-
- News
- Books
Featured Books
- pcb007 Magazine
Latest Issues
Current IssueInventing the Future with SEL
Two years after launching its state-of-the-art PCB facility, SEL shares lessons in vision, execution, and innovation, plus insights from industry icons and technology leaders shaping the future of PCB fabrication.
Sales: From Pitch to PO
From the first cold call to finally receiving that first purchase order, the July PCB007 Magazine breaks down some critical parts of the sales stack. To up your sales game, read on!
The Hole Truth: Via Integrity in an HDI World
From the drilled hole to registration across multiple sequential lamination cycles, to the quality of your copper plating, via reliability in an HDI world is becoming an ever-greater challenge. This month we look at “The Hole Truth,” from creating the “perfect” via to how you can assure via quality and reliability, the first time, every time.
- Articles
- Columns
- Links
- Media kit
||| MENU - pcb007 Magazine
Estimated reading time: 6 minutes
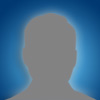
Contact Columnist Form
Material Witness: Tg, CTEZ and the Implications of So-Called Standard Testing
Material Witness by Chet Guiles
We've talked about glass transition temperature (Tg) and thermal expansion rates (CTE) previously, but there seems to be some confusion about how it is tested and what the results mean in practical terms. Tg and CTEZ are not simply numbers generated to fill a block in a data sheet. Nor are they the whole story in terms of the applicability of a material for its intended application. Other characteristics, such as material chemistry, thermal decomposition temperature (Td) and short-term heat exposure testing (T288, T300 etc.) are also elements of determining the total suitability of a product for manufacturing, assembly and end-use. Different methods of determining Tg (TMA, DSC, DMA) will give somewhat different numeric results and may serve to make a data sheet look a little better (or worse). But remember that the material is what it is because of its chemistry and composition, and while testing may be helpful in selecting materials, it does not ever, ever, ever tell the entire story. Typically, the manufacture and assembly processes are more demanding than the end-use condition because the devices mounted on most boards will fail before the board will in a pure high-temperature exposure. Equally, most PWBs in manufacturing, assembly and use will never see the temperatures at which rapid chemical decomposition will take place (unless you are using an old style IR reflow system and don't take care to adjust it for the unique radiation absorption characteristics of the material you are using). So what are the principal impacts of Tg and CTEZ in a laminate system?
- At or above the Tg, the CTEZ increases substantially. Due to increased molecular movement, the CTEZ is four to five times as great above the Tg as it is below. In a typical epoxy system, it might be that 60 ppm/°C below the Tg will translate to 250 ppm/°C or more above it. The principal impact of the Z-Direction expansion is that it strains the copper in a plated through hole. The greater the amount of laminate expansion relative to that of the copper itself, the greater the strain on the copper in the hole. If the PTH copper does not have sufficient elongation, or if by frequent thermal cycling the copper is "work hardened," it can develop cracks which will then grow over time as the temperature is cycled. And, once a crack is started, it can continue to propagate even though the expansion in-use will not be as great as it was during board manufacture and assembly. Small cracks (perhaps not even visible in cross-sections, or not found in every cross section) are considered "latent defects" that can come back while the board is in use as intermittent opens or unexpected increases in resistivity that can effect signal integrity. Remember that the closer the CTEZ is to that of Copper (about 17 ppm/°C) the less strain will be put on the plating in the hole and the less force (stress) will be applied that would tend to stretch, crack or work the copper in the hole barrel.
- Above the Tg, resins tend to be softer and can "smear" during drilling as drill bit temperatures exceed the Tg due to frictional heat buildup; or they may exhibit reduced peel strength resulting in pad-lifting.
