-
- News
- Books
Featured Books
- pcb007 Magazine
Latest Issues
Current IssueInventing the Future with SEL
Two years after launching its state-of-the-art PCB facility, SEL shares lessons in vision, execution, and innovation, plus insights from industry icons and technology leaders shaping the future of PCB fabrication.
Sales: From Pitch to PO
From the first cold call to finally receiving that first purchase order, the July PCB007 Magazine breaks down some critical parts of the sales stack. To up your sales game, read on!
The Hole Truth: Via Integrity in an HDI World
From the drilled hole to registration across multiple sequential lamination cycles, to the quality of your copper plating, via reliability in an HDI world is becoming an ever-greater challenge. This month we look at “The Hole Truth,” from creating the “perfect” via to how you can assure via quality and reliability, the first time, every time.
- Articles
- Columns
- Links
- Media kit
||| MENU - pcb007 Magazine
Estimated reading time: 7 minutes
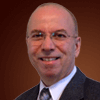
New Column: Bert's Practical Design Notes
Welcome to my new column, “Bert’s Practical Design Notes.” I am Lambert Simonovich, founder and president of Lamsim Enterprises Inc., but most everyone calls me Bert. It is a pleasure to be a part of PCBDesign007, and to be associated with such a distinguished list of fellow columnists.
From as far back as I can remember I was always interested in how things worked. I would often take things apart just to see what was inside; but not always successful in putting them back together again. I was always fascinated with electricity and electronics. At about 10 or 11 years old, I was mystified with how telephones worked. After reading about Alexander Graham Bell in a booklet published by The Bell Telephone Company of Canada, I became inspired to buy a pair of old push-to-talk handsets from a local army surplus store. I experimented with them using dry cell batteries and lamp cord wire. When I finally was able to get two-way communications, it seemed like magic. I knew right then what my career choice would be.
After graduating college as an electronic engineering technologist, I was fortunate enough to get a job at Bell Northern Research (BNR) in Ottawa. Back then, it was the research and development lab jointly owned by Bell Canada and Northern Electric (later becoming Northern Telecom, then finally Nortel). For me, this was the Mecca for high-technology in Canada, and I stayed there my entire career until I left in 2009 to start my own consulting business.
Over the years, I have held a variety of hardware design engineering positions and pioneered several advanced technologies into products. I learned many new skills along the way outside of my formal training. Eventually I ended up specializing in high-speed signal integrity and backplane architecture. I have been fortunate throughout my career to have been a part of and contribute to some of the technology that enables the gadgets we enjoy today. Along the way, I have met and worked with many smart and talented individuals who took the time to unselfishly share their knowledge and experience.
And now, after all this time, I still have the passion I had as kid to learn and understand new things. Except now, like cradling a fine glass of wine, I am able to slowly swirl it around, sip it and savor the taste. This column is about sharing some of that passion. It will cover a range of topics from signal integrity, PCBs, backplane design, circuit modeling, simulation tools and other practical engineering solutions. I hope you find them interesting and get inspired to further explore some of the subject matter on your own.
A Blast from the Past
But before I go, I would like to leave you with an example of the technology back in the day. I recently came across some souvenir pictures and artwork of work I had done early in my career.
For those of you who are old enough to remember, it will bring back some fond memories; and for you young designers, this is how we did things in the late ‘70s, early '80s.
Figure 1. Northern Telecom T1C line repeater circa 1980.
Figure 1 is a T1C line repeater I helped to design early in my career circa 1980. Line repeaters were used to regenerate digital signals along a span between two central offices. There were two regenerators per line repeater, and one repeater for every 4-pairs (2Tx, 2Rx) in the cable. They were housed in apparatus cases mounted on telephone poles or pedestals every mile or so. In the city they were usually installed in manhole vaults buried underground.
T1 digital transmission was introduced in 1961 as a way to replace older analog voice frequency technology, and is still in use today. T1 data rate is 1.544 Mb/s and carries 24 channels of DS0 at 64Kb/s. As digital technology exploded through the 1970s, it became more affordable, allowing T1 to become more popular. By the early 1980s, the installed base was reaching capacity especially in large cities, and the industry was looking for ways to increase its bandwidth.
Sound familiar? To address this issue, a new T1C standard was developed to double the bandwidth. T1C stands for T1-concatenated, and doubles the data rate to 3.152 Mb/s allowing it to carry 48 DS0 channels.
As part of the T1C project team, my primary responsibility was to package the design and layout the printed circuit board. Because of the limited real estate available and because through-hole component technology was the only choice for PCBs, we needed to use thick-film technology for the receiver equalization circuitry.
