-
- News
- Books
Featured Books
- design007 Magazine
Latest Issues
Current IssueProper Floor Planning
Floor planning decisions can make or break performance, manufacturability, and timelines. This month’s contributors weigh in with their best practices for proper floor planning and specific strategies to get it right.
Showing Some Constraint
A strong design constraint strategy carefully balances a wide range of electrical and manufacturing trade-offs. This month, we explore the key requirements, common challenges, and best practices behind building an effective constraint strategy.
All About That Route
Most designers favor manual routing, but today's interactive autorouters may be changing designers' minds by allowing users more direct control. In this issue, our expert contributors discuss a variety of manual and autorouting strategies.
- Articles
- Columns
- Links
- Media kit
||| MENU - design007 Magazine
Estimated reading time: 6 minutes
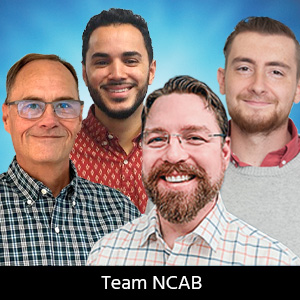
Fresh PCB Concepts: PCB Stackup Strategies—Minimizing Crosstalk and EMI for Signal Integrity
PCBs are critical components in almost every modern electronic device, but their design goes far beyond routing signals from one point to another. The stackup of a PCB (the arrangement of its layers) has a significant impact on signal integrity, electromagnetic interference (EMI), and crosstalk. The complexity of these issues grows exponentially as designs increase in speed, frequency, and complexity. Figure 1 depicts the electrical and magnetic fields produced by transmission lines when power is applied to the PCB. These fields interact with the surrounding signals, causing signal degradation. In this article, we'll break down the key strategies for designing an optimal PCB stackup to minimize crosstalk and EMI, ensuring the signals remain clean and the board operates as intended.
Understanding the Importance of Layer Stackups
The PCB stackup defines the layout of the layers, including signal layers, power and ground planes, and any internal layers for routing. Each layer serves a specific purpose, from maintaining signal integrity to noise shielding. Proper stackup design helps control impedance, minimizes crosstalk, and shields signals from external noise, which is critical for high-speed, high-frequency designs. With signal integrity, the key to a good stackup is understanding how to arrange the layers to support the circuit’s performance requirements while preventing noise and signal degradation. A well-designed stackup is essential for high-quality, cost-effective PCB manufacturing.
Minimizing Crosstalk: The Correct Layer Arrangement
Crosstalk is the unwanted coupling of signals between traces, which can lead to errors or interference, especially in high-speed circuits. Minimize crosstalk by isolating signal traces from each other and noise sources. Here are some design phase best practices to reduce crosstalk.
- Signal layer placement: Ideally, sandwich signal traces between solid ground or power planes. This configuration provides a stable return path for the signals and serves as a shield, helping to isolate the signal traces from each other.
- Ground and power planes: Use continuous ground and power planes as close as possible to signal layers. The closer these planes are to the signal traces, the better the shielding, which reduces the potential for crosstalk.
- Trace spacing: Increasing the distance between traces, particularly high-speed ones, is a straightforward way to reduce crosstalk. Increasing the physical spacing of traces lessens the chance of coupling, thus enhancing signal integrity.
Impedance Control for Clean Signals
Controlling impedance is critical to maintaining signal integrity, especially at high frequencies. Mismatches between the trace impedance and the impedance of the transmission medium can lead to signal reflections, which degrade signal quality.
- Microstrip vs. stripline: Deciding between microstrip and stripline routing can greatly impact signal integrity. A microstrip has the signal layer on the outer surface of the PCB, while a stripline places the signal between two ground planes. Stripline configurations generally offer better impedance control because the signal is more enclosed, providing less exposure to external factors that could interfere with the signal.
- Controlled impedance layers: Maintain consistent impedance by routing traces between power and ground planes.The trace width and the spacing to the reference plane will directly affect the impedance. Using simulation software for impedance analysis can help optimize trace dimensions.
Reducing EMI Through Proper Grounding and Shielding
EMI can wreak havoc on signal integrity, causing degradation and the potential failure of your circuit. Preventing EMI from disrupting your signals requires effective grounding and shielding. A well-designed PCB stackup can help minimize EMI and ensure a clean environment for signal transmission.
