-
- News
- Books
Featured Books
- pcb007 Magazine
Latest Issues
Current IssueInventing the Future with SEL
Two years after launching its state-of-the-art PCB facility, SEL shares lessons in vision, execution, and innovation, plus insights from industry icons and technology leaders shaping the future of PCB fabrication.
Sales: From Pitch to PO
From the first cold call to finally receiving that first purchase order, the July PCB007 Magazine breaks down some critical parts of the sales stack. To up your sales game, read on!
The Hole Truth: Via Integrity in an HDI World
From the drilled hole to registration across multiple sequential lamination cycles, to the quality of your copper plating, via reliability in an HDI world is becoming an ever-greater challenge. This month we look at “The Hole Truth,” from creating the “perfect” via to how you can assure via quality and reliability, the first time, every time.
- Articles
- Columns
- Links
- Media kit
||| MENU - pcb007 Magazine
The Cost-Benefit Analysis of Direct Metallization
October 21, 2024 | Carmichael Gugliotti, MacDermid AlphaEstimated reading time: 1 minute
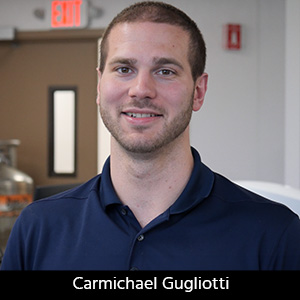
Carmichael Gugliotti of MacDermid Alpha discusses the innovative realm of direct metallization technology, its numerous applications, and significant advantages over traditional processes. Carmichael offers an in-depth look at how direct metallization, through developments such as Blackhole® and Shadow®, is revolutionizing PCB manufacturing by enhancing efficiency, sustainability, and cost-effectiveness. From its origins in the 1980s to its application in cutting-edge, high-density interconnects and its pivotal role in sustainability, this discussion sheds light on how direct metallization shapes the future of PCB manufacturing across various industries, including automotive, consumer electronics, and beyond.
Carmichael, please explain direct metallization technology generally, and why it is a better solution for some applications.
Carmichael Gugliotti: Direct metallization (DM) is a primary metallization process used to make PCB hole and via walls conductive prior to electrolytic copper plating. In DM processing, a coating of carbon or graphite is deposited on the surface and within the features of a bare PC board, creating a conductive pathway across the laminate areas. The coating is then etched from the exposed copper areas, leaving the conductive material on the laminate surfaces.
Electroless copper has been the primary metallization process for fabricators for a long time, even though early versions of the direct metallization process were developed in the 1980s. DM was originally deployed for use with double-sided, low-layer count applications. Through years of innovation, the process has been optimized for higher layer count, mSAP, and HDI designs.
Direct metallization is used in a wide range of applications, various end-use markets, and with common dielectric materials. It is used in rigid, rigid-flex, and flexible designs, though it is most widely deployed in plating flexible circuits. It is widely utilized in consumer electronics, such as hand-held devices, and in automotive, mil/aero, computing, industrial, and wireless applications, to name a few.
To read this entire conversation, which appeared in the October 2024 issue of PCB007 Magazine, click here.
Testimonial
"Advertising in PCB007 Magazine has been a great way to showcase our bare board testers to the right audience. The I-Connect007 team makes the process smooth and professional. We’re proud to be featured in such a trusted publication."
Klaus Koziol - atgSuggested Items
Marcy’s Musings: Destination Metallization
10/17/2024 | Marcy LaRont -- Column: Marcy's MusingsTo reach your intended destination, you must have some form of pathway or route upon which to travel. It is much the same with the metallized traces and features on a printed circuit board. They are how electrical signals and power are carried from one point to another in an electronic device. Copper is the most prevalent metal conductor, but other metals are also used to a lesser degree, including gold, silver, tin, and palladium.
PCB007 Magazine October 2024: Alternate Metallization Processes
10/16/2024 | I-Connect007 Editorial TeamTraditional electroless copper and electroless copper immersion gold have been primary PCB plating methods for decades. But alternative plating metals and processes have been introduced over the past few years as miniaturization and advanced packaging continue to develop taking us into new directions. In this issue of PCB007 Magazine, we examine the impact of alternate metallization methods giving a glimpse into how and when we will arrive at 'destination metallization'.
Trouble in Your Tank: Processes to Support IC Substrates and Advanced Packaging, Part 5
08/06/2024 | Michael Carano -- Column: Trouble in Your TankDirect metallization systems based on conductive graphite or carbon dispersion are quickly gaining acceptance throughout the world. Indeed, the environmental and productivity gains one can achieve with this process are outstanding. In today’s highly competitive and litigious environment, direct metallization reduces costs associated with compliance, waste treatment, and legal issues related to chemical exposure. What makes these processes leaders in the direct metallization space? This is detailed below.
Real Time with… THECA 2024: MacDermid Alpha Electronics Solutions–A Critical Comparison of Metallization Methods
08/01/2024 | Real Time with... THECACarmichael Gugliotti, product manager for primary metallization, MacDermid Alpha Electronics Solutions, describes his research—presented here at THECA—looking at reliability, process efficiency, and environmental sustainability. Learn about his findings in this interview.
Trouble in Your Tank: Supporting IC Substrates and Advanced Packaging, Part 5
03/19/2024 | Michael Carano -- Column: Trouble in Your TankDirect metallization systems based on conductive graphite or carbon dispersion are quickly gaining acceptance worldwide. Indeed, the environmental and productivity gains one can achieve with these processes are outstanding. In today’s highly competitive and litigious environment, direct metallization reduces costs associated with compliance, waste treatment, and legal issues related to chemical exposure. What makes these processes leaders in the direct metallization space?