design007 Magazine
Latest Issues
Current IssueAll About That Route
Most designers favor manual routing, but today's interactive autorouters may be changing designers' minds by allowing users more direct control. In this issue, our expert contributors discuss a variety of manual and autorouting strategies.
Creating the Ideal Data Package
Why is it so difficult to create the ideal data package? Many of these simple errors can be alleviated by paying attention to detail—and knowing what issues to look out for. So, this month, our experts weigh in on the best practices for creating the ideal design data package for your design.
Designing Through the Noise
Our experts discuss the constantly evolving world of RF design, including the many tradeoffs, material considerations, and design tips and techniques that designers and design engineers need to know to succeed in this high-frequency realm.
- Articles
- Columns
- Links
- Media kit
||| MENU - design007 Magazine
Estimated reading time: 5 minutes
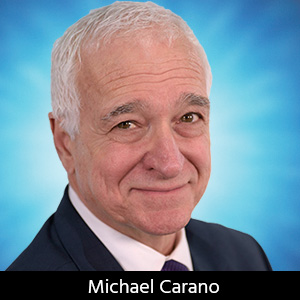
Contact Columnist Form
Trouble in Your Tank: Interconnect Defect—The Three Degrees of Separation
It has been well documented that, with a very expensive and complex printed circuit board, thermal and mechanical excursions often find weaknesses. A lack of robustness and poor process control often leads to the exploitation of those weaknesses.
An interconnect defect (ICD) often goes undetected until the printed circuit board reaches the final assembly stage or undergoes multiple thermal cycles, including interconnect stress tests or thermal shock. It is impossible to rework the ICD defect. But unlike voids, if detected in time, the panels can be reprocessed. However, ICDs are not always detected by Quality Control, mainly because the ICDs are rarely catastrophic failures. Rather, constant thermal cycling or the high temperatures of assembly operations cause a weakened interconnect to separate. Many engineers expect that performing one or two solder floats on plated coupons removed from panels will provide a sufficient QC check. Unfortunately, for the reasons cited, this often allows the problem to go undetected, much to the chagrin of many.
The Three Degrees of Separation
ICD is categorized as three types of inter-plane (IP) separation:
- Type 1: Separation of the electroless copper deposit from the interconnect
- Type 2: Separation of the electrolytic copper deposit from the electroless copper deposit but the electroless remains on the post
- Type 3: Cohesive failure of the electroless whereby the electroless copper deposit separates from itself
Note: There is often a fourth type that I will present in a future edition of this column. However, let’s try to understand the insidious nature of ICDs, also referred to as IP separation.
Why Do ICDs Often Go Undetected?
Figure 1 depicts an example of an ICD separation. One can detect a slight separation after the coupon was subjected to two solder floats at 550°C for 10 seconds. If not seen by section, the panel would easily have passed the electrical test. However, because of the weakness evident in the interconnect, continued thermal stresses and vibration of the PCB will most likely lead to an open. If in doubt about whether the defect is present, simply regrind and polish the potted coupon and inspect. Remember, inspect for ICD only after polishing the coupon. Do not etch the specimen. When a specimen is etched, a line of demarcation is often visible with electroless copper deposits. This line may lead one to conclude that it is a true ICD. Un-etched coupons must be used to detect the presence or absence of the defect.
Certainly, an ICD is not confined to just the IP. Blind vias can also exhibit a separation of the plated copper from the capture pad.
- ICD (IP separation) generally exhibits these underlying characteristics:
- Occurs during the stress of thermal shocks such as soldering. This produces expansion in the Z-axis and places strain on the copper in the hole wall.
- Most often seen on the first inner layer from either side of the board. (i.e., in a 12-layer board, the defect is seen on layers 2 and 11).
- The weakest bond breaks first.
- Under-cured boards are the most susceptible.
- Affected by board construction, PCBs with more resin, less copper, and lower Tg materials tend to show more expansion in the Z-axis.
