-
- News
- Books
Featured Books
- pcb007 Magazine
Latest Issues
Current IssueInventing the Future with SEL
Two years after launching its state-of-the-art PCB facility, SEL shares lessons in vision, execution, and innovation, plus insights from industry icons and technology leaders shaping the future of PCB fabrication.
Sales: From Pitch to PO
From the first cold call to finally receiving that first purchase order, the July PCB007 Magazine breaks down some critical parts of the sales stack. To up your sales game, read on!
The Hole Truth: Via Integrity in an HDI World
From the drilled hole to registration across multiple sequential lamination cycles, to the quality of your copper plating, via reliability in an HDI world is becoming an ever-greater challenge. This month we look at “The Hole Truth,” from creating the “perfect” via to how you can assure via quality and reliability, the first time, every time.
- Articles
- Columns
- Links
- Media kit
||| MENU - pcb007 Magazine
Estimated reading time: 2 minutes
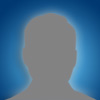
Contact Columnist Form
Material Witness: Thermal Oxidation of Materials, Part II
In a previous column we looked at the some preliminary work that addressed the way polymers are affected when aged in oxidative environments. One of the follow-on activities was to look at the chemistry of materials that had been thermally aged in an oxidizing environment to see whether the observed changes (or not) in electrical properties could be correlated to the development of oxygen-containing chemical groups.Two materials were selected for additional analysis that had targeted applications in the high-frequency microwave/RF area where dissipation factor (loss) is considered important to the design community. In each case FTIR (Fourier Transform Infrared Spectrosopy) was performed on the materials before and after a four week exposure at 120°C (a relatively low temperature), with results as shown below:
As is obvious from the FTIR scans above, the ageing of the olefin-based material resulted in the formation of structures with significant IR absorbance that were not seen in the original scan. These absorbances are in regions associated with hydroxyl (-OH) and carboxylate groups, both of which are polar relative to the original molecules.Similar scans were made on a newly introduced halogen-free product, designed to serve similar markets as the olefin products, with results as shown in the next IR spectrum.
As can be seen, the new halogen-free material did not show any development of potentially polar groups, and the insertion loss testing results (below) confirmed that loss did not change materially.
So what's the "lesson learned" in this work, and what does it tell us about our traditional approach to developing new materials for the multilayer microwave/RF arena? First of all, now that we are aware that this phenomenon can happen (and has happened), as material suppliers we owe it to our customers to look at the effects of oxidative ageing and be able to provide data showing how and to what extent the may be a change in properties under oxidative elevated temperature use conditions. Obviously there are ways to protect materials from oxidation (protective coatings, etc.) and all materials won't be used at elevated temperatures. But the old approach of looking at "state" properties won't be enough for the future. We need to be prepared to study changes over time in terms of critical microwave properties much as UL now looks at changes in physical and electrical properties to determine RTI (relative thermal index) of materials.To be sure, the materials looked at here are not the only materials designed for the multilayer microwave/RF market, and we do know that other suppliers' olefinic materials exhibit similar kinds of ageing and for similar reasons, though some more than others, but it is not the intent of this column to try to do a side-by-side comparison of all the products available or to try to influence users' choices of particular materials.For now, this is the "Material Witness" signing off...until next time.
Chet Guiles is a consultant for Arlon Electronic Materials.
About Arlon Arlon Electronic Materials Division, now part of Rogers Corporation (www.rogerscorp.com), is a major manufacturer of specialty high performance laminate and prepreg materials for use in a wide variety of printed circuit board (PCB) applications and in several distinctive markets. www.arlon-med.com
More Columns from Various Archived Columns
Slash Sheet Chaos: Is What You See, What You Get?Moisture in Materials: Avoiding Process Gremlins
Material Witness: Beat the Heat--A Non-Math Intro to Thermal Properties
Material Witness: Considerations in Using TC Materials for PWBs
Material Witness: Are Your Materials Up to the Challenge?
Material Witness: Thermal Oxidation of Materials, Part I
Material Witness: R.I.P. Speedboard C
Conversations with...Integrated Micro-Electronics Inc.