-
- News
- Books
Featured Books
- design007 Magazine
Latest Issues
Current IssueShowing Some Constraint
A strong design constraint strategy carefully balances a wide range of electrical and manufacturing trade-offs. This month, we explore the key requirements, common challenges, and best practices behind building an effective constraint strategy.
All About That Route
Most designers favor manual routing, but today's interactive autorouters may be changing designers' minds by allowing users more direct control. In this issue, our expert contributors discuss a variety of manual and autorouting strategies.
Creating the Ideal Data Package
Why is it so difficult to create the ideal data package? Many of these simple errors can be alleviated by paying attention to detail—and knowing what issues to look out for. So, this month, our experts weigh in on the best practices for creating the ideal design data package for your design.
- Articles
- Columns
- Links
- Media kit
||| MENU - design007 Magazine
Estimated reading time: 5 minutes
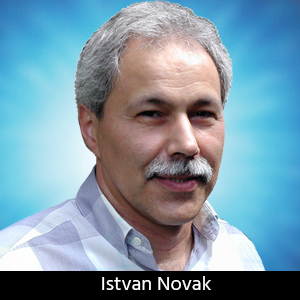
Quiet Power: Inductance of Bypass Capacitors, Part II
We finished the last column, Inductance of Bypass Capacitors, Part I, with a few questions about the inductance of bypass capacitors: Why is nominally the same capacitor sometimes reported with different inductance values by different vendors?
Figure 1 will help us to understand the reasons. The sketch shows the side cross-section view of a mounted bypass capacitor. We see here a multilayer ceramic capacitor (MLCC), but the following arguments are the same for aluminum electrolytic or tantalum capacitors as well. The capacitor is shown mounted to surface pads on the PCB. For the sake of simplicity, only those two layers are shown in the board, where the capacitor connects.
Figure 1: On the left, a side cross-section view of a mounted bypass capacitor. On the right, contributors to the loop inductance. The red line represents the current loop.
We can identify inductance along a loop of current, composed of conductive or displacement currents through conductors or insulators. When we use the capacitor in a bypass application like the one shown in Figure 1, the current goes through the terminals and plates of the capacitor (this is conductive current), through the dielectric insulation of the capacitor (this is displacement current), continues in the solder pads, escape traces, vias, planes/puddles (this is conducive current) and finally displacement current closes through the dielectric material between the power and ground plane shapes.
There is a simple but very important observation we can make at this point: a big part of the loop, the size of which eventually determines the inductance of the mounted bypass capacitor, is determined by the user geometry, and only a smaller part of the loop is determined by the capacitor itself. This is true for the actual usage of the capacitor, but also true when we measure or simulate the inductance of the capacitor. This large dependence on the user geometry is the main reason for having various inductance definitions associated with bypass capacitors.
Does this mean we cannot determine the true inductance of a bypass capacitor? Well, there is one inductance definition, which depends only on the capacitor geometry itself and not on the user geometry. It is called the partial self-inductance. Unfortunately, as we will now see, knowing the partial self-inductance of a capacitor helps very little in bypass applications.
Figure 2: Current loop with partial self-inductances and mutual inductances.
Figure 2 shows a closed rectangular current loop, which is a simplified geometry of the current loop in Figure 1, shown by the red line. The arrows show the direction of current as it goes around the closed loop. The top horizontal leg represents the capacitor. In this rectangular current loop the two horizontal and the two vertical current paths are coupled through mutual inductance. Since the parallel legs of the path carry opposite-sign current, the mutual inductance subtracts from the partial self inductance. The perpendicular current filaments do not couple and therefore there is no mutual inductance shown between the horizontal and vertical legs.
The loop inductance is shown on the right of Figure 2. Note also that tighter coupling (smaller loop height and/or width) reduces the loop inductance. For weak coupling the actual loop inductance will be higher than the partial self-inductance of the capacitor itself. However, for strong coupling, the loop inductance can be even less than the capacitor's partial self-inductance. This is why knowing the partial self-inductance of the capacitor, though it does not depend on the user geometry, does not really help us in determining the inductance of the mounted capacitor.
Figure 3: Fixture geometry for capacitor measurements. On the left, a short compensation/calibration with shorting bar. On the right, a device under test mounted on the fixture.
Figure 3 shows the simplified geometry when we measure capacitors. The fixture has terminals where the capacitor is connected. During the fixture compensation or calibration process we first measure--among others--a reference short. This reference shorting bar establishes the value that the instrument will consider as zero impedance. If we know the actual resistance and inductance of the shorting bar, some instruments will take these values and adjust the baseline reading accordingly. After calibration, the device under test is connected and measured. The measured inductance value of the capacitor will be shown with respect to the inductance of the shorting bar. Since we usually do not know the internal geometry details of the fixture, we can already see several reasons why and how the same part measured by different vendors (possibly with different fixture geometries) could end up having different inductances: it could be that the shorting bar geometry is different, or perhaps the internal geometry of the fixture is different, or the way how the measurement represents the shorting bar either neglecting or taking into account its inductance.
So if you see different inductance numbers for the same nominal part, first ask the vendors how they obtained those inductance values; the different simulation or measurement conditions are usually the reason. If you cannot ask the vendors, look at the parts and see if anything in the geometry visible from the outside may explain the difference: taller (thicker) capacitor body increases the size of the current loop and the inductance. If nothing appears to be different from the outside, make cross sections of the parts and look at the internal geometry: thicker encapsulation or cover layer also increases inductance. If all dimensions appear to be the same or very similar, the inductance values should also be very close--as long as we have the same user geometry for the mounting. This is true for characterization measurements, simulations and user applications alike.
The reference listed below walks you through various considerations about the inductance of bypass capacitors, and it also lists several possible ways how we can specify the inductance of a bypass capacitor.
References
"On the Uniqueness of the Inductance of Bypass Capacitors" in TecForum TF-MP2 "Inductance of Bypass Capacitors: How to Define, How to Measure, How to Simulate," DesignCon 2005 East, High-Performance System Design Conference, Worcester, Massachusetts, September 19-22, 2005, available online at www.electrical-integrity.com/.
Istvan Novak is a distinguished engineer at Oracle, working on signal and power integrity designs of mid-range servers and new technology developments. He can be reached at istvan.novak@att.net.Follow I-Connect007 on Twitter here.
More Columns from Quiet Power
Quiet Power: An Evolution in PCB Design CostsQuiet Power: The Effect on SI and PI Board Performance
Quiet Power: 3D Effects in Power Distribution Networks
Quiet Power: Noise Mitigation in Power Planes
Quiet Power: Uncompensated DC Drop in Power Distribution Networks
Quiet Power: Ask the Experts—PDN Filters
Quiet Power: Friends and Enemies in Power Distribution
Quiet Power: Be Aware of Default Values in Circuit Simulators