-
- News
- Books
Featured Books
- pcb007 Magazine
Latest Issues
Current IssueInventing the Future with SEL
Two years after launching its state-of-the-art PCB facility, SEL shares lessons in vision, execution, and innovation, plus insights from industry icons and technology leaders shaping the future of PCB fabrication.
Sales: From Pitch to PO
From the first cold call to finally receiving that first purchase order, the July PCB007 Magazine breaks down some critical parts of the sales stack. To up your sales game, read on!
The Hole Truth: Via Integrity in an HDI World
From the drilled hole to registration across multiple sequential lamination cycles, to the quality of your copper plating, via reliability in an HDI world is becoming an ever-greater challenge. This month we look at “The Hole Truth,” from creating the “perfect” via to how you can assure via quality and reliability, the first time, every time.
- Articles
- Columns
- Links
- Media kit
||| MENU - pcb007 Magazine
Estimated reading time: 4 minutes
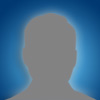
Contact Columnist Form
Material Witness: Considerations in Using TC Materials for PWBs
Material Witness by Chet Guiles
It's one thing to know you have to reduce the temperature at active devices mounted on a PWB, but it's another altogether to do so while maintaining a "normal" manufacturing and assembly process for circuit boards. In our previous discussion of thermally conductive materials (Beat the Heat: A Non-Math Intro to Thermal Properties) we summarized some of the important properties of laminates and prepregs that would be ideal for such applications: High thermal conductivity (at least 1 W/m-K, and preferably higher), minimum thickness and the ability to flow and fill the interface to minimize thermal impedance. This time we will talk about some of the practical issues involved.Two different applications of thermally conductive prepregs exist: 1) Use as interface bonding layers between a PWB and a heat sink; and 2) Use as part of a total thermally conductive package in which the entire PWB is composed of thermally conductive materials.In the use of thermally conductive prepregs (whether standard or so-called "low-flow") as bond layers between a PWB and, for instance, an aluminum heat sink, the critical issues will be (in addition to thermal conductivity) bond to both the aluminum and the PWB, and the completeness of the wetting to both surfaces to minimize thermal resistance due to any trapped air, imperfect mating of the surfaces, etc. Rheologically, highly thermally conductive materials will be different than standard unfilled FR-4 in that they will have substantially higher minimum melt viscosities by at least an order of magnitude (10,000 to 15,000 poise versus about 1,000 poise), as the chart below indicates.
In practical terms, this will mean that to achieve optimum bonding and complete wetting to the bonding surfaces, pressures used will tend to be higher than for an equivalent unfilled conventional epoxy system. The actual pressures used will depend on how much unevenness there is between the heat sink and the board, whether there are circuits on the underside of the board that also have to be filled, etc. If there will be cutouts in the heat sink, the pressure used will have to be balanced so as not to fill cutout areas while still achieving an acceptable fill and bond.Bonding a filled system to the aluminum heat sink and the PWB requires that both surfaces be clean, and that the aluminum preferably be sandblasted or abraded and any grease or fingerprint residue be removed (wiping with dry isopropyl alcohol is normally a good way to do a final clean and dry of the aluminum bonding surface). Lap shear testing for bond to aluminum has indicated that values of 750 psi, or greater, will ensure a good bond that will resist normal thermal cycling or shock.These same considerations will be present to some degree with bonding layers together with prepreg in an all-conductive MLB. Because these materials tend to be highly filled and have reduced flow (higher minimum melt viscosity) they will take more effort in filling circuitry on inner layers, and especially in filling vias or clearance holes in heavy metal inner layers. Here again, additional pressure and a higher rate of heatup will help to get more flow from any given system, but it may be necessary to pre-fill clearances in very thick metal layers or in thicker board sections with high aspect ratio vias, such as in complex sequentially laminated PWBs. Interlaminar bonds in highly filled materials will not be as great as with unfilled epoxy, and this should not normally present any major problem. Avoid the old standby of trying to peel them apart by inserting an X-acto knife at the edge and twisting. The ability to force layers apart does not indicate unacceptable bond. When polyimides were first introduced during the late Jurassic Period (when I first joined this industry) there was concern about interlaminar bond because it was possible to peel multilayer boards apart, whereas it was nearly impossible with standard epoxies. Accepting that this is a difference rather than a defect is an important step in moving forward with thermally conductive technology today, as it was for polyimides 30 years ago.You will not be able to drill as many holes in a board with a highly filled system as with an unfilled FR-4. While every effort is made to use filler materials that are as nonabrasive as possible, our objective is increased thermal conductivity and we need to use materials of a type and quantity such that the product will fulfill that necessary condition. Conditions that work well for filled materials and give optimum drill life usually include slower drill surface speeds.
Chet Guiles is a consultant for Arlon Electronic Materials.
About Arlon Arlon Electronic Materials Division, now part of Rogers Corporation (www.rogerscorp.com), is a major manufacturer of specialty high performance laminate and prepreg materials for use in a wide variety of printed circuit board (PCB) applications and in several distinctive markets. www.arlon-med.com
More Columns from Various Archived Columns
Slash Sheet Chaos: Is What You See, What You Get?Moisture in Materials: Avoiding Process Gremlins
Material Witness: Beat the Heat--A Non-Math Intro to Thermal Properties
Material Witness: Are Your Materials Up to the Challenge?
Material Witness: Thermal Oxidation of Materials, Part I
Material Witness: Thermal Oxidation of Materials, Part II
Material Witness: R.I.P. Speedboard C
Conversations with...Integrated Micro-Electronics Inc.