-
- News
- Books
Featured Books
- pcb007 Magazine
Latest Issues
Current IssueInventing the Future with SEL
Two years after launching its state-of-the-art PCB facility, SEL shares lessons in vision, execution, and innovation, plus insights from industry icons and technology leaders shaping the future of PCB fabrication.
Sales: From Pitch to PO
From the first cold call to finally receiving that first purchase order, the July PCB007 Magazine breaks down some critical parts of the sales stack. To up your sales game, read on!
The Hole Truth: Via Integrity in an HDI World
From the drilled hole to registration across multiple sequential lamination cycles, to the quality of your copper plating, via reliability in an HDI world is becoming an ever-greater challenge. This month we look at “The Hole Truth,” from creating the “perfect” via to how you can assure via quality and reliability, the first time, every time.
- Articles
- Columns
- Links
- Media kit
||| MENU - pcb007 Magazine
Estimated reading time: 4 minutes
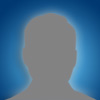
Contact Columnist Form
Material Witness: Are Your Materials Up to the Challenge?
Material Witness by Chet Guiles
Have you ever dropped your brand new cell phone? There is a "gee-whiz" dropping sensation in the pit of your stomach as you hear it bounce off the floor, or impact on the cement, or whatever. And it always seems a bit of a miracle that when you pick it up it still works. One of the reasons it still works is that the designers of cell phones build into their design criteria the assumption that we are going to drop them, and part of the design is that they have to be able to withstand the G-Shock of a one meter drop onto a hard concrete surface. The typical distance a phone falls is one meter, and I know, for example, based on my granddaughter's experience, that a 1 meter fall is enough to break the arm of a 12-year-old girl riding a skateboard. That's a lot of banging around. "What does it mean to us in terms of printed circuit material technology?" you may ask. "A 12-year-old kid is not a cell phone!" True, but the underlying physics of motion and impact are the same...
An apple dropped from one meter, Newton discovered, will fall in a manner governed in a mathematically definable manner by the force of gravity, and will attain a "final velocity" of about 4.4 meters/second, or roughly 14.4 feet/second. Apples, cell phones and 12-year-old girls all fall governed by the same gravitational force and, unless something acts to retard their fall, hit the ground at about the same speed. It's not the falling that breaks bones, bruises apples and damages cell phones--it's the stopping. The G-Force generated by an object falling at 4.4 meters/second is determined by how quickly it stops, or its "deceleration." If it stops, let's say, in a thousandth of a second, then the deceleration is 4.4 m/s divided by 0.001 or 4,400 m/sec². Divide that by one gravity (9.80665 m/sec²), and you wind up with a deceleration of about 4,500 G's!
When the little circuit board in that phone, which has a number of small devices mounted on it, is subject to a 4,500 G deceleration, the designers of the phone can calculate how much force will be generated that will attempt to shear those devices off the board or otherwise cause them to separate from their solder joints and become independent entities, at which time the phone stops working. "Can you hear me now?" Hence, the 1 meter drop test is a regular part of the design for a phone.
By the magic of finite element analysis and a lot of trial and error, many designers have determined that a copper peel strength of at about 8 lb/in is necessary to keep the G-shock of a 1 meter free fall from ripping the copper pads off the PWB on impact and rendering the phone "hors de combat." And for a conventional FR-4 material, an 8 lb/inch peel strength was fairly normal, so the whole issue of drop test failure was for a while somewhat quiescent. Now, though, several factors have entered into play and made this issue re-emerge as a potential issue.
Electrical demands on materials have changed. Higher data rates and frequencies of operation demand materials with lower dielectric constant and lower loss, so conventional FR-4 fades into the background. And the demand for materials suitable for lead-free solder usually includes higher Tg's and hence somewhat more rigid (read "brittle") materials. Combine that with the fact that lead-free solders are, by and large, much stiffer than their lead-tin predecessors, and you have the potential for a not so subtly changed dynamic.
The terminal velocity and G-shock will be the same, but the materials themselves will be different. The shock transmitted from the device to the copper pads on the PWB will be greater, because the nice soft lead-tin solder will not be there to dampen it. And the more tightly cured chemistries (permitting higher Tg's) of cost-effective "low dielectric constant/low loss" materials may mean that absolute values of peel strengths are not as high as those of conventional FR-4 to begin with, even in epoxy-based systems. The result is increased risk of drop-failures or other impacts related to material mechanical properties.
Beyond the basic physics, what is not well understood yet is the effect of thermal cycling, during manufacture and assembly, on the durability of copper pads on newer generations of materials whose low Dk and df values may be offset to some degree by their diminished physical properties, both at room temperature and at elevated temperatures. One new product under development at Arlon, a low loss "green" substrate (no brominated flame retardants) for instance, has a Dk of 3.7 and a loss of 0.0045 at 10 GHz, but it also has a high peel; strength that makes it potentially a good candidate for hand held high speed consumer electronics. Interestingly, while a widely used competitive material with lower copper values to begin with, exhibits significant reduction in copper peel at elevated temperature, the new Arlon product remains significantly higher in peel value at elevated temperatures, even with some of the lower profile copper foils that are used to improve loss characteristics for high frequency systems.
What's the bottom line here? It isn't to always specify Arlon's material, although that's never a bad idea, but that as you consider materials for use in your handheld devices you remember that there may be trade-offs between HF electrical performance and the physical properties you often take for granted from your experience from the old "FR-4" days.
Until next time.
Chet Guiles is a consultant for Arlon Electronic Materials.
About Arlon Arlon Electronic Materials Division, now part of Rogers Corporation (www.rogerscorp.com), is a major manufacturer of specialty high performance laminate and prepreg materials for use in a wide variety of printed circuit board (PCB) applications and in several distinctive markets. www.arlon-med.com
More Columns from Various Archived Columns
Slash Sheet Chaos: Is What You See, What You Get?Moisture in Materials: Avoiding Process Gremlins
Material Witness: Beat the Heat--A Non-Math Intro to Thermal Properties
Material Witness: Considerations in Using TC Materials for PWBs
Material Witness: Thermal Oxidation of Materials, Part I
Material Witness: Thermal Oxidation of Materials, Part II
Material Witness: R.I.P. Speedboard C
Conversations with...Integrated Micro-Electronics Inc.