Measurement of Z-Axis CTE, according to IPC-4101 is as follows:3.10.1.11 Z-Axis CTE: When specimens are tested in accordance with Table 3-1, the Z-Axis CTE shallmeet the values as specified on the purchase order or in the applicable specification sheet. Note: Test specimens shall be constructed such that their thickness will be 1.5-2.36 mm [0.0591-0.0929 in] thick and have a retained resin content of 40 to 45%.In consequence of this standardized testing requirement (which can only be reasonably met using heavyweight glass, such as styles 7628 or 7642, with low resin content) many materials are reported as having Z-axis expansion coefficients and total Z-direction movement that is materially lower (pun intended!) than the data sheet would suggest. In an application where PTH reliability is particularly critical due to the expectation of high-temp processing or severe environmental or use conditions, the expansion of a high resin content MLB will be considerably greater than that for an "IPC-4101" standard material test. In the chart below, we compare high Tg FR-4 (Tg~170°C) and two grades of polyimide both of which have Tg of 250°C, but one is a standard polyimide and the other is Arlon's EP2, enhanced ceramic-filled polyimide, with a CTEZ that is very close to the expansion coefficient of copper.As is obvious the total expansion of the materials is dependent both on Tg (the epoxy system starts expanding at a high rate at about 170°C while the polyimide materials start expanding at the higher rate at about 250°C) and the composition of the material. The filled system, having an inherently lower CTE both because of the volume of inorganic filler (which does not have a Tg) and the reduced resin content due to displacement by the filler as well as the glass, will produce substantially less strain on the copper. The result will be less expansion for any given thermal excursion, and a reduction in cracking even with lower ductility plating. With less potential for latent defects, the ultimate reliability of boards should be greatly enhanced.The following graph, from a paper by Knadle et. al. [1] indicates the dramatic effect of the practical impact of this: There is a dramatic increase in mean time to failure in the field when using higher Tg/lower Z-direction expansion materials. While this chart does not specifically address the difference in expansion between the material and the copper of the PTHs, the principle is clear and the effects are very real and repeatable.
This is not intended as a warning not to trust data sheets--for the most part, the data presented by all of us in the industry is intended to be accurate and to represent standard methodology where possible for comparison purposes. Just don't forget that standard test methods can result in an "apples to oranges" comparison if you do not understand the details behind the individual results and likely will not address what you will experience in actual boards made to your own design and using variations on materials that the standard methods do not anticipate.Until next time.
Reference:1. Kevin T. Knadle and Virendra R. Jadhav, "Proof is in the PTH -- Assuring Via Reliability from Chip Carriers to Thick Printed Wiring Boards," Endicott Interconnect Technologies, Inc., Paper presented at the 2005 Electronic Components and Technology Conference
Chet Guiles is a graduate of the University of New Haven with a BA in Chemistry (1971) and of the Syracuse University Eastern European languages Institute in Russian Language (1963, while on active duty with the USAF). Subsequent to his military service, Chet worked in the areas of corrosion metallurgy (Olin Metals Research), and PVC and silicone rubber technology (Automation Industries). Prior to joining Arlon in 1979, Chet worked as a Senior Research Chemist at Pennwalt Corporation performing research on PVC stabilization.At Arlon, Chet has served in a number of roles including Technical Manager for the Silicone Rubber Group in DE, Quality Assurance Manager for the Delaware Microwave Materials operation, Division Technical Director and, most recently, as Director of New Business Development for the Electronic Substrates Division. Retired in 2004, Chet now acts as a part-time consultant to Arlon.Chet has several U.S. patents and has written and published widely over the past 30 years in the area of materials for PCBs.
More Columns from Various Archived Columns
Slash Sheet Chaos: Is What You See, What You Get?Moisture in Materials: Avoiding Process Gremlins
Material Witness: Beat the Heat--A Non-Math Intro to Thermal Properties
Material Witness: Considerations in Using TC Materials for PWBs
Material Witness: Are Your Materials Up to the Challenge?
Material Witness: Thermal Oxidation of Materials, Part I
Material Witness: Thermal Oxidation of Materials, Part II
Material Witness: R.I.P. Speedboard C