-
- News
- Books
Featured Books
- pcb007 Magazine
Latest Issues
Current IssueInventing the Future with SEL
Two years after launching its state-of-the-art PCB facility, SEL shares lessons in vision, execution, and innovation, plus insights from industry icons and technology leaders shaping the future of PCB fabrication.
Sales: From Pitch to PO
From the first cold call to finally receiving that first purchase order, the July PCB007 Magazine breaks down some critical parts of the sales stack. To up your sales game, read on!
The Hole Truth: Via Integrity in an HDI World
From the drilled hole to registration across multiple sequential lamination cycles, to the quality of your copper plating, via reliability in an HDI world is becoming an ever-greater challenge. This month we look at “The Hole Truth,” from creating the “perfect” via to how you can assure via quality and reliability, the first time, every time.
- Articles
- Columns
- Links
- Media kit
||| MENU - pcb007 Magazine
Estimated reading time: 11 minutes
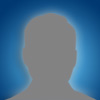
Contact Columnist Form
Proof of Design - Supplier Evaluation And Qualification Here and Off Shore - Part II
Proof of Design
The last column (9) drew lots of attention. More than 300 people, and counting, read it and emailed very similar thoughts on the subject. This column installment, therefore, is a follow up. It will be short and sweet - to some.
The following two emails tell about the same story as do most others:
Hello Earl,
We are a backplane & enclosure design house and manufacturer located in Waterloo, Ontario, Canada.
Over the past years we were pretty much swept by the same tidal change in the industry regarding bare PCB suppliers. Long story short, we had the same issues qualifying the offshore/Asian suppliers that you have mentioned in your lengthy and very informative article on pcb007.com. We switched from a handful of well-known North American PCB manufacturers (which we had known for years) to a "pool" of Asian suppliers handled through a North-American based rep. Now, I was surprised to find out that some Asian manufacturers actually knew about IPC-1710A, albeit when they sent us back the questionnaires they were all full of old data (and we did manage to get them to send updated information, eventually).
I would like to have a copy of your list of bad and good Asian suppliers which you are familiar with. It would help with our PCB outsourcing efforts, both now and in the future. What we are seeing as a trend is the Asian prices going up while some NA prices are going down, even for fast prototypes.
I cannot comment on the quality issues since we did not observe a lot of failures so far, but it would be good to have a list of "bugs" that you encountered with the Asian manufacturers, in order to know what to look for.
Finally I would like a chance to look over your documentation on the POD ftp download site; please email me a login and password.
Thank you
Ovidiu Mesesan
Senior Design Engineer
Kaparel Corporation, A Rittal Company
Earl,
Read your article on the qualification.
I have the same frustrations. I have been on the road for 6 months; 5 countries looking at PCB shops and auditing them to IPC standards. My company is in contract manufacturing for highly regulated industries, and our customers range from aerospace (Honeywell) to gaming (Bally's) -- all of which require quality over price.
Ironic though, the same customers pound on us for cost reductions weekly and force upon us inferior PCB suppliers to choose from. So we took the show on the road. Every DWG we have requires the PCBs be built to IPC-600, 6012 or 2221 (which all refer back to 6012 for process controls). Almost every shop said they were IPC compliant.
Not a single one was. We visited 15 shops in 5 countries, some didn't even own the spec, some were doing micro-sections fairly often, others were doing it every 4 hours (NOT EVEN BY LOT).
Just thought I would drop you a note to let you know that I feel your pain--never checked out any of "your" shops, but we are now working with a few to develop them into "real" IPC compliance. Even funnier, one of the shops sent a letter to its top 10 customers letting them know they were doing this for us, asking their other customers if they wanted full IPC controls implemeted on their product. NOT A SINGLE ONE WANTED IT if it meant increasing the price (which, obviously, it would).
I took the PCB commodity manager position over a year ago, had 40+ suppliers and now am down to 25 goal of hitting 15 in various regions for various technologies. I am starting to think this whole industry is bracing for failures all over the place. Luckily, I know we build good parts for the airplanes I fly in...not sure about the rest of these guys though......
Paul Pluta, CPIM, C.P.M.