- ICDs are often accompanied by hole wall pullaway, but not always.
There are many causes for IP separation. This is what makes this defect so difficult to pinpoint and eliminate. To further confuse the issue, one must first determine which of the three types of IP it is.
ICD Root Cause
Now, let’s dive into the root causes of the three primary types of ICDs.
Figure 2 depicts a Type 1 ICD. Type 1 is the most common. Since this defect involves so many processes and additional insight into the desmear/electroless copper process, I will defer the discussion on Type 1 to a future column.
Figure 3 shows a different type of ICD. Here, the electroless copper remains on the post or the interconnect. So, it’s not a Type 1. Instead, the separation is between the electrolytic copper and the electroless copper. Solving a particular issue requires looking at different process steps than previously looked at in Type 1 ICD.
It is important to stress Type 2 ICD is not an electroless copper/direct metallization/desmear problem. The electroless deposit in Figure 2 is firmly on the interconnect. The electrolytic copper has separated from the electroless copper.
The root cause of such a defect is the lack of adhesion of the electrolytic copper to the electroless copper. When encountering this problem, the first order of business is to determine if the PCB was panel- or pattern-plated. If it’s pattern-plated, did developer or photoresist residues remain on the interconnect? Was the developer solution at proper concentration, temperature, and pH? Is there resist lock-in? These problems will prevent the electrolytic copper from adhering to the electroless.
Other potential sources of Type 2 defects include:
- Oxidation at the interconnect
- Poor adhesion of electroplated copper to the electroless
Long hold times or rinsing with excessively hot water cause oxidation between operations. To improve adhesion, enough copper must be micro-etched. Typically, a 15–20 micro-inch etch is sufficient. The concern arises when 10 or fewer microinches of copper are removed. This is an insufficient amount of copper removal to provide enough anchoring sites for the copper electroplate. Since many PCB fabricators have reduced electroless copper plating thickness to reduce costs, they have been reluctant to be aggressive on the microetch. The result is insufficient anchoring of the electrolytic copper to the electroless. The solution is simple: If your electroless copper process cannot stand up to a microetch that removes 15–20 microinches, then find one that does.
Perhaps a less common ICD is a cohesive failure of the electroless copper deposit (Figure 4). Essentially, the copper deposit separates from itself. In Figure 4, the copper is both on the post and the electro-deposited copper, clearly separating from itself.
There are several causes for Type 3 defects:
- Excessively thick electroless copper deposits
- Lack of epitaxial copper deposit growth
- Excessive catalyzation
- Operating parameters favoring excessive copper deposition rates
All of these will interfere with the orderly growth of the electroless copper crystals. Essentially, the copper crystals cannot orient themselves as one crystalline coating over another (i.e., substrate). I liken this situation to a “spongy”-looking deposit. As the grain of the metal lacks epitaxy, the copper grains are disorganized and build up on other grains. This leads to a very weakened structure that will fracture.
Getting to the root cause of an ICD requires deep knowledge of processes and the ability to understand upstream and downstream processes. This is a complex issue that requires knowledge of the mechanics of electroless copper and subsequent additional processes and how each relates to the success or failure of the interconnect.
In a future column, I will explore Type 1 ICDs.
This column originally appeared in the September 2024 issue of PCB007 Magazine.
More Columns from Trouble in Your Tank
Trouble in Your Tank: Yield Improvement and ReliabilityTrouble in Your Tank: Causes of Plating Voids, Pre-electroless Copper
Trouble in Your Tank: Organic Addition Agents in Electrolytic Copper Plating
Trouble in Your Tank: Things You Can Do for Better Wet Process Control
Trouble in Your Tank: Processes to Support IC Substrates and Advanced Packaging, Part 5
Trouble in Your Tank: Materials for PWB Fabrication—Drillability and Metallization
Trouble in Your Tank: Supporting IC Substrates and Advanced Packaging, Part 5
Trouble in Your Tank: Electrodeposition of Copper, Part 6