-
- News
- Books
Featured Books
- design007 Magazine
Latest Issues
Current IssueShowing Some Constraint
A strong design constraint strategy carefully balances a wide range of electrical and manufacturing trade-offs. This month, we explore the key requirements, common challenges, and best practices behind building an effective constraint strategy.
All About That Route
Most designers favor manual routing, but today's interactive autorouters may be changing designers' minds by allowing users more direct control. In this issue, our expert contributors discuss a variety of manual and autorouting strategies.
Creating the Ideal Data Package
Why is it so difficult to create the ideal data package? Many of these simple errors can be alleviated by paying attention to detail—and knowing what issues to look out for. So, this month, our experts weigh in on the best practices for creating the ideal design data package for your design.
- Articles
- Columns
- Links
- Media kit
||| MENU - design007 Magazine
Estimated reading time: 4 minutes
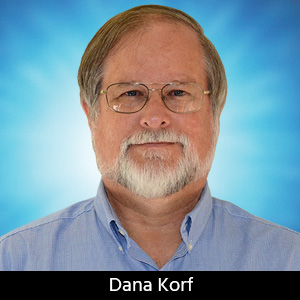
Dana on Data: The Missing AI-NPI Link
“AI enables designers to automate repetitive tasks and streamline the design process, reducing workflow and improving productivity. With AI, designers can work faster and generate more creative concepts than ever, drastically reducing production time.” (Microsoft Bing, March 8, 2025)
This year is yielding an extensive amount of communications, conferences, software updates, consultants, and news releases about how generative and re-generative artificial intelligence solutions and large language models are revolutionizing design, all with the intent to reduce new product introduction (NPI) cycle times.
The Gap
Design software companies are investing significant resources in using AI in an innovative and exciting way to reduce the schematic to PCB data package cycle time. As simulation software becomes more prevalent, AI and LLMs are required to compile and interpret to generate optimum solutions to match the increasingly complex signal integrity, EMI/EMC, and thermal requirements while keeping the cost low.
These tools allow the design to be completed in preparation for releasing manufacturing information to PCB fabricators and assemblers. All these requirements and dependencies are incorporated into the database.
Users (designers) then export the intelligent knowledge into a multi-document Gerber-based file documentation structure to provide fabrication data. In effect, the completed intelligent design file/model is then disassembled, without the assistance of AI, into multiple conflicting files and sent to production. The assumption is that the data files are perfect, don’t conflict with each other, and contain all the required information. Typically, 25% or more data packages have conflicting requirements between supplied documents and files, requiring manual (non-AI) interpretation.
The industry even sends a notoriously bad file (the netlist), a remnant from the 1990s, to ensure the graphical information was deconstructed properly. However, in reality, the 2020 version of the design export software doesn’t have this issue. The netlist format has not kept up with the design software and provides error messages for intentionally shorted and open nets, thus requiring a human to review the error log and contact the sender via email for resolution.
Once the data package is received by the fabricator, a team of skilled people opens the data files and tries to re-construct the PCB design per the provided documentation to create production files for manufacturing. But there is always something that doesn’t make sense (an extra layer in the Gerber file), clearly visible design errors (impedances that can’t be built with the provided constraints, legend ink on solderable surfaces), or the plant doesn’t have the capability to build the technology.
So, humans analyze the data and use their local databases and knowledge to propose potential solutions to current issues. No AI or LLMs have been developed to assist with this problem resolution. The issues are completed by sending emails with text, spreadsheets, and lots of pictures to the customer technical contact for resolution. Hours and days are lost during this resolution period.
The Solution
Fortunately, there is hope. IPC released the bi-directional IPC-2581 data format 21 years ago and has had several technology updates. This format is supported by most eCAD, DFM, and CAM software companies and a large consortium (ipc2581.com) composed of over 120 global companies. This team meets often each month to discuss issue resolution and proposed new features. A major update should be released this year.
- This is an intelligent data format. Only one file is required.
- No additional documentation is required to send design information.
- No netlist is required.
- TQ resolution information can be incorporated into the format (with responses)
- No stackup files. Multiple material stackup and impedance/loss models can be incorporated.
- IP protection is inherent to the structure.
- It’s digital twin-compatible.
Intelligent data residing in the eCAD systems can be directly output as an intelligent file for the manufacturer. The receiving engineering department doesn’t need to review several documents to re-enter the intelligence into rule-based engineering/CAM systems. When a person requires a paper drawing, it can be created by many software packages.
This format is compatible with an LLM AI-based system. The databases held separately by the designer and manufacturer can be linked via AI. The system can update repeated designer issues and perform automatic revision updates based on the IPC-2581 electronic feedback.
AI can be used to dramatically reduce the tooling time and increase design or customer specific trends/patterns. Automated production tooling and process quality results can be developed. (Portions of this path are commonly in place).
The Proposal
Companies that produce designs need to understand how much designer and NPI introduction time is lost and scrap produced due to paper-based design transfers with humans, not computers, making decisions. IPC needs to provide more visibility to design transfer. The recent IPC Technology Roadmap does not mention working on design transfer. They focus on just the Design Rule Checking element and new technology developments.
One IPC committee is updating a standard to combine multiple drawing standards into a single standard. This is in a world where drawings are not required to transfer design information anymore. We need OEMs to push the industry to use intelligent data for transfers so AI can be implemented.
Dana Korf is senior director of technology/FAE director at Victory Giant Technology in Huizhou City, Guangdong, China.
More Columns from Dana on Data
Dana on Data: Merging 2D Electrical, 3D Mechanical WorldsDana on Data: Resurrecting IPC Class 1
Dana on Data: The Evolution of Fabrication Drawing
Dana on Data: The Insane PCB DFM Process
Dana on Data: eCAD PCB Design Deficiencies
Dana on Data: Nuke the Netlist
Dana on Data: Simplify PCB Documentation
Dana on Data: IPC AME Standards Development Launched