Thick-film technology was quite popular at the time, and was the predecessor to today’s surface mount technology on PCBs. It allowed for the miniaturization of circuitry by screen printing conductive traces and resistive ink onto a ceramic substrate, then firing it to a high temperature. Surface mount components were limited to capacitors, SOT transistors and diodes.
At the time, Northern Telecom (NT) had its own in-house thick-film design and manufacturing facility in Aylmer, Quebec. All of the thick-film designs used in NT’s products prior to the T1C project were single in-line packages (SIPs). Because of the height restriction and the amount of circuitry needed to be integrated onto the substrate, SIPs were impractical, so we had to develop dual in-line manufacturing capability at the same time we were developing the product.
The final dual in-line thick-film packages are shown near the faceplate. Since the packaging of the repeater was so dense, I needed to place components under the thick-film substrates. This was all well and good until I was testing a bunch of repeaters for a field trial in California coming up in December of that year. I accidentally dropped one and it happened to land flat with component side up. After I picked it up, I noticed both thick-film substrates were cracked. How could this be? There was enough clearance from the highest component underneath, and enough pins to support the ceramic substrate, so why did it break?
Fortunately, we had a state-of-the-art photography lab in the building with high-speed camera equipment. So we set up a controlled experiment to capture what went wrong. We built up some test samples and dropped them while capturing it all at high speed. Well, it wasn’t a fluke. Every one that we dropped and filmed showed the same result. It turns out there was enough flex in the long right-angle pins that the momentum of the substrate caused it to hit the radial capacitor underneath, then spring back as if nothing had ever happened. Under other circumstances, this would have been cool to see, but not when the project was in jeopardy.
To make a long story shorter, I eventually came up with an elegant solution for a plastic carrier that would support the substrate and keep it at a fixed height above the board. Not only did it solve the reliability problem, but it also solved the shipping and handling protective packaging issue for the thick-film assembly at the same time.
Figure 2. Example of double sided artwork for the T1C line repeater. Red is solder side, blue is component side.
Figure 2 shows the actual artwork for the repeater’s PCB. Back then, all our boards were double-sided and all layouts were done by hand: First in colored pencil, then using red/blue tape and pads on mylar film for final artwork. Red usually represented the solder (bottom) side of the board and blue was the component (top) side. The artwork was usually done at 2:1 scale and later photo reduced to produce the 1:1 photomasks. Red and blue filters were used during the photo reduction process to separate individual layer masks. A red filter generated the component side and blue filter produced the solder side photomasks respectively. All drilled holes were manually specified on a separate drawing with various symbols for the drill sizes. Line widths and space were typically 25 mils and components were on 100 mil pitch. All components were through-hole mounted on one side only and passed through a solder wave.
The entire T1C line repeater project – from inception through designing, testing, building 50 prototypes by hand and completing a successful field trial in California – took about six months. And this was with a team of three plus our manager, and mechanical design support staff. Finding these pictures truly was a blast from the past. Looking back, I sometimes wonder if we could have done it any faster with today’s modern technology, CAD tools and outsourcing business model.
What do you think?
Bert Simonovich was born in Hamilton, ON, Canada. He received his Electronic Engineering Technology diploma from Mohawk College of Applied Arts and Technology, Hamilton, ON, Canada in 1976. Over a 32-year career, working as an Electronic Engineering Technologist at Bell Northern Research and later Nortel, in Ottawa, Bert helped pioneer several advanced technology solutions into products. He has held a variety of engineering, research and development positions, eventually specializing in signal integrity and backplane architecture for the last 10 years. He is the founder of Lamsim Enterprises Inc., where he continues to provide innovative signal integrity and backplane solutions to clients as a consultant. With three patent applications and two patent grants to his name, Bert has also (co)authored several publications, including an award-winning DesignCon2009 paper related to PCB via modeling. His current research interests include signal integrity, high-speed characterization, and modeling of high-speed serial links associated with backplane interconnects. To contact Bert, click here.
More Columns from Bert's Practical Design Notes
Practical Modeling of High-Speed Backplane ChannelsObsessing over Conductor Surface Roughness: What’s the Effect on Dk?
The PDN Bandini Mountain and Other Things I Didn’t Know I Didn’t Know
Bert's Practical Design Notes: Accelerating the SI Learning Curve - Bogatin's SI Academy
Bert's Practical Design Notes: Are Guard Traces Worth It?
Bert's Practical Design Notes: Perils of Lumped Via Modeling
Bert's Practical Design Notes: The "Stubinator" vs. Back-Drilling
Backplane High-Level Design: The Secret to Success