Sparton Electronics
Corporate Commodity Manager
----
It's kind of interesting as so many folks are on the same page struggling to evaluate and qualify suppliers. It also is interesting that most impose, or attempt to impose, IPC guidelines and specifications with little initial realization, by the candidate suppliers, what they are, what they mean, what they require, or how to approach them when asked. I'm sure IPC Asia eventually will take care of the situation. However, it is left to us to get the ball rolling.
To add a little fuel to the fire, or stir the pot as I prefer to call it, the following is going on in this country at this time on the IPC DesignerCouncil:
FROM THE DESIGNER COUNCIL
Hi Designers.
I don't normally do this but I have a need to hook up with a few more board vendors that do 2-sided and multilayer FR4 type commercial boards consistently well and for a lower price for short production runs...Like 100 pieces here and 300 pieces there, etc... with a few weeks' turn typical ('gravy' work for most shops). We have a lot of this sort of work and need to develop relationships with a few more good shops.
I would like to get recommendations from DESIGNERS, please. I don't need a bunch of sales people from board shops cold calling me... I want tried and true shops that designers know do a good job for them and get good prices...and I don't want to send our business overseas. We want our boards made here in the good old USA, close to home. Our products are used by the military and we don't need to comply with RoHS. We can use regular SN63 solder.
Thanks in advance for your help and Merry Christmas!
Bill Brooks - KG6VVP
PCB Design Engineer, C.I.D.+, C.I.I.
If someone is compiling a list (Andy?), when this thread dies down a bit, would you mind publishing the list to this discussion group?
Regards-
Michael Howell
...and Prototron is a supporter of the IPC Designer's Council PNW Chapter
George Patrick
Tektronix, Inc.
Central Engineering, Engineering Design Services
or go to:
http://www.pcbyellowpages.com :)
Merry Christmas all,
Mitch
----
DISTURBED BUT NOT TOO SURPRISED - AFTER ALL THESE YEARS
The forum posting from Bill Brooks, above, is particularly disturbing to me as, apparently, he has the authority to choose suppliers - based on what other criteria than seeking advice from other designers, I don't have a clue. It's as if designers and fabricators grew up on two different sides of a railroad track but neither crossed over to visit. This is especially true of designers, it appears, and Bill doesn't even want to talk to a supplier across a 4.5' wide track.
This gentleman only wants to hear from other designers. He doesn't want to talk with board shops either for fear of a sales pitch or possibly learning something. It's just a trust your good ol' boy buddy mentality and hope for the best. This is not uncommon. Also, he is looking to expand his supplier base when most smart, knowledgeable folks are reducing theirs as in the example again sited below and in the beginning of this column.
Again, Paul Pluta says, "I took the PCB commodity manager position about a year ago, had 40+ suppliers and now am down to 25 goal of hitting 15 in various regions for various technologies. I am starting to think this whole industry is bracing for failures all over the place."
Of course Mitch, above, throws in a little humor that could be an example of the "shotgun" mentality still alive and well - more often than not. He says check out the yellow pages. Sure Mitch, but we love the humor, eh?
Getting back to reality, most folks agree, as do I, that any supplier first must show proof of effective process management and capabilities. It is not good enough for them to say their processes are in control because all that means is product quality will be consistent as inconsistently good or bad. Then, a supplier must prove quality is acceptable in accordance with contract requirements and the main instrument for board suppliers is the master drawing. These requirements must be met.
First, they must be met by suppliers clearly indicating they manage processes and all elements being introduced to them. Then they must show clear evidence of quality effected by them.
Show me how you manage processes:
Show me the effects of how well you managed processes:
Well, wasn't that easy? I can tell you it is, but I cannot always say why I make a good bit of my living consulting with folks who just don't get it, often don't seem to care, or are just too damn lazy to do anything but call their "friends" for recommendations. Bill and many others still don't get it, and probably never will, but I'll be watching, reporting, and definitely not flying, riding, or otherwise using anything in which their boards reside - just waiting to bite my ass.
Note: Bill Brooks and everyone mentioned in this column installment have previewed it before publication. Most approved of it, though it makes little difference to me but for the smart folks mentioned herein. Damn, doubt I'll be doing any consulting with Bill, who so badly needs it.
A DESIGNER'S REPLY TO MY "ASSUMPTIONS" BEFORE ARTICLE PUBLICATION
As I've said many times, a good engineer never assumes anything. This was the case when considering what I took first at face value as stated above by Bill Brooks. Most folks would agree, based upon his request about locating new PCB suppliers. I mean it clearly says what it says but I knew there had to be something more to the story or we're all in deeper stuff than anyone could imagine. Because of this, I emailed Bill with my article and asked for his response. It is as follows:
Earl,
I think I see how you are attempting to use me and my search for leads to good PCB suppliers from my fellow designers council members as an example of 'what NOT to do' when evaluating suppliers. You have made it plainly obvious that you think that designers know very little or nothing when it comes to making boards, (thus discounting any advice I might get from them) but you missed the point of why I sent that inquiry and what I was hoping to accomplish by doing it. A collection of recommendations from other designers is not the sole method of selection used by me or my company nor is the recommendation of another designer the sole criteria for approval to purchase from a board supplier. We DO have a process, and we DO review our suppliers on a regular basis. I was only hoping to reduce the number of choices to a smaller collection that my peers had already had a good experience with, that does not mean we would automatically use them upon my receipt of the list.
Board shop evaluation is a multi-step process and involves more people than just the designer. The initial lead may be found by the buyer, the designer, or just someone in the company looking for a board shop on the internet for that matter... the 'weeding out' process is expensive and time consuming and our QA people are choosy about who we partner with. So as you say, 'the good old boy network' as you sarcastically refer to using the members of the DC list server, can work to the advantage of a company in collecting leads to good board houses, but the process of selection does not stop with the designer or the buyer which you seem to assume is what was going on. The list I collected and sent to the buyer is just the beginning of a lengthy qualification process. The Quality Assurance department spends the time and effort to QUALIFY the shops we recommend before we do business with them. The designer seldom needs to get involved in the process except if there is a design related issue that needs review. But I am flattered that you thought my search for an additional supplier was such a 'prime' example of 'doing it wrong'. Have fun with your column...
Bill Brooks
----
My reply was short and most appreciated even though he laid that word assume upon me. If I had assumed anything, I would not have contacted him to set the record straight.
Thanks for the clarification Bill,
I will change my column to reflect this.
Enjoy, Earl
----
The key thing here is knowing a complete evaluation and qualification system and team in place at this company and thank goodness for that. Often, this is not true as evidenced by what I said earlier in this column and so much more in earlier column installments.
Concurrence, involving a complete team, is required in the qualification process. Designers designing, buyers buying (only from qualified suppliers), engineers engineering things suppliers can make, and quality folks reporting supplier quality performance information to keep everyone on the same page. Still, to start, the yellow pages probably is as good a place to start as any - initially UNLESS YOU KNOW SOMETHING ABOUT BOARDS because opinions can be as bad as assumptions. Everyone has opinions but, if they are based on assumptions, that's a real problem. You have to do your work yourself and the following is a little message I was reminded about from my good friend, and fine quality engineer at Pitney Bowes, Randy Bock:
Don't wait for the light at the end of the tunnel, walk on down there yourself and turn the damn thing on!
SUMMARY
Don't take anything for granted. Don't assume anything. Don't just trust your "friends" especially when you seldom know what they do with whom and you never know where their fingers have been. Etc., etc..
Visit POD's new feature as PODWORLDINPICS1-4 and post your story in YOURWORLDINPICS. Individuals may post free. Companies pay just a little.
Stay tuned for my next column about stencil printing improvement.
MoonMan always says just do it, but do it right by using DFM/CE.
Earl Moon (Proof Of Design)
More Columns from Various Archived Columns
Slash Sheet Chaos: Is What You See, What You Get?Moisture in Materials: Avoiding Process Gremlins
Material Witness: Beat the Heat--A Non-Math Intro to Thermal Properties
Material Witness: Considerations in Using TC Materials for PWBs
Material Witness: Are Your Materials Up to the Challenge?
Material Witness: Thermal Oxidation of Materials, Part I
Material Witness: Thermal Oxidation of Materials, Part II
Material Witness: R.I.P. Speedboard C