-
- News
- Books
Featured Books
- pcb007 Magazine
Latest Issues
Current IssueInventing the Future with SEL
Two years after launching its state-of-the-art PCB facility, SEL shares lessons in vision, execution, and innovation, plus insights from industry icons and technology leaders shaping the future of PCB fabrication.
Sales: From Pitch to PO
From the first cold call to finally receiving that first purchase order, the July PCB007 Magazine breaks down some critical parts of the sales stack. To up your sales game, read on!
The Hole Truth: Via Integrity in an HDI World
From the drilled hole to registration across multiple sequential lamination cycles, to the quality of your copper plating, via reliability in an HDI world is becoming an ever-greater challenge. This month we look at “The Hole Truth,” from creating the “perfect” via to how you can assure via quality and reliability, the first time, every time.
- Articles
- Columns
- Links
- Media kit
||| MENU - pcb007 Magazine
Estimated reading time: 4 minutes
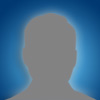
Contact Columnist Form
The Bleeding Edge: It's All about Pitch
By Robert Tarzwell with Ken Bahl - Sierra Proto Express
Two years ago, we wrote an article about looking in the crystal ball regarding the printed circuit business--the article received both kudos and criticism. We will admit, here and now, that the prediction of major change in the printed circuit business was quite wrong. The change is happening at a much faster rate than we had first thought! The fast ramp up of silicon advancement in packaging will force the printed circuit manufacturers to change the very way boards are made.
Silicon packaging is pushing the pitch down to as low as 0.125 mm (5 mils) for direct die attachment. The 0.125 mm 5 mil pitch is so small, a line of 1 mil or less is required to pass through the 1.75 mil pads with 1 mil vias for escaping paths. At a 0.25 mm, a 10 mil pitch, a 3.5 mil pad (with a 2 mil micro via) and a 1 mil line/1 and space will be needed to route escape signals. The move to such high technology will push every board shop to the limit and beyond. We have, in fact, received many calls recently from larger electronics companies inquiring about the availability of 10 micron lines and spaces. The solution to this advancement is the technology many, like Happy Holden, have toted for years--HDI.
Sierra Proto Express has realized that HDI and micro circuits is the only way to create the newer, high-technology micron featured circuits. The best current technology--drilled 5 mils holes and 1 oz. thick copper with 3 mil lines--will not allow a pitch below 0.4mm. A new method will be needed to reduce the size of the vias and pads and to create smaller line widths. To achieve the advanced technology required, the Micro Circuits Division of Sierra is ramping up technology to provide HDI circuits with micro vias as small as 2 mils in a 3.5 mil pad and under 1 mil lines. The division has just purchased two high resolution imaging units capable of 1/5 mil (5 micron) lines. Both exposure units are new to the PCB business--so new, in fact, we had them designed and manufactured exclusively for the company.
One can, of course, opt to not use silicon exposure units to image a PCB--they do not have a large enough format and most are not I line (365 nm). The typical silicon exposure stepper only has a 0.5 x 0.5 in. exposure area which is fine for the small silicon chips. The PCB micro exposure unit needs a significantly larger exposure area in the 6 x 6 area size and most chip carriers and small micro electronic circuits fit into a 4 x 4 area. Additionally, to manufacture less then 2 mil (50 micron) lines, special new bleeding edge ideas are needed in the dry film and etching area. Achieving 1 mil lines with acceptable yields are very difficult, but not impossible. To manufacture the tight below 1 mil via/pad registration, a different tooling and alignment system is utilized. If the via/pad registration moves around by more than 0.25 mil, a 2 mil via to a 3.5 mil pad cannot be achieved without breakout.
To utilize the typical 50 ohm impedance, used by all designers for a line width of 1 mil, a different dielectric material, other than FR4, must be used. When the dielectric thickness is calculated against the line, width problems can occur (Figure 1).
Figure 1: Normal best PCB technology.
Figure 2: Advanced micro line HDI technology.An important change to consider for 50 ohm impedance is that when the pitch decreases, the line and space will decrease, forcing the dielectric to correspondingly decrease in thickness (Figure 2).
Figure 3: Impedance line width measurements. Figure 3 shows that, as the pitch decreases for impedance controlled circuits, different materials, other than FR4, should be considered. The minimum prepreg thickness of an FR4 system is a 106 prepreg, at 2.0 to 2.4 mils depending on the type of laminate. This number relates to a minimum line width of 3 mils and a minimum pitch of 0.5 mm. A single 106 prepreg is not considered ideal due to problems associated with glass fibers. A single sheet of 106 can easily create pin holes, as well develop CAF, which can create shorts with use. A single sheet between opposing traces can cause shorts due to excessive resin flow. The single sheet dielectric layer will vary in impedance in areas where the glass bundles compress between opposing tracks--causing a higher Dk in that area.
Sierra has developed a very thin film dielectric--the film has very high voltage ratings of 4,000 volts per mil and is available in various thicknesses from 1 to 3 mil. The film prevents changes in the Dk and also stops any CAF from forming because it contains no fibers. Sierra will continue to advance the technology to finer lines and smaller vias--enabling engineers to soon utilize a 0.125 mm pitch design.
Bob Tarzwell, Director of Technology at Sierra Proto Express, has worked with Ken Bahl to introduce new bleeding edge, advanced circuit technology like lead-free, high reliable electronics, heat sinking technology and ultra fine lines to the world. Since selling his company in 2000, Bob has disseminated PCB high-tech to many companies as a consultant, and has written ten books on PCBs and car racing. He has three patent-pending applications in fine lines, high reliability and outer space PCBs. He is currently semi-retired in the Bahamas, spending his free time writing books, working on antique cars and deep sea fishing.
Ken Bahl, President of Sierra Proto Express (San Jose, CA), started in the PCB business in 1965 as a process engineer with Honeywell in New Hampshire. In 1986, Ken founded Sierra Proto Express, the PCB industry's leader in innovative bleeding edge technologies--dedicated to producing Tomorrow's Technology Today.
For more information, visit www.protoexpress.com.
More Columns from Various Archived Columns
Slash Sheet Chaos: Is What You See, What You Get?Moisture in Materials: Avoiding Process Gremlins
Material Witness: Beat the Heat--A Non-Math Intro to Thermal Properties
Material Witness: Considerations in Using TC Materials for PWBs
Material Witness: Are Your Materials Up to the Challenge?
Material Witness: Thermal Oxidation of Materials, Part I
Material Witness: Thermal Oxidation of Materials, Part II
Material Witness: R.I.P. Speedboard C