-
- News
- Books
Featured Books
- pcb007 Magazine
Latest Issues
Current IssueInventing the Future with SEL
Two years after launching its state-of-the-art PCB facility, SEL shares lessons in vision, execution, and innovation, plus insights from industry icons and technology leaders shaping the future of PCB fabrication.
Sales: From Pitch to PO
From the first cold call to finally receiving that first purchase order, the July PCB007 Magazine breaks down some critical parts of the sales stack. To up your sales game, read on!
The Hole Truth: Via Integrity in an HDI World
From the drilled hole to registration across multiple sequential lamination cycles, to the quality of your copper plating, via reliability in an HDI world is becoming an ever-greater challenge. This month we look at “The Hole Truth,” from creating the “perfect” via to how you can assure via quality and reliability, the first time, every time.
- Articles
- Columns
- Links
- Media kit
||| MENU - pcb007 Magazine
Estimated reading time: 4 minutes
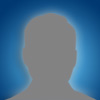
Contact Columnist Form
Material Witness: Rheology, Part II
Material Witness by Chet Guiles
"Panta Rei" - "Everything Flows" -- Part 2
I would be tempted to say "It's all Greek to me," but that might suggest a warped sense of humor. Last time we talked about a practical application of the theoretical formula for resin flow to establishing lamination pressure for various-sized panels of the same prepreg. But suppose you have a variety of different board designs and the prepreg just doesn't flow the way you want it to from one design to the next. We can still apply some of the science of rheology to help you adjust your process with a minimum of muss, fuss and confusion, to take into account the fundamental rheological properties of the resin itself.
Revisiting the mathematics or prepreg flow, remember we defined a resin flow parameter in terms of work done by Bartlett, Bloechele and Mazieka as:
F = c*(P/A) ∫ (1/v) dt
Where: F is the resin flow parameter
c is a constant based on system geometry
P/A is the pressure divided by the area of the board
v is the viscosity
t is time (viscosity changes with time as the resin starts to cure)
Knowing how the resin flow changes as a function of the process with which you are working can allow you to make subtle process changes that will tweak in a cycle for a variety of board configurations. I remember "way back when" when Bill Reimann of Hughes, El Segundo, was trying to fill opposed 6 ounce copper signal layers with polyimide prepreg, and it seemed that no matter how much prepreg he stuffed in the opening, there just wasn't enough flow to fill that Grand Canyon depth circuit profile. We finally fixed the problem empirically with three variables: more pressure (obvious enough), faster application of pressure (not so obvious) and faster ramp-rate on the temperature in the cycle. All of these are factors that are affected by the viscosity of the resin as it melts and flows.More pressure is obvious. If the "P" in the "P/A" part of the equation goes up, so does the total amount of flow. But how do the other variables, rate of application of pressure and the change in heat up rate relate to our theoretical study of rheological principles. Many resins are semi-thixotropic, and as a result they flow more quickly during a time when there is an increasing rate of application of pressure. So a quick application of pressure results in a greater "squooshing" out of resin while the pressure is changing from low to high. Change the rate at which pressure is applied, and you change the overall amount of flow.
It is reasonably well known that most resin systems' viscosities are affected by the heat-up rate in a predictable way. The attached chart represents the effect of the rate of heat up on the viscosity of Arlon's 35N polyimide. Note that the fastest heat-up rate results in the lowest melt viscosity and pushes out the temperature at which minimum viscosity is reached. While the chart here is for a specific polyimide product, most conventional epoxy and polyimide materials behave similarly - only the absolute values of melt viscosity change. Whereas the "low" viscosity for 35N polyimide at 70C/min is between 600 and 1000 poise, the equivalent viscosity for a low flow product would be 6000 to 10,000, a full order of magnitude higher.How does this data help you as a MLB producer optimize your process? Self-evidently, when you heat up your resin faster, you can achieve a lower melt viscosity and thereby a greater total amount of flow. If you have too much flow, a significant improvement can be made by slowing down the heat up rate (which can be achieved by adding paper padding or other thermal insulating material). I remember a customer years back using a high Tg epoxy and winding up with excessive flow and footballed boards. The flow bead was smooth and clear with no foaminess indicating water or some other volatile component as the source of the excess flow. By adding a single ply of kraft paper padding to each side of the book, the heat rate was slowed enough (in this case from about 70C/min to just about 50C/min) to cut back the flow, flatten the panels and still fill circuitry and bond without a problem.
With low-flow products used in rigid-flex products the benefit of being able to tweak your process with heat up rate and pressure without having to have a series of prepregs of varying flow values simplifies your inventory and allows you to be flexible (no pun intended) in your manufacturing process without any "give-ups."
I want to talk more about low-flow and no-flow materials in a future column (If we believe Heraclitus -- "Panta Rei" -- can there really be such thing as a "No-Flow" product?) but for now I'll leave you to chew on the sticky subject of rheology and how you can use rheological principles to help tune your processes.
Chet Guiles is a graduate of the University of New Haven with a BA in Chemistry (1971) and of the Syracuse University Eastern European languages Institute in Russian Language (1963, while on active duty with the USAF). Subsequent to his military service, Chet worked in the areas of corrosion metallurgy (Olin Metals Research), and PVC and silicone rubber technology (Automation Industries). Prior to joining Arlon in 1979, Chet worked as a Senior Research Chemist at Pennwalt Corporation performing research on PVC stabilization.At Arlon, Chet has served in a number of roles including Technical Manager for the Silicone Rubber Group in DE, Quality Assurance Manager for the Delaware Microwave Materials operation, Division Technical Director and, most recently, as Director of New Business Development for the Electronic Substrates Division. Retired in 2004, Chet now acts as a part-time consultant to Arlon.Chet has several U.S. patents and has written and published widely over the past 30 years in the area of materials for PCBs.
More Columns from Various Archived Columns
Slash Sheet Chaos: Is What You See, What You Get?Moisture in Materials: Avoiding Process Gremlins
Material Witness: Beat the Heat--A Non-Math Intro to Thermal Properties
Material Witness: Considerations in Using TC Materials for PWBs
Material Witness: Are Your Materials Up to the Challenge?
Material Witness: Thermal Oxidation of Materials, Part I
Material Witness: Thermal Oxidation of Materials, Part II
Material Witness: R.I.P. Speedboard C