-
- News
- Books
Featured Books
- pcb007 Magazine
Latest Issues
Current IssueInventing the Future with SEL
Two years after launching its state-of-the-art PCB facility, SEL shares lessons in vision, execution, and innovation, plus insights from industry icons and technology leaders shaping the future of PCB fabrication.
Sales: From Pitch to PO
From the first cold call to finally receiving that first purchase order, the July PCB007 Magazine breaks down some critical parts of the sales stack. To up your sales game, read on!
The Hole Truth: Via Integrity in an HDI World
From the drilled hole to registration across multiple sequential lamination cycles, to the quality of your copper plating, via reliability in an HDI world is becoming an ever-greater challenge. This month we look at “The Hole Truth,” from creating the “perfect” via to how you can assure via quality and reliability, the first time, every time.
- Articles
- Columns
- Links
- Media kit
||| MENU - pcb007 Magazine
Estimated reading time: 4 minutes
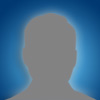
Contact Columnist Form
Material Witness: Rheology, Part I
Material Witness, by Chet Guiles
The Greek meta-physician Heraclitus, writing in the fifth century BC said, "Panta Rei" or "Everything Flows." I'd like to spend a little time visiting the science of rheology (how and why things flow) and, in particular, how understanding the rheology of the prepregs you use, during the time they melt and flow, can help you, as a process engineer, manage and control your lamination process.Anyone who has ever scratched his or her head studying the flash or edge trim of a laminate cycle that has not gone as expected knows empirically about some of the effects of flow, or not flow, on a laminated MLB. Too much flow means boards that are "footballed;" too little flow means boards with dry edges and maybe inadequate fill around circuit traces or in low pressure areas. Application of the science of rheology, and an understanding of how and why your materials behave the way they do, can reduce the dependency on prayer, magic and guesswork in designing press cycles.But let's start at the beginning. What is "rheology" and why does "everything flow?" We are interested in viscosity (the resistance of a material to flow) and in flow itself: How much, how quickly and what factors affect it. Viscosity, in very simple and non-mathematical terms, is a measurement of the resistance of a fluid to flow when a force is applied to it. All other things being roughly equal, the amount of flow is proportional to the amount of pressure per unit area (P/A) multiplied by a constant (determined by the geometry of the system) and integrated over time as a function of viscosity.A "resin flow parameter" [1]has been defined by the following formula:F = c*(P/A) ∫ (1/v) dtWhere:
- F is the resin flow parameter;
- c is a constant based on system geometry;
- P/A is the pressure divided by the area of the board;
- v is the viscosity; and
- t is time (viscosity changes with time as the resin starts to cure).
You can see that the ratio of the pressure to the area is critical. As an example of what that might mean to you as a PWB processor, consider the old standard IPC test for flow, where a stack of 4" x 4" samples is pressed at 200 psi and the flow measured. The P/A ratio is 200/16 or 12.5. How does that relate to your laminating an 18" x 24" panel at 350 psi? Not very well. The P/A ratio there is 0.81! The scaled flow test (IPC TM-650, 2.4.38A) which uses 31 psi on a 5.5" x 7" sample area is a closer approximation of the kind of flow expected in a normal lamination process. The P/A ratio there is 31/38.5 or 0.81!An unexpected benefit of this information is that given a known resin system, it is possible to adjust laminating pressure depending on the area of the board being fabricated to keep the P/A ratio constant. It goes like this:P = k * SQRT(A)Where:
- P = pressure in psi;
- k is a constant based on the resin system (usually determined empirically); and
- A = the area in square inches of the laminated panel.
Let's say you are using a particular polyimide prepreg and you laminate a 12" x 18" panel at 275 psi with good results. So working the math:275 = k * SQRT(12 * 18) and so k = 275/14.7 and k = 18.7If you want to laminate an 18" x 24" panel, you can guesstimate the proper pressure as 13.2 * SQRT(18 x 24) or 18.7 * 20.8 = 390 psi.In my next column, we'll talk about the effect of your process on the actual viscosity of the prepregs you use, and how to make simple adjustments of process based on two easy to adjust parameters: Pressure and heat-up rate.Thanks to Paul Kyle, formerly of Arlon, for much of the theoretical and "spade work" on rheology that helped in our development of practical rheological tools. He has moved on, but his work on rheology brought us--and me in particular--out of the "stone age" of simple P/A calculations, to a place where we can use some sophisticated rheological tools to evaluate and characterize newer resins.
Reference: 1. Bartlett, Bloechele and Mazieka, "The Use of Scaled Flow Testing for B-Stage Prepreg," IPC Technical Paper TP-281, IPC Annual Meeting, April, 1979.
Chet Guiles is a graduate of the University of New Haven with a BA in Chemistry (1971) and of the Syracuse University Eastern European languages Institute in Russian Language (1963, while on active duty with the USAF). Subsequent to his military service, Chet worked in the areas of corrosion metallurgy (Olin Metals Research), and PVC and silicone rubber technology (Automation Industries). Prior to joining Arlon in 1979, Chet worked as a Senior Research Chemist at Pennwalt Corporation performing research on PVC stabilization.At Arlon, Chet has served in a number of roles including Technical Manager for the Silicone Rubber Group in DE, Quality Assurance Manager for the Delaware Microwave Materials operation, Division Technical Director and, most recently, as Director of New Business Development for the Electronic Substrates Division. Retired in 2004, Chet now acts as a part-time consultant to Arlon.Chet has several U.S. patents and has written and published widely over the past 30 years in the area of materials for PCBs. His classic "Everything You Ever Wanted to Know About Laminates, But Were Afraid to Ask" was recently released in a 9th Edition in November 2008, available on-line in pdf format at www.arlon-med.com.
More Columns from Various Archived Columns
Slash Sheet Chaos: Is What You See, What You Get?Moisture in Materials: Avoiding Process Gremlins
Material Witness: Beat the Heat--A Non-Math Intro to Thermal Properties
Material Witness: Considerations in Using TC Materials for PWBs
Material Witness: Are Your Materials Up to the Challenge?
Material Witness: Thermal Oxidation of Materials, Part I
Material Witness: Thermal Oxidation of Materials, Part II
Material Witness: R.I.P. Speedboard C