- Solid ground planes: Ground planes should be solid and free from breaks or voids. A continuous ground plane minimizes the potential for noise coupling in your signal traces. It also provides a low-impedance return path, which further reduces EMI.
- Shielding with planes: Shielding is crucial for high-speed designs. A ground plane between signal layers helps block noise from external sources and prevents signals from radiating into the environment.
- Minimizing layer-to-layer coupling: The closer the signal layers are to the ground or power planes, the more effective the shielding. Correctly position reference planes to minimize EMI coupling.
Optimizing for Manufacturability and Cost
While signal integrity is the priority, manufacturability, and cost-effectiveness also play a role in stackup design. Increasing the number of layers or using non-standard materials can quickly drive up costs and complexity.
Manufacturing Considerations:
- Layer count: Keep the number of layers to a minimum while ensuring performance. Additional layers increase the manufacturing cost and complexity. For many designs, four or six layers are enough, and anything beyond that should be considered only if necessary.
- Standard materials: Using standard PCB materials like FR-4 for most layers can keep costs in check. If higher performance is critical, advanced materials used in high-frequency designs are worth considering; however, evaluate the associated trade-offs.
- Standard copper thickness: Avoid non-standard copper thicknesses unless required by the design. Custom copper thicknesses can result in longer lead times and higher costs.
Stackup Documentation for Clear Communication
A well-documented stackup drawing is essential for effective communication between the designer and the manufacturer. A well-documented stackup drawing minimizes misunderstandings, reduces manufacturing errors, and ensures consideration of all necessary details.
Layer arrangement: Specify the arrangement of signal layers, power, ground planes, and any internal layers. Ensure consistency between the stackup drawing and the PCB artwork.
- Copper thickness: List the copper thickness for each layer, especially for internal layers that may require specific thicknesses for impedance control.
- Material types and dielectric thickness: For designs requiring controlled impedance, specify the material types (e.g., FR-4, Rogers) and dielectric thicknesses.
- Impedance specifications: If impedance control is critical, provide detailed information about the required impedance values, trace widths, and the reference layers each trace will use.
- Drill and via Information: For complex designs involving blind or buried vias, include clear details about the drill and via structures, ensuring no uncertainties for the manufacturer.
Simulation and Testing: Verifying the Design
Following completion of the design stackup, it’s essential to run simulations to verify the design’s integrity. Tools such as Signal Integrity Workbench (SIW) or electromagnetic simulation software can model how signals will behave in your PCB stackup, helping you spot potential problems early in the design process.
- Run early simulations: Perform signal integrity analysis early in the design process to catch any impedance mismatches or crosstalk issues ahead of production. To get the best simulations, contact your PCB manufacturer.
- Test prototypes: Once the design is finalized and simulations run, create physical prototypes to validate the design in real-world conditions. Use time-domain reflectometers (TDRs) to test signal integrity. However, the PCBs can be tested by the manufacturer before shipping.
Conclusion
Designing a PCB stackup that minimizes crosstalk and EMI while ensuring signal integrity is essential for creating high-performance circuit boards. By selecting the right layer arrangements, controlling impedance, and using effective grounding and shielding techniques, you can reduce noise and ensure clean signal transmission. Optimizing for manufacturability and cost is equally important, but the goal is a stackup that meets the design requirements and performs reliably in real-world applications. With the right strategies and careful documentation, your PCB will be able to handle the most demanding electrical environments. I recommend always working with your PCB supplier early in the design phase to ensure optimization for every aspect of the design, particularly with complex designs.
Ryan Miller is a field applications engineer with NCAB Group.
More Columns from Fresh PCB Concepts
Fresh PCB Concepts: More Than Compliance—A Human-centered Sustainability ApproachFresh PCB Concepts: Assembly Challenges with Micro Components and Standard Solder Mask Practices
Fresh PCB Concepts: The Power of a Lunch & Learn for PCB Professionals
Fresh PCB Concepts: Key Considerations for Reliability, Performance, and Compliance in PCBs
Fresh PCB Concepts: Traceability in PCB Design
Fresh PCB Concepts: Tariffs and the Importance of a Diverse Supply Chain
Fresh PCB Concepts: PCB Plating Process Overview
Fresh PCB Concepts: PCB Design Essentials for Electric Vehicle Charging