-
- News
- Books
Featured Books
- pcb007 Magazine
Latest Issues
Current IssueInventing the Future with SEL
Two years after launching its state-of-the-art PCB facility, SEL shares lessons in vision, execution, and innovation, plus insights from industry icons and technology leaders shaping the future of PCB fabrication.
Sales: From Pitch to PO
From the first cold call to finally receiving that first purchase order, the July PCB007 Magazine breaks down some critical parts of the sales stack. To up your sales game, read on!
The Hole Truth: Via Integrity in an HDI World
From the drilled hole to registration across multiple sequential lamination cycles, to the quality of your copper plating, via reliability in an HDI world is becoming an ever-greater challenge. This month we look at “The Hole Truth,” from creating the “perfect” via to how you can assure via quality and reliability, the first time, every time.
- Articles
- Columns
- Links
- Media kit
||| MENU - pcb007 Magazine
Estimated reading time: 5 minutes
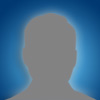
Contact Columnist Form
Material Witness: Beat the Heat--A Non-Math Intro to Thermal Properties
Material Witness by Chet Guiles
If you are designing, fabricating or using PWBs these days, you are aware of issues regarding the management of heat. In the process itself lead-free solder technology has resulted in incremental stresses on PTHs due to higher temperature excursions and issues with cracks in solders that are more brittle than their tin-lead ancestors. With PWBs getting smaller and devices more densely packed, the watt-density of many boards is such that significantly higher heat generation requires active measures to prevent development of excessive temperatures. And since most semiconductor devices exhibit a mean time to failure that is cut in half with every 10°C temperature increase, managing temperature is a critical element in product life expectancy.
Design strategies are based on several factors:
- Beating the Heat: For over 30 years, high temperature applications have used polyimide laminate and prepreg systems to provide device reliability in operating environments exceeding 200°C. Enhanced polyimide systems and newer lead-free compatible thermally conductive epoxy systems offer designers new approaches to maximizing reliability in tough operating environments.
- Surviving the Environment: How materials respond to cyclic thermal exposure remains a critical contributing factor in determining device reliability. Designing PWBs on materials that reduce or control thermal expansion will improve PTH reliability and reduce stress and fatigue on solder joints to SMT components.
- Removing the Heat: Many designs today continually push limits for heat transfer, resulting in high device operating temperatures. Newer PCB materials offer increased thermal conductivity to reduce peak operating temperatures and improve component life.
- Reducing the Heat: Reduced power usage (when possible) and the use of materials with lower dielectric loss will also incrementally reduce heat generated.
In simple terms, heat is a measure of molecular excitation resulting from the inefficient application of power (and hence current flow) in imperfect conductors. Work on superconductors is directed precisely at the idea of achieving materials exhibiting essentially no resistance to current flow. In "semiconductors" however, heat is generated whenever a device activates. In solid state DC to DC converters for example, solid state switches turn on and off at high rates and generate a lot of heat. If the heat cannot be removed from the immediate area of the device, temperature buildup will eventually damage or destroy it.
There are three basic ways of moving heat from a hot place to a colder place: Conduction (in which physical contact permits the molecular excitation to move energy from the hotter to the cooler body), convection (in which a fluid, such as air, or in extreme cases even liquid nitrogen, absorbs some of the energy of the hot body and carries it away either by convection currents, or by forced convection, such as by the use of a fan or a pump) and radiation (in which the energy of the system is removed by the transmission into the atmosphere of electromagnetic or thermal radiation).
Just to focus on conductivity for a few minutes (since for most PWBs the use of a heat sink or thermal vias or other thermally conductive materials is the method of choice for removal of heat) we need to ask what properties of a material used for a heat sink, or to bond a heat sink to a PWB, are important and why.
All materials have some degree of thermal conductivity (Tc). Thermal conductivity is a measure of the rate at which heat will pass through a mass of that material. The thermal conductivity of materials is measured in terms of Watts/meter-K where watts are a measure of heat flow as a function of time, K is the temperature difference between the hot and cold bodies in terms of Kelvin (an absolute temperature scale) and meters actually stands for "square meters/meters," which is the ratio of area to thickness. For any material the actual amount of heat flow is determined by a factor we call Tc (thermal conductivity) and the area and thickness of the material itself. For a given area (we can't arbitrarily make our PWBs larger to manage heat!) a higher Tc and a thinner material will result in more heat being transferred in any given time.
Another factor weighs heavily on the matter of actual heat transfer, and that is what we call interfacial thermal resistance. The best heat transfer takes place when the heat sink (let's think practically now about PWBs with aluminum heat sinks) is intimately in contact with the PWB. Unless both your board and your heat sink are machined to the smoothness of Jo-Blocks, that contact will not be particularly intimate, and so you depend on the material by which you bond the heat sink to the PWB to achieve an intimate bond. But in many cases the interface material (typically a prepreg in MLB applications) has a much lower Tc (perhaps as low as 0.2 W/m-K) than the heat sink itself (since aluminum has a Tc of about 250 W/m-K). Moreover, while the PWB may have an array of thermal vias (copper plated through holes) that will move heat quickly from the board surface to the heat sink (copper has a Tc of about 425 W/m-K), the interface material can be so much lower in Tc that it will be the "weakest link" in the system.
So the "ideal" prepreg for bonding heat sinks to PWBs will be a product with a high thermal conductivity (at least 1 W/m-K or even higher) that is as thin as possible while still being able to flow into any irregularities in the board and the heat sink to achieve a thin, intimate interface that will bond well (we like to be able to achieve lap shear values of 700 psi to properly prepared aluminum) and still be an effective dielectric (because you really don't want to connect your board electrically to the heat sink). An even better solution would be to use this same material in the body of the PWB itself, since then there would be additional heat dissipation radially around thermal vias and through the body of the board itself in addition to the bonded external heat sink. The result, of course, has to be a significant reduction of temperature on the device itself.
Next time we will talk about the kinds of material used for making thermally conductive connections and some of the practical considerations you will need to take into account in design and fabrication. Arlon's Thermal Management Guide contains additional material that you will hopefully find useful as you get deeper into heat management issues.
Chet Guiles is a consultant for Arlon Electronic Materials.
About Arlon Arlon Electronic Materials Division, now part of Rogers Corporation (www.rogerscorp.com), is a major manufacturer of specialty high performance laminate and prepreg materials for use in a wide variety of printed circuit board (PCB) applications and in several distinctive markets. www.arlon-med.com
More Columns from Various Archived Columns
Slash Sheet Chaos: Is What You See, What You Get?Moisture in Materials: Avoiding Process Gremlins
Material Witness: Considerations in Using TC Materials for PWBs
Material Witness: Are Your Materials Up to the Challenge?
Material Witness: Thermal Oxidation of Materials, Part I
Material Witness: Thermal Oxidation of Materials, Part II
Material Witness: R.I.P. Speedboard C
Conversations with...Integrated Micro-Electronics Inc.