-
- News
- Books
Featured Books
- pcb007 Magazine
Latest Issues
Current IssueInventing the Future with SEL
Two years after launching its state-of-the-art PCB facility, SEL shares lessons in vision, execution, and innovation, plus insights from industry icons and technology leaders shaping the future of PCB fabrication.
Sales: From Pitch to PO
From the first cold call to finally receiving that first purchase order, the July PCB007 Magazine breaks down some critical parts of the sales stack. To up your sales game, read on!
The Hole Truth: Via Integrity in an HDI World
From the drilled hole to registration across multiple sequential lamination cycles, to the quality of your copper plating, via reliability in an HDI world is becoming an ever-greater challenge. This month we look at “The Hole Truth,” from creating the “perfect” via to how you can assure via quality and reliability, the first time, every time.
- Articles
- Columns
- Links
- Media kit
||| MENU - pcb007 Magazine
Estimated reading time: 7 minutes
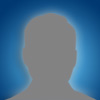
Contact Columnist Form
Jack Olson: Preparing for Component Placement
Editor's Note: This article previously appeared in the August issue of SMT Magazine. Jack Olson has been putting together an introductory tutorial for novice circuit board designers at http://HowToPCB.net.
Jack's entire site is not yet complete, but we can't resist giving our readers a sneak preview. His latest chapter outlines one approach to component placement.
This week we'll focus on preparing for component placement.
At this point you have already:
- Packaged the schematic, which mapped all of the symbols into corresponding components and assigned unique reference designators to them; and
- Entered some kind of board outline or boundary which defines the area we can use for component placement.
Depending on the CAD system, your layout environment may look like a jumble of components with a rat's nest of net lines connecting them all together, or it may be completely empty, waiting for you to select parts one at a time (or in groups) for placement.
It would be very difficult to mentally keep track of everything we need to remember for a complex design, so we depend on the computer to maintain connectivity and help us keep track of any built-in rules. Even with computers helping us, looking at perhaps hundreds or thousands of parts that need to be placed intelligently can be very intimidating.
How Do We Start?We can develop a "plan of attack" by logically breaking down the final goal into smaller steps. Some of the steps can be accomplished immediately and you probably won't have to worry about them again (like placing mounting holes). Others must be maintained throughout the design process (like component height restrictions). These should either be incorporated into the CAD system by creating design constraints or rules, or added to a manual checklist for the review process to make sure the design meets all expectations.
Use the capabilities of your CAD system!
Mechanical Constraints
Component placement will be confined to a limited area, which may have to be reduced even more by mounting considerations. Before you start placing parts, make sure any mounting holes have been placed at the proper locations and that you know how much clearance area is needed around them. If your CAD system supports it, lock these down in a way that prevents you from accidentally moving them.
Depending on the final assembly, there may also be clearances needed for tooling, card ejectors, brackets, etc., as well as component keep-out areas and areas with component height restrictions. Some CAD systems provide a way to define these "keepout" areas so the computer can report violations during automatic checking; others prevent violations from occurring at all.
Next, some components may have pre-defined locations. Depending on the next-level assembly, connectors might have to be placed with a specific orientation to mate with other parts of the system. Switches, displays, indicators, LEDs, variable components and some types of test points may need to be placed for accessibility.
All components with pre-defined locations should be placed first.
Assembly Considerations
It will help to know how your board will be assembled and tested. Will the bare boards be processed individually or in arrays? If individually, will the boards need extra rails for support? If palletized in arrays, how will they be separated? Will you need clearance for v-scoring? Routing? Tab-cutting? Can your design have parts on both sides? If there are through-hole parts, will they be wave soldered, selective soldered or hand soldered? Will an in-circuit test (ICT) fixture be developed?
Don't panic; these questions are not designed to make your job more difficult. You may not know all of the answers, but component placement can influence assembly processes later on, and knowing something about them may help you design a better product. If your design will be built using an automated assembly line, you may need to add fiducials and extra tooling holes, which will use up more of the board area. Get these placed before you run out of room.
If the assembly will be transported from place to place using conveyors, you will need to keep components away from the edges. If your design is small and will be assembled in a pallet array, the pallet itself will provide rails that are discarded later. In this scenario you may be able to use the full area of the board for placement, leaving only enough clearance for singulation tools - tools that break the boards apart at the end of the process. Otherwise, you will not be able to place components too close to the board edge.
If the boards will be assembled individually, keep components 3 mm away from the board edge.
You will decide which of several placement schemes will work best for your design, which will define a specific assembly type. The type that you choose will determine the basic steps required to assemble the product.
If you can fit all of the parts on one side of the board you probably should. One-sided assemblies are designated as TYPE 1:
TYPE 1A - All Through-Hole Parts
The easiest type to assemble and solder manually, automatic component insertion is more difficult than TYPE 1B, but can be wave soldered with a single pass.
TYPE 1B - All Surface Mount parts
Assembled using a single paste screen and a single pass through component insertion and reflow soldering. IDEAL.
TYPE 1C - Mixed Assembly SMT and Through-HoleTwo soldering passes required.
If you have to place components on both sides of the board, it automatically becomes a TYPE 2 assembly and will require a greater number of assembly processes.
TYPE 2A - Through-Hole Parts on Both SidesRequires manual processes. NOT RECOMMENDED.
TYPE 2B - Surface Mount Devices on Both Sides (Try to keep active devices on same side.)
TYPE 2C - Complex Intermixed Assembly on Both Sides
You should have an idea of the assembly type that is most appropriate for your design before you start placing components. Limited placement area (circuit density) may drive you towards using both sides of the board, and the component types required may drive extra assembly processes that can influence placement.
Before proceeding, determine if your design will be a one-sided or two-sided assembly.
If through-hole components are inserted from the top, they will usually be soldered from the bottom using wave soldering or selective soldering.
Wave SolderingThis method moves the bottom of the board over a molten wave of solder, and when the wave touches any exposed metal it will be coated. Where two exposed metal surfaces are touching each other (like a lead in a hole or an SMT termination sits on a land), a solder joint will be formed between them. Surface mount devices are often attached to the bottom of the board with adhesive and then wave soldered.
Figure 1. Preferred orientation of parts vs. defect-prone orientation.
What does this have to do with component placement? If the design is to be wave soldered, parts should be aligned or oriented to the direction of the wave to prevent solder shorts or open connections. For example, if you put a very small component behind a very tall component, as the wave passes over the tall component it could create a "shadowing effect" which may result in the smaller component having insufficient solder or none at all. Figure 1 shows how surface mount parts should be rotated with respect to the wave direction.
Selective SolderingIf there are only a few through-hole connections that need to be soldered, assemblers may choose to do selective soldering for just those through-hole leads, and reflow solder the rest. If selective soldering will be used, maintain a 6 mm diameter keepout area around each through-hole. See Figure 2.
Figure 2. Proper clearances required for selective soldering.
If passives must be placed closer to the through-hole pin, the selective soldering nozzle can be offset, but make sure there is enough room on the other side for the full 6 mm clearance diameter, and make sure there is at least 1.5 mm from pad to pad. Also, if the selective solder nozzle heats both ends of a passive SMT device at the same time and they both reflow, the component may fall off the board. Try to place passives "inline," with one end close and the other farther away.
Testability
One more consideration before we get started placing parts: If an ICT fixture will be required, you will have to add extra vias for test point accessibility to every net. Since the goal is 100% accessibility to every net from the bottom of the board (double-sided fixtures are more expensive), even short traces that can be routed on the top of the board have to use a via to get to the bottom-side for a test point. Adding vias to every net means extra space between components, so keep this in mind (or just add them) while you are placing functional groups of components.
That was a lot of preparation, but now we're ready. Next time, we start placing components.
Jack Olson is currently designing circuit boards for Caterpillar. He can be reached at pcbjack@gmail.com.
More Columns from Various Archived Columns
Slash Sheet Chaos: Is What You See, What You Get?Moisture in Materials: Avoiding Process Gremlins
Material Witness: Beat the Heat--A Non-Math Intro to Thermal Properties
Material Witness: Considerations in Using TC Materials for PWBs
Material Witness: Are Your Materials Up to the Challenge?
Material Witness: Thermal Oxidation of Materials, Part I
Material Witness: Thermal Oxidation of Materials, Part II
Material Witness: R.I.P. Speedboard C