-
- News
- Books
Featured Books
- pcb007 Magazine
Latest Issues
Current IssueInventing the Future with SEL
Two years after launching its state-of-the-art PCB facility, SEL shares lessons in vision, execution, and innovation, plus insights from industry icons and technology leaders shaping the future of PCB fabrication.
Sales: From Pitch to PO
From the first cold call to finally receiving that first purchase order, the July PCB007 Magazine breaks down some critical parts of the sales stack. To up your sales game, read on!
The Hole Truth: Via Integrity in an HDI World
From the drilled hole to registration across multiple sequential lamination cycles, to the quality of your copper plating, via reliability in an HDI world is becoming an ever-greater challenge. This month we look at “The Hole Truth,” from creating the “perfect” via to how you can assure via quality and reliability, the first time, every time.
- Articles
- Columns
- Links
- Media kit
||| MENU - pcb007 Magazine
Estimated reading time: 3 minutes
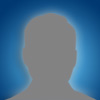
Contact Columnist Form
Material Witness: Thermal Oxidation of Materials, Part I
Material Witness by Chet Guiles
A while back I mentioned that we were doing some work to try to determine the way oxidation affects common PWB polymers. A first look at the data we have been developing has resulted in some "interesting" observations, and while I make no claim to having developed the Universal Theory of PWB Oxidation, what we have found is both interesting and, I think, instructive.
The somewhat busy graph you are looking at is the result of a series of tests in which a variety of PCB materials have been oxidized in air at 150°C and weight gain measured for by TGA for approximately 10 hours.
The materials in this study included:
- Olefin-Based System: A filled polyolefin material widely used in microwave/FR applications, reported Tg >280°C;
- Polyimide A: A filled UL-94 V0 polyimide product, Tg = 260°C;
- Polyimide B: A UL-94 V1 General Purpose polyimide Tg = 260°C;
- FR-4: A flame-retardant multi-functional epoxy system, Tg = 170°C;
- Polyimide C: A "pure polyimide" without flame retardant, Tg = 260°C; and
- New Halogen-Free: A filled, low-loss, halogen-free system for Microwave/RF Application, Tg = 190°C.
The one "dramatic" thing we notice is that the commercial olefinic product gained weight quite severely in the relatively short duration of the test, while the other materials seem to oxidize more slowly. The high-Tg epoxy shows little if any weight gain at all. This last is somewhat surprising because we would have assumed that epoxy would oxidize more rapidly than polyimide, for example. Something is either offsetting the weight gain of oxidation (perhaps some minor thermally induced degradation?) or else the particular formulation we examined is unexpectedly resistant to oxidation. The jury is out on that for now.
Why does the commercial polyolefin (published Tg >280°C, with an observed secondary transition at approximately 100°C) oxidize more rapidly than other materials in the test? The lower temperature transition (typical of olefinic materials) while having minimal effect on intrinsic physical and electrical properties on a highly frilled system, may result in an increase in free molecular volume which could increase the rate of oxygen diffusion into the polymer surface. Since oxygen-containing groups are is often very polar, a substantial degree of oxidation would be expected to result in an increase in dissipation factor (also referred to as "loss tangent") at high frequencies, and indeed such an increase in loss was observed in this material even after only 10 hours at 150°C, from approximately 0.0035 to over 0.005 (at 10 GHz), about A 30% increase.
By comparison, polytetrafluoroethylene (PTFE)-based materials that are historically the "gold standard" for microwave/RF applications at high frequencies, essentially resist oxidation (the fluorine atoms on PTFE are poor "leaving groups" so are not displaced by oxygen under these conditions) and thus PTFE circuit boards with similar loss tangents are very stable in oxidizing environments and show essentially no change in Dk or loss under these relatively benign 150°C thermal oxidizing conditions.
It's just another example of how the data sheets do not necessarily tell the whole story.
Page 1 of 2
More Columns from Various Archived Columns
Slash Sheet Chaos: Is What You See, What You Get?Moisture in Materials: Avoiding Process Gremlins
Material Witness: Beat the Heat--A Non-Math Intro to Thermal Properties
Material Witness: Considerations in Using TC Materials for PWBs
Material Witness: Are Your Materials Up to the Challenge?
Material Witness: Thermal Oxidation of Materials, Part II
Material Witness: R.I.P. Speedboard C
Conversations with...Integrated Micro-Electronics